miniature inductive proximity sensor
- time:2025-07-02 03:07:04
- Click:0
The Mighty Miniature: How Tiny Inductive Proximity Sensors Are Revolutionizing Automation
In the intricate dance of modern machinery, machines need to “see” without eyes and “feel” without touch. This crucial non-contact sensing capability, especially for detecting metal objects in demanding, space-constrained environments, is where the unassuming hero – the miniature inductive proximity sensor – shines. Compact, robust, and remarkably precise, these tiny titans are driving innovation across countless industries.
Understanding the Core Technology
Before diving into their miniature marvels, let’s grasp the fundamental principle. An inductive proximity sensor operates by generating an oscillating electromagnetic field via a copper coil wrapped around a ferrite core. When a metallic target enters this field, it induces tiny circulating electrical currents within the metal itself – known as Eddy currents. These Eddy currents draw energy from the sensor’s field, causing a measurable change in the oscillation amplitude or frequency. The sensor’s electronics detect this change and trigger an output signal (e.g., switching a relay or sending a signal to a PLC), indicating the presence of the object without any physical contact.
The “miniature” designation signifies drastic size reduction while retaining core functionality. Moving beyond standard M18 or M30 threaded barrels, miniature inductive sensors often boast housings as small as M5, M8, or even specialized rectangular or block styles only millimeters thick. This extreme compactness is key to their revolutionary impact.
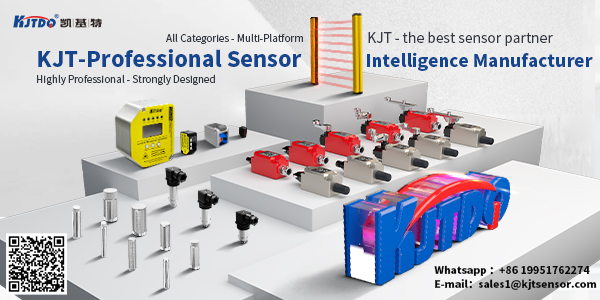
The Power of Size: Advantages Amplified
Why does making them smaller matter so much? The benefits are significant and multifaceted:
- Unlocking Confined Spaces: This is the most obvious and critical advantage. Miniature inductive proximity sensors can be installed in locations where larger sensors simply wouldn’t fit. Think inside intricate robotic gripper assemblies, within compact medical devices, along densely packed PCB assembly lines, or embedded into lightweight automated guided vehicles (AGVs) and collaborative robots (cobots) where every gram and cubic centimeter counts.
- Lightweight Integration: Reduced size inherently means reduced weight. This is vital for applications on moving parts, articulated robot arms, or anywhere minimizing inertial load enhances precision, speed, and energy efficiency.
- Enhanced Precision and Density: Their small footprint allows designers to place multiple sensors very close together. This enables high-resolution position feedback, multi-point detection on small components, or complex presence verification schemes within a tiny area.
- Reduced Material Costs & Installation Flexibility: Less material is used in manufacturing smaller sensors. Furthermore, their diminutive size often requires smaller mounting holes and less invasive installation, potentially simplifying machinery design and reducing overall system cost.
- Maintaining Core Strengths: Crucially, modern miniature inductive proximity sensors haven’t significantly sacrificed the inherent benefits of their larger counterparts. They typically offer:
- High Reliability: No moving parts and sealed designs (often IP67/68 rated or higher) ensure long life in harsh industrial environments (dust, oil, coolants).
- Fast Switching Speeds: Capable of detecting objects moving at high velocities, essential for modern high-speed automation.
- Non-Contact Operation: Eliminates wear and tear on both sensor and target, ensuring consistent performance over time.
- Metal-Only Detection: Immune to dust, smoke, water (unless affecting the housing seal), and non-metallic objects, providing precise targeting.
Applications: Where Miniature Makes the Difference
The unique advantages of miniature inductive proximity sensors make them indispensable across diverse sectors:
- Robotics & Cobots: Essential for end-of-arm tooling (EOAT), detecting gripper closure, verifying part presence in confined grippers, and ensuring safe human-robot collaboration space monitoring on compact joints.
- Semiconductor & Electronics Manufacturing: Detecting micro-components on PCBs, verifying wafer handling positions within delicate processing equipment, and ensuring precision placement in SMT machines where space is ultra-premium.
- Medical Device Manufacturing & Automation: Used within life-saving devices like surgical robots, infusion pumps, and diagnostic equipment for precise part detection and positioning verification in sterile, compact environments.
- Packaging Machinery: Monitoring small parts counts, verifying cap or seal presence on vials and bottles, and ensuring the correct operation of micro-actuators within increasingly smaller packaging systems.
- Automotive Manufacturing: Position sensing in tight engine compartments, detecting gear positions in compact transmissions, and verifying assembly steps on intricate sub-components.
- Material Handling (Miniaturized): Monitoring conveyors handling small items, detecting pallet position on compact AGVs, and managing inventory on micro-scale storage and retrieval systems.
Selecting the Right Miniature Sensor: Key Considerations
Choosing the optimal miniature inductive proximity sensor involves several factors beyond just size:
- Sensing Distance: Miniaturization often means shorter nominal sensing ranges (Sn). While impressive ranges exist for small sizes (e.g., 1.5-3mm for M5/M8), ensure the range meets the application’s physical constraints and detection needs.
- Housing Material & Shape: Options include rugged stainless steel, chemically resistant nickel-plated brass, PBT plastic, or specialized rectangular/flat-pack designs. Choose based on environmental exposure (temperature, chemicals) and mounting constraints.
- Output Configuration: Standard DC output choices are NPN or PNP transistor switching (sourcing/sinking). Ensure compatibility with your control system’s input type. Advanced miniature models increasingly feature IO-Link for digital communication, diagnostics, and configuration flexibility.
- Electrical Connection: Common choices are fixed cable (varying lengths), compact M5, M8, or M12 connectors. Consider ease of installation and serviceability.
- Shielding/Non-Shielding: Shielded sensors allow flush mounting in metal, crucial for tight spaces. Non-shielded offer slightly longer ranges but require an unobstructed side area.
The Future is Small and Smart
The trend towards miniaturization shows no sign of slowing down. We are already seeing sub-M5 sensors and specialized form factors pushing the boundaries of how small inductive sensing can get. Concurrently, the integration of IO-Link technology into miniature inductive proximity sensors is a game-changer, providing richer diagnostic data (temperature, signal strength), remote configuration, and seamless integration into Industry 4.0 architectures – all without increasing physical size. This combination of extreme compactness, high functionality, and intelligence ensures miniature inductive proximity sensors will remain vital components in designing the smarter, leaner, and more efficient machines of tomorrow. Their ability to solve complex detection challenges within the tiniest footprints makes them truly mighty components in the modern automation landscape.