schneider proximity sensor
- time:2025-07-02 02:55:01
- Click:0
The Silent Guardian: Schneider Proximity Sensors Powering Industrial Efficiency
In the hum and thrum of a modern factory floor, amidst towering machinery and precise robotic arms, many critical operations happen without direct human touch. Vital components move, align, and process materials with astonishing speed and accuracy. Yet, ensuring this intricate dance runs smoothly relies heavily on unseen sentinels – devices that detect presence or absence without physical contact. Schneider Electric proximity sensors stand as quintessential examples of this technology, silently safeguarding operations and enabling relentless industrial productivity.
Understanding the Core: What Are Proximity Sensors?
At their essence, proximity sensors are non-contact detection devices. They emit an electromagnetic field or beam (using inductance, capacitance, ultrasonic, or photoelectric principles) and sense changes caused by a target object entering their detection zone. Crucially, they do not require physical touch, making them ideal for harsh environments, high-speed operations, or where targets could be damaged. Schneider’s portfolio primarily focuses on inductive sensors (detecting metallic objects) and capacitive sensors (detecting both metallic and non-metallic objects like liquids or plastics). This core technology forms the bedrock of countless automated processes.
Schneider Proximity Sensors: Precision Engineered for Reliability
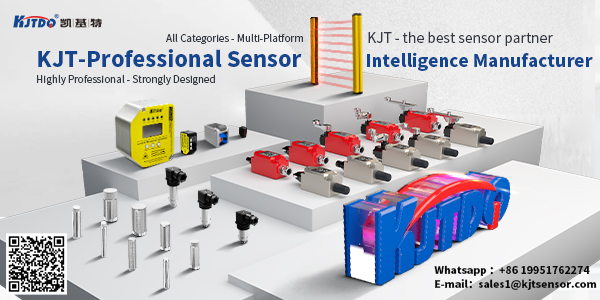
What sets Schneider sensors apart in a crowded market? It’s a blend of robust engineering, unwavering reliability, and seamless integration into broader industrial ecosystems.
- Exceptional Durability: Engineered for the rigors of industrial life, they withstand extreme temperatures, humidity, shock, vibration, and exposure to oils, coolants, and chemicals. Many boast IP67, IP68, or IP69K ratings, offering superior protection against dust and water ingress. This resilience directly translates to minimized downtime and reduced maintenance costs.
- Uncompromising Accuracy: Schneider sensors offer precise and repeatable detection, critical for positioning tasks, counting operations, and safety interlocks. Their designs minimize interference from ambient conditions or nearby metallic objects, ensuring consistent, trustworthy performance.
- Diverse Range & Specialized Solutions: Schneider doesn’t offer a one-size-fits-all product. Their extensive range includes:
- Tubular sensors in varied sizes (M8, M12, M18, M30) for standard applications.
- Rectangular/flat sensors (XS series) for space-constrained installations.
- High-temperature sensors for demanding environments like foundries.
- Factor 1 sensors detecting any metal at the same range.
- Analog sensors providing continuous distance measurement.
- IO-Link enabled sensors, offering advanced diagnostics, parameterization, and integration into Industry 4.0 networks.
- Seamless Integration: Designed with ease of installation and connection in mind, Schneider sensors often feature standardized M12/M8 connectors and simple mounting options. Their compatibility with Schneider’s wider TeSys™ and Modicon™ ecosystems allows for efficient system design, commissioning, and management.
Where They Shine: Key Industrial Applications
The versatility of Schneider proximity sensors makes them indispensable across virtually every manufacturing and processing sector:
- Manufacturing & Assembly: Detecting part presence/absence on conveyors, verifying component insertion, controlling robotic arm positions, and ensuring proper jig/clamp closure. Precision is paramount here.
- Material Handling & Packaging: Monitoring package position on fillers, cappers, and labelers; detecting bottles/cans on conveyors; counting items; and verifying case sealing. The ability to detect diverse materials (metallic and non-metallic) is crucial.
- Automotive: Used extensively in welding lines (detecting weld nuts, studs), paint shops (positioning bodies), assembly stations (verifying component fitment), and engine assembly. Durability against harsh chemicals is essential.
- Food & Beverage: Hygienic designs suitable for washdown environments monitor ingredient levels in silos, detect containers on filling lines, and control valve positions. Sanitary standards compliance (IP69K) is non-negotiable.
- Machinery & Equipment: Providing position feedback on hydraulic cylinders, controlling safety gates, monitoring tool changers, and detecting end-of-travel positions. Reliability prevents costly machinery damage.
Choosing the Right Schneider Sensor: Key Considerations
Selecting the optimal sensor involves evaluating several factors:
- Target Material: Metal (inductive) or almost anything (capacitive/mixed)?
- Required Sensing Distance: What range is needed? Schneider sensors specify nominal and assured operating distances.
- Environment: Exposure to temperature extremes, chemicals, washdown (IP rating needed), or strong EMI?
- Mounting: Space constraints? Flush or non-flush mounting required?
- Electrical Output: NPN/PNP transistor, NO/NC contacts, or analog output? Voltage requirements (10-30V DC typical)?
- Special Needs: IO-Link for smart diagnostics/data? Analog output for position? High-temperature tolerance? Factor 1 capability? Consulting Schneider’s detailed datasheets is crucial.
- Safety: For safety-related functions (e.g., gate monitoring), ensure selection of dedicated safety-rated sensors (like the XPS safety range) designed with redundancy and monitored outputs.
Beyond Detection: The Value Proposition of Schneider Sensors
While the primary function is detection, the true value of Schneider proximity sensors lies in what they enable:
- Enhanced Productivity: Reliable detection ensures smooth, uninterrupted operation of machinery and processes.
- Improved Quality Control: Consistent positioning and verification prevent errors and product defects.
- Reduced Operating Costs: Durable designs minimize replacement frequency and maintenance downtime. Early fault detection via IO-Link diagnostics prevents larger failures.
- Increased Safety: Ensuring guards are closed, tools are retracted, or personnel are clear of danger zones.
- Foundation for Automation & IIoT: As reliable data points, they form the bedrock of automated control systems and feed valuable data into Industrial Internet of Things (IIoT) platforms for optimization.
Conclusion: An Indispensable Component of Modern Industry
From the minute detection of a tiny screw to safeguarding large machinery movements, Schneider Electric proximity sensors perform their vital roles reliably, day in and day out. Their blend of ruggedness, precision, and adaptability makes them far more than just simple switches; they are fundamental enablers of efficiency, safety, and intelligent manufacturing. By understanding their capabilities and carefully selecting the right sensor for the job, engineers and technicians leverage Schneider’s engineering excellence to build more robust, productive, and future-proof industrial processes.