12v proximity sensor
- time:2025-07-02 02:49:00
- Click:0
Unlock Efficiency with 12V Proximity Sensors: Your Key to Non-Contact Detection
Imagine a world where machines respond before touch, where production lines hum with uninterrupted precision, and where harsh environments pose no threat to critical sensing operations. This isn’t science fiction; it’s the everyday reality enabled by the 12V proximity sensor. These robust, versatile components are fundamental to modern automation, offering reliable, non-contact detection across countless industries. Understanding their capabilities and why the 12V DC power supply is so prevalent unlocks significant advantages for engineers and system designers.
What Exactly is a 12V Proximity Sensor?
At its core, a proximity sensor detects the presence or absence of an object without requiring physical contact. A 12V proximity sensor specifically operates on a 12V DC power supply, making it compatible with a vast range of industrial control systems, vehicle electronics, and machinery. When an object enters its detection field, the sensor’s internal state changes (e.g., a solid-state switch opens or closes), sending a clean electrical signal to a controller like a PLC.
- Primary Function: Detect metallic or non-metallic targets (depending on type) within a specified range.
- Key Characteristic: Operates on a 12V DC power source.
- Output: Typically provides a switching signal (PNP/NPN transistor, NO/NC).
Why 12V? The Voltage Advantage
The widespread adoption of 12V DC for proximity sensors isn’t arbitrary. It offers crucial benefits:
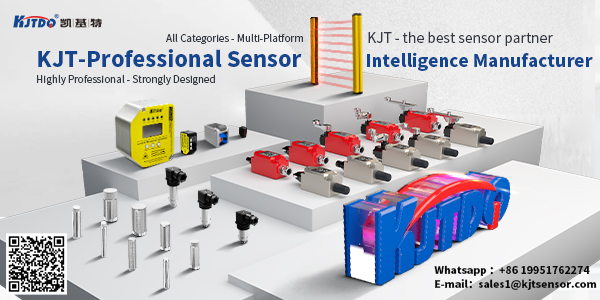
- Ubiquity & Compatibility: 12V DC is one of the most common voltage levels found in industrial control panels, automotive applications, material handling equipment, and conveyor systems. Using 12V sensors simplifies integration, eliminating the need for additional voltage converters in many setups.
- Safety & Practicality: Compared to higher voltages (like 24V or 120VAC), 12V DC represents a safer low-voltage level. This reduces risks during installation, maintenance, and troubleshooting, especially in potentially hazardous environments. It often falls under lower safety certification requirements.
- Sufficient Power & Stability: 12V provides ample power for reliable sensor operation, including driving the internal oscillator and output switching circuitry, while maintaining good signal integrity over reasonable cable lengths. It balances power needs with energy efficiency.
- Robustness Against Voltage Fluctuations: Industrial power supplies can experience minor fluctuations. A 12V DC sensor typically has a wide operating voltage range (e.g., 10-30V DC). This means it continues functioning reliably even if the input voltage dips slightly below or rises above the nominal 12V, enhancing system resilience.
Core Mechanism: How Do They “Sense”?
While various technologies exist (capacitive, ultrasonic, photoelectric), the most common type of 12V proximity sensor is the inductive sensor. Here’s a simplified look at its operation:
- Oscillator Circuit: Inside the sensor, an oscillator generates a high-frequency alternating magnetic field emanating from the sensor’s active face.
- Target Interaction: When a conductive metal target (ferrous or non-ferrous like aluminum, brass, copper) enters this field, eddy currents are induced on the target’s surface.
- Damping Effect: These eddy currents draw energy from the oscillator circuit, causing a detectable reduction (damping) in the oscillation amplitude.
- Signal Processing & Output: The sensor’s internal circuitry monitors this amplitude change. When the damping exceeds a preset threshold (indicating the target is within the nominal sensing range), the sensor triggers its output switch – turning it ON or OFF depending on its configuration (Normally Open or Normally Closed).
- Clean Control Signal: This change in the sensor’s output state (e.g., switching the 12V DC line) provides a clear signal to the PLC or controller about the target’s presence.
Where 12V Proximity Sensors Shine: Key Applications
Their reliability, speed, and non-contact nature make 12V proximity sensors indispensable in diverse settings:
- Automated Manufacturing: Detecting parts on conveyors, confirming robot end-of-arm tooling position, verifying fixture clamping, monitoring spindle position on CNC machines, counting products. Boosts throughput and minimizes downtime.
- Packaging Machinery: Verifying bottle/cap presence, controlling fill levels (via presence detection), detecting labels, monitoring film feed, ensuring case sealing. Ensures consistent packaging quality.
- Material Handling: Detecting pallets on lifts, confirming the position of AGVs (Automated Guided Vehicles), monitoring conveyor belt movement, sensing bin levels. Optimizes logistics flow.
- Automotive: Position sensing in engines (camshaft, crankshaft), transmission control, detecting door/hatch open/closed status, seat position sensing. Critical for vehicle control and safety systems.
- Machine Safety: Used as part of safety circuits to confirm machine guards are closed before operation commences (safety-rated sensors required).
- General Machinery: Position feedback for cylinders (end-of-stroke detection), detecting tool breaks, monitoring rotational speed.
The Power of Non-Contact Detection
This fundamental characteristic delivers game-changing advantages:
- Zero Physical Wear: Without moving parts contacting targets, the sensor experiences virtually no mechanical wear, leading to exceptionally long service life and reduced maintenance.
- High Reliability: Fewer failure modes compared to mechanical limit switches. Immune to issues like sticking, bouncing contacts, or target adhesion.
- Blazing Speed: Detection happens electronically at high frequencies, enabling use in very fast processes where mechanical switches are too slow.
- Harsh Environment Tolerance: Sealed designs (rated IP67, IP68, IP69K) withstand dust, dirt, moisture, oils, coolants, and high-pressure washdowns – common challenges in industrial settings.
- Consistent Performance: Provides reliable detection of metallic objects regardless of surface finish (oily, dirty, painted), unlike some optical sensors.
Selecting the Right 12V Proximity Sensor: Key Considerations
Choosing the optimal sensor involves understanding your specific needs:
- Sensing Distance (Sn): The nominal distance the sensor can reliably detect a standard target. Ensure it’s sufficient for your application, considering mounting and target movement paths. Don’t confuse this with the often larger maximum distance.
- Target Material & Size: Inductive sensors require metallic targets. Specify if ferrous steel, non-ferrous (aluminum, brass, copper), or stainless steel is needed, as sensing distance reduces for non-ferrous metals. Target size also impacts effective sensing range.
- Output Type & Wiring:
- PNP (Sourcing): Outputs positive voltage (12V) when active. Common in Europe/Asia.
- NPN (Sinking): Outputs ground (0V) when active. Common in North America.
- NO (Normally Open)/NC (Normally Closed): Defines the output state when no target is present.
- 3-wire vs 2-wire: 3-wire is most common for digital outputs. 2-wire sensors act like a switch in series with the load but may have a small leakage current.
- Housing Material & Shape: Cylindrical (threaded barrels) are common, but rectangular “block” styles exist. Materials range from nickel-plated brass or stainless steel for durability to specialized plastics.
- Environmental Protection (IP Rating): Essential for longevity. IP67 (dust-tight, immersion to 1m), IP68 (continuous immersion), and IP69K (high-pressure/steam cleaning) are critical ratings for industrial use.
- Operating Temperature Range: Ensure the sensor can handle your ambient temperature extremes.
Embracing Reliability and Versatility
The 12V proximity sensor is far more than just a simple switch. It’s a sophisticated, rugged component that forms the bedrock of reliable automation. Its non-contact sensing principle ensures longevity and consistency, while its widespread 12V DC compatibility makes it incredibly easy to integrate into existing