m30 proximity sensor
- time:2025-07-02 01:36:41
- Click:0
M30 Proximitive Proximity Sensor: The Unsung Hero of Reliable Detection in Industrial Automation
Imagine a critical packaging line suddenly grinding to a halt. Bottles are colliding, product spills, and costly downtime accumulates. The culprit? An unreliable sensor failed to detect a passing component accurately. This scenario underscores the vital, often overlooked role sensors play in industrial efficiency. Among the workhorses keeping processes running smoothly stands the M30 inductive proximity sensor – a compact, robust solution trusted globally for consistent object detection without physical contact. Its specific size designation, M30, refers directly to its 18mm threaded barrel diameter, making it instantly recognizable and widely applicable across diverse industrial landscapes.
Understanding the M30 Proximity Sensor
At its core, an M30 proximity sensor is a type of non-contact detection device. Operating on the principle of electromagnetic induction, it generates an oscillating high-frequency electromagnetic field from its sensing face. When a metallic target (the object to be detected) enters this field, eddy currents are induced within the target. These currents cause a measurable change in the sensor’s own oscillation amplitude or frequency. This change is detected by the sensor’s internal circuitry, triggering an output signal – typically a solid-state switch (PNP or NPN transistor) – indicating the presence of the target. This entire process happens without any physical touch, eliminating wear and tear and enabling high-speed detection.
Why the M30 Form Factor Reigns Supreme
The M30 designation isn’t arbitrary; it signifies a specific physical size perfectly balanced for industrial needs:
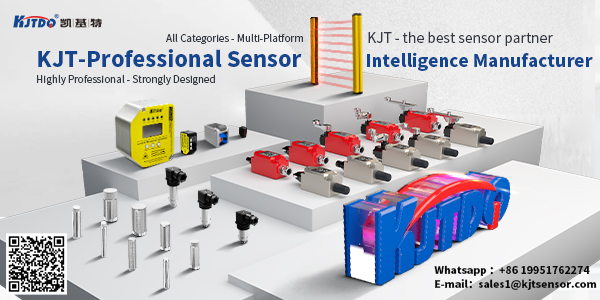
- Optimal Size and Sensing Distance: The 30mm body diameter provides ample space for the necessary electronics and coil while remaining compact enough for installation in tight spaces. M30 sensors frequently offer generous sensing ranges, often up to 15mm or even 20mm for ferrous metals, providing a crucial buffer for reliable detection.
- Robustness and Durability: Industrial environments are harsh. M30 sensors are typically housed in robust materials like nickel-plated brass, stainless steel (V2A, V4A), or rugged plastics. This construction grants them exceptional resistance to impacts, vibration, and harsh chemicals. Crucially, they boast high Ingress Protection (IP) ratings like IP67 or IP69K. This means they are dust-tight (IP6x) and can withstand immersion in water (IPx7) or high-pressure, high-temperature washdowns (IPx9K), making them ideal for demanding sectors like food and beverage or chemicals.
- Mounting Simplicity and Standardization: The ubiquitous M30 x 1.5 standard thread allows for quick and secure installation. They simply screw into a pre-tapped hole or a matching mounting bracket (often called a “saddle clamp” or “bracket mount”). This standardization ensures easy replacement and compatibility across manufacturers.
- Versatility in Outputs and Configurations: M30 sensors come in various configurations:
- NO (Normally Open) / NC (Normally Closed): Defines the output state when no target is present.
- 3-Wire DC: The most common type, offering PNP (sourcing) or NPN (sinking) transistor outputs, compatible with most Programmable Logic Controllers (PLCs).
- Analog Output (less common): Provides a continuous signal proportional to the target distance.
- Flush or Non-Flush Mountable: Flush-mountable types can be embedded in metal without affecting performance, while non-flush types offer longer sensing ranges but require surrounding clearance.
Key Advantages Driving Adoption
M30 proximity sensors deliver tangible benefits that contribute directly to operational efficiency and cost savings:
- Exceptional Reliability: Their non-contact nature inherently provides a long operational life, free from mechanical wear associated with mechanical switches. Solid-state electronics ensure millions of reliable switching cycles.
- High-Speed Operation: Capable of detecting objects moving at high speeds, making them perfect for high-speed counting and position verification applications on conveyor belts or rotating machinery.
- Resilience in Tough Conditions: As highlighted, their robust housing and high IP ratings allow them to perform reliably in environments with oil, coolant, dust, moisture, and significant vibration found in manufacturing plants, foundries, and outdoor applications.
- Immunity to Environmental Factors: Unlike optical sensors, they are largely unaffected by ambient light, dirt (non-metallic), smoke, or steam (within reason), ensuring stable performance where optics might fail.
- Cost-Effectiveness: While initial investment varies, their durability, minimal maintenance needs, and prevention of costly downtime make them a highly economical choice over the long term.
Critical Applications Across Industries
The reliability and versatility of M30 proximity sensors make them indispensable in countless scenarios:
- Machine Building: Position sensing of cylinders, end-of-travel detection, part presence/absence verification on assembly lines, rotational speed monitoring.
- Material Handling & Packaging: Detecting products on conveyors, confirming box flap closure, verifying pallet presence, controlling filling levels (via target position).
- Automotive Manufacturing: Ensuring robot tooling is correctly positioned, verifying part seating in fixtures, monitoring component feeds.
- Food & Beverage / Pharmaceutical:Stainless steel (V4A/316L) variants are essential for hygiene-critical zones, detecting cans, bottles, caps, and verifying machine component positions during washdown cycles.
- Metalworking: Tool breakage detection, stock feeding control, spindle orientation, monitoring coolant flow (using a metallic float).
- Conveyor Systems: Jam detection, counting objects, divert gate actuation, speed synchronization.
Selecting the Right M30 Proximity Sensor
Choosing the optimal sensor involves considering several factors:
- Target Material: Standard models detect ferrous metals (steel, iron) best. For reliable detection of non-ferrous metals (aluminum, brass, copper) or even stainless steel, look for models specifically designed as “non-ferrous metal detectors” or featuring all-metal detection capabilities.
- Sensing Distance: Select a sensor with a nominal sensing distance (Sn) greater than the maximum required installation distance to ensure reliable operation despite tolerances and potential misalignment. Account for the target material’s influence (sensing distance reduces for non-ferrous metals).
- Output Type & Wiring: Ensure compatibility with your control system (PLC input type). Choose between PNP (typically sourcing +24V) or NNP (sinking to 0V). Verify the voltage rating (commonly 10-30V DC).
- Housing Material: Choose nickel-plated brass for general use, stainless steel (V2A/304 or V4A/316L) for corrosion resistance or washdown environments.
- Electrical Connection: Options include axial cable, fixed connector (M8, M12 plug), or quick-disconnect versions.
- Special Features: Consider shielded (flush-mountable) vs unshielded (non-flush mountable, longer range), high-temperature variants, or models with IO-Link capability for smart diagnostics and parameterization.
Installation and Maintenance Best Practices
Proper installation ensures peak performance:
- Ensure adequate clearance around the sensing face (especially critical for non-flush mountable models).
- Mount securely to minimize vibration effects.
- Follow manufacturer wiring diagrams precisely.
- Keep the sensing face clean of excessive metallic debris buildup (though generally resistant to light dirt).
- While maintenance is minimal, periodically verify operation as part of a preventative maintenance routine. Many modern sensors featuring LED status indicators simplify diagnostics.
From intricate robotics to rugged conveyor belts packing products for global shipment, the M30 proximity sensor operates silently and reliably in the background. Its standardized size, robust construction, immunity to harsh conditions, and proven detection technology make it a cornerstone of modern industrial automation. Understanding its capabilities and selecting the correct variant ensures machines run smoothly, production targets are met, and costly unplanned downtime becomes