hall effect proximity sensor
- time:2025-07-02 01:30:39
- Click:0
Hall Effect Proximity Sensors: The Silent Guardians of Contactless Detection
Imagine machines that sense nearby objects without ever touching them – detecting position, counting rotations, or triggering actions with silent, unwavering precision. This isn’t science fiction; it’s the everyday reality powered by Hall effect proximity sensors. In our increasingly automated world, where seamless, reliable operation is paramount, these versatile devices have become indispensable components. But how exactly do they work their magic, and why are they the go-to choice for demanding applications? Let’s delve into the magnetism and ingenuity behind these silent sentinels.
The Core Principle: Harnessing the Hall Effect
The foundation lies in the Hall effect, a fundamental physical phenomenon discovered by Edwin Hall in 1879. It describes what happens when a conductor or semiconductor carrying an electrical current is exposed to a perpendicular magnetic field. The moving charge carriers within the material experience a force (known as the Lorentz force), causing them to deflect to one side. This deflection creates a measurable voltage difference – the Hall voltage – across the material, perpendicular to both the current flow and the magnetic field direction.
A Hall effect proximity sensor leverages this principle. It essentially consists of:
- A Hall Effect Element: A thin piece of semiconductor material (like doped silicon or gallium arsenide).
- Supporting Electronics: Integrated circuitry to amplify the tiny Hall voltage, condition the signal, and provide a clean, usable output (digital ON/OFF or analog signal proportional to field strength).
- A Protective Package: Housed to shield sensitive components from environmental factors.
How Does it Sense Proximity?
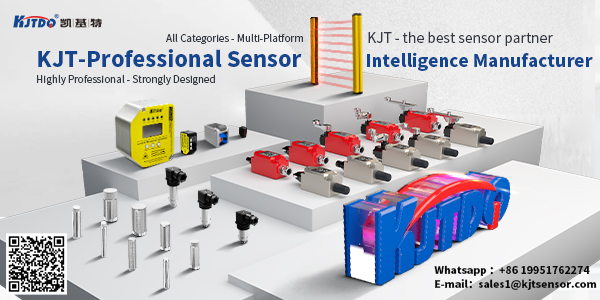
Unlike sensors relying on light or physical contact, a Hall effect sensor detects the presence, absence, or strength of a magnetic field. Proximity detection is achieved by associating the target object with a magnet. Here’s the sequence:
- Magnet Placement: A permanent magnet is mounted on (or embedded within) the object whose position or proximity needs detecting.
- Sensor Positioning: The Hall effect proximity sensor is fixed strategically relative to the expected path of the magnet.
- Detection Event: As the magnet approaches the sensor, its magnetic field permeates the Hall element within the sensor.
- Voltage Generation: The magnetic field causes the generation of the Hall voltage.
- Signal Processing: The sensor’s internal electronics detect this voltage change. Once the field strength exceeds a predefined threshold (or drops below it, depending on configuration), the sensor triggers its output signal.
- Output Switch: The output typically changes state – switching from High to Low (or vice versa), signaling the presence or proximity of the target.
Why Choose Hall Effect Sensors? Unrivaled Advantages
Hall effect proximity sensors are the preferred choice in countless industrial and consumer applications due to their unique set of advantages:
- Truly Contactless and Wear-Free: No physical contact occurs between the sensor and the target magnet. This eliminates mechanical wear, drastically extending operational lifespan and reducing maintenance costs. They simply don’t wear out from the sensing action itself.
- Immunity to Environmental Challenges: Unlike optical sensors that can be blinded by dust, dirt, oil, or fog, Hall sensors function remarkably well in harsh environments. They are unaffected by non-magnetic contaminants, moisture (provided sealing is adequate), vibrations, and offer excellent resistance to shock. Their performance also remains stable across a wide range of operating temperatures.
- High Speed and Reliability: Capable of detecting objects at high speeds (kHz range) due to the solid-state nature of the sensing principle. They provide highly repeatable and reliable switching, crucial for precision applications like motor control or speed sensing.
- Solid-State Robustness: With no moving parts inherent to the sensing mechanism, they are incredibly robust and resistant to mechanical failure.
- Position Flexibility: Can detect position not just linearly (front-facing), but also laterally (sensing the side of the magnet passing by) or even rotationally (used in rotary encoders), offering significant design flexibility.
- Electrical Noise Resistance: Generally exhibit good immunity to common industrial electrical noise, providing stable signals.
- Long Sensing Ranges (for Magnetic Prox): While not directly comparable to inductive or capacitive sensors detecting metal/any material, Hall sensors typically offer longer sensing distances relative to the size of the magnet used, compared to other sensing principles when specific target types are required.
Where Do They Shine? Key Applications
The robustness, reliability, and contactless operation of Hall effect proximity sensors make them ideal for demanding scenarios:
- Industrial Automation: End-of-travel detection on actuators, cylinder position feedback, conveyor belt object counting (object detection), machine tool positioning.
- Brushless DC (BLDC) Motor Control: Crucial for detecting rotor position (via magnets on the rotor) to electronically commutate the motor phases efficiently (motor control).
- Automotive Systems: Gearbox speed sensing (speed measurement), crankshaft/camshaft position sensing (position detection), seatbelt buckle detection, brake pedal position, window/mirror limit stops, anti-lock braking systems (ABS) wheel speed sensing.
- Consumer Electronics: Lid/door open/close detection in laptops and appliances (e.g., washing machine doors), smartphone flip covers, rotary encoder knobs.
- Fluid Level Sensing: Detecting the position of a magnetic float in tanks for level detection.
- Safety Interlocks: Ensuring guards or doors are closed before machinery starts.
- Speed Measurement: Counting gear teeth or magnetic markers on rotating shafts.
Selecting the Right Sensor: Key Considerations
Choosing the optimal Hall effect proximity sensor involves several factors:
- Output Type:
- Digital (Switch): Most common. Provides a simple ON/OFF signal when the magnetic field threshold is crossed. Includes choices like Open Collector (NPN or PNP) or Push-Pull outputs.
- Analog (Linear): Outputs a voltage proportional to the detected magnetic field strength, useful for position detection over a range or precise magnetic field sensing.
- Operating Voltage Range: Ensure compatibility with your system’s power supply.
- Sensitivity: Determines the magnetic field strength required to trigger the output. Higher sensitivity allows the use of smaller/weaker magnets or longer sensing distances.
- Switching Behavior (Unipolar/Bipolar/Latch): Defines how the sensor responds to magnetic field polarity and whether it requires an opposite field to reset:
- Unipolar: Responds to one magnetic pole (e.g., South pole approaching).
- Bipolar: Responds to both poles (North or South).
- Bipolar Latch: Requires one pole to switch ON and the opposite pole to switch OFF.
- Sensing Distance: The maximum distance at which a specific magnet will reliably trigger the sensor. Determined by sensor sensitivity and magnet strength/size. Always consult sensor/magnet datasheets.
- Temperature Range: Ensure the sensor is rated for the environmental operating temperatures it will experience.
- Package and Mounting: Physical size, shape, mounting options (threaded barrel, flat-pack SMD), and environmental protection (IP rating) are crucial for integration.
- Magnet Choice: The magnet type, size, shape, grade (strength), and orientation relative to the sensor critically impacts performance and sensing distance.
The Unseen Engine of Modern Precision
Hall effect proximity sensors, operating silently on the principles of physics discovered over a century ago, are fundamental enablers of modern technology. Their unique blend of contactless operation, robustness in harsh environments, high-speed capability,