ifm m12 proximity sensor
- time:2025-07-02 00:48:25
- Click:0
ifm M12 Proximity Sensors: The Compact Powerhouse Revolutionizing Industrial Detection
Imagine stopping machine downtime before it happens. Picture a production line humming along flawlessly, where components are reliably detected, positions are accurately monitored, and collisions are prevented – all thanks to a small, unassuming component. This is the reality enabled by sophisticated proximity sensors, and among the most trusted names in rugged industrial environments is ifm. Specifically, the ifm M12 proximity sensor range stands as a testament to German engineering excellence, offering unparalleled reliability, versatility, and performance in challenging applications. Whether you’re an OEM designing new machinery or a plant manager optimizing an existing line, understanding the power packed into these compact sensors is crucial for maximizing uptime and efficiency.
Proximity sensors are the unsung heroes of automation. They perform the vital task of detecting the presence or absence of objects without physical contact. This non-contact operation translates directly to reduced wear and tear, longer service life, and minimal maintenance requirements. Within this broad category, inductive sensors reign supreme for detecting metallic targets. And when it comes to packaging these powerful inductive elements into a form factor ubiquitous across global industry, the M12 threaded housing is the gold standard.
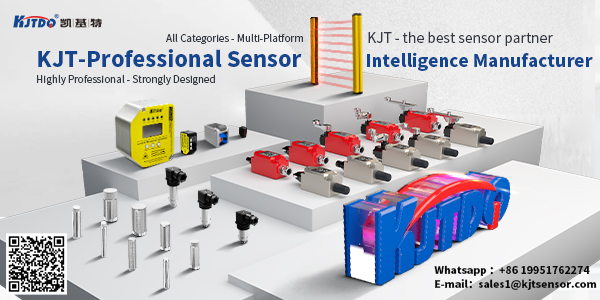
Why the M12 Design Dominates Industry
The M12 threaded barrel offers significant advantages that have cemented its place in factories worldwide:
- Robustness: The rugged metal or reinforced polymer housing provides excellent protection against impacts, vibration, and harsh environmental conditions.
- Standardization: The M12 form factor is an internationally recognized standard (defined in IEC 60947-5-2). This simplifies mounting, replacement, and sourcing of compatible connectors.
- Sensing Range: Despite their compact size (typically 12mm diameter), modern M12 sensors offer impressive sensing distances relative to their size, allowing flexible installation.
- Versatility: The threaded barrel design facilitates easy mounting in countless orientations using standard locknuts, even in tight spaces. Sealing properties meeting IP67/IP68/IP69K ratings ensure reliable operation in dusty, wet, or washdown environments common in food processing, packaging, and heavy machinery.
- Wide Compatibility: Vast arrays of cables and connectors with M12 interfaces are readily available globally.
The ifm Advantage: Engineering Excellence in Every Sensor
ifm electronic has built a formidable reputation on the pillars of precision, durability, and innovation. Their extensive range of M12 inductive proximity sensors embodies these principles, setting them apart:
- Unwavering Reliability: ifm sensors are renowned for their exceptional build quality and rigorous testing. They are designed to withstand millions of operating cycles, delivering consistent, fail-safe detection crucial for demanding industrial processes. This high reliability directly translates to reduced downtime and lower total cost of ownership.
- Extended Sensing Distances: Pushing the boundaries of physics, ifm offers M12 sensors with industry-leading sensing ranges. For example, their standard shielded inductive sensors provide impressive detection capabilities for ferrous metals, maximizing installation flexibility even in challenging layouts.
- Sophisticated Electronics: Beyond basic detection, many ifm M12 sensors incorporate advanced features:
- IO-Link Integration: Leading the Industry 4.0 charge, many ifm M12 sensors feature IO-Link communication. This open standard protocol transforms a simple sensor into a smart device, enabling parameter configuration, remote diagnostics, real-time process data transmission, and predictive maintenance capabilities.
- NAMUR Output: Specifically designed for hazardous areas, sensors with NAMUR output provide intrinsically safe operation within explosive atmospheres (ATEX/IECEx zones).
- Enhanced Switching Frequency: Capable of detecting very fast-moving targets or high-speed events on production lines.
- Specialized Materials: For aggressive chemical environments or ultra-hygienic applications (food & beverage, pharmaceuticals), ifm offers sensors constructed from high-grade stainless steel (V4A / 316L) and specialized polymers resistant to cleaning agents and harsh substances.
Where ifm M12 Proximity Sensors Deliver Impact
The applications for these robust sensors span virtually every industrial sector:
- Factory Automation: Detecting the presence of parts on conveyors, monitoring cylinder piston positions (end-of-stroke detection), verifying tool changes on CNC machines, and confirming workpiece clamping.
- Packaging Machinery: Detecting fill levels in bottles/cans, confirming the presence of caps or lids, counting packages, and controlling the position of capping heads or labeling units.
- Material Handling: Monitoring positions of pallets on automated guided vehicles (AGVs), detecting packages on sorting systems, and ensuring safe operation on conveyor transfers.
- Automotive Manufacturing: Position feedback on robots for welding and assembly, confirming part presence before joining operations, and monitoring automated guided carts (AGCs).
- Food & Beverage & Pharmaceutical: Crucial in hygienic areas due to stainless steel housing and high IP protection ratings. Used for level detection in tanks, detecting containers on washdown lines, and verifying seal integrity.
- Mobile Equipment: Monitoring hydraulic cylinder positions, detecting bucket or attachment angles, and providing feedback for control systems on excavators, loaders, and agricultural machinery.
Choosing the Right ifm M12 Sensor: Key Considerations
Selecting the optimal sensor for your application involves evaluating several factors:
- Target Material: Standard inductive sensors detect ferrous metals. For non-ferrous metals like aluminum or copper, look for ifm’s specialized sensors designed for these materials. Non-metallic targets require capacitive or photoelectric sensors.
- Required Sensing Distance: Determine the maximum air gap needed between the sensor face and the target. Choose an ifm M12 sensor whose published sensing range (Sn) comfortably exceeds this requirement.
- Electrical Requirements: Match the sensor’s operating voltage (e.g., 10-30V DC), output type (NPN, PNP, NO, NC), and current rating to your control system. Consider IO-Link compatibility for future-proofing and advanced diagnostics.
- Environmental Conditions: Assess temperature extremes, potential chemical exposure, required hygiene standards, and ingress protection needs (e.g., IP67 for temporary immersion, IP68 for continuous submersion, IP69K for high-pressure/high-temperature washdown). ifm offers sensors specifically rated for harsh and hazardous areas.
- Mounting Constraints: Ensure the sensor’s profile (flush, non-flush shielded, unshielded) suits the mounting location. ifm provides detailed dimensional drawings.
- Special Features: Do you need high switching frequency, analog output, temperature resistance above standard specs, or NAMUR output for safety?
In the relentless pursuit of efficiency, reliability, and uptime, equipping your machinery with quality sensing technology is non-negotiable. ifm M12 proximity sensors represent a pinnacle of design, offering a powerful combination of compact size, rugged durability, advanced features like IO-Link, and unwavering performance. From the harsh conditions of a foundry to the ultra-clean environments of a pharmaceutical lab, these sensors deliver consistent, contactless detection, forming the reliable backbone of countless automated systems worldwide. When detection fails, production stalls; choosing ifm M12 sensors is a proactive step towards eliminating that risk.