metal proximity sensor
- time:2025-07-02 00:36:22
- Click:0
Metal Proximity Sensors: Boost Efficiency and Cut Costs in Industrial Automation
Imagine a high-speed production line suddenly grinding to a halt. Faulty detection of a metal component caused a costly jam, missed delivery deadlines, and frustrated engineers. Metal proximity sensors prevent precisely this scenario, silently safeguarding efficiency within countless industrial processes. These robust electronic sentinels detect the presence of metallic objects without physical contact, forming an indispensable layer of intelligence in modern automation. By understanding how they work and where they excel, engineers and facility managers can unlock significant operational improvements.
The Unseen Force: How Metal Proximity Sensors Operate
At the heart of standard inductive proximity sensors lies a fascinating principle. An internal oscillator generates a high-frequency oscillating electromagnetic field radiating from the sensor’s face. When a metal target enters this active field, Eddy currents are induced within the metal. These tiny circulating currents draw energy from the sensor’s oscillator. Critically, this energy loss is detected by the sensor’s circuitry. Once a sufficient amplitude threshold is passed – correlating to a pre-determined sensing distance – the sensor’s output state switches (e.g., from OFF to ON, or ON to OFF). This instantaneous signal provides critical binary information: metal object present or metal object absent. Their operation relies entirely on the electromagnetic interaction with ferrous metals or non-ferrous metals like aluminum or copper (detectability varies by type and sensor model). Crucially, no physical contact occurs, minimizing wear and tear.
Where Metal Detection Makes the Critical Difference
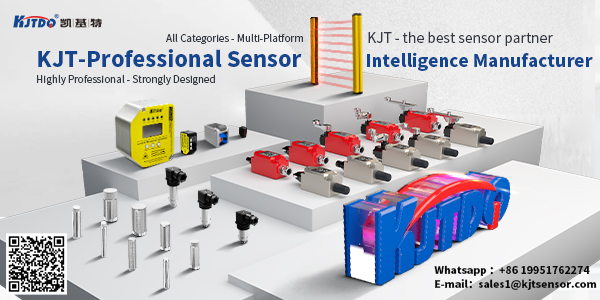
Industrial Metal Proximity Sensors are ubiquitous due to their reliability in harsh environments:
- Machine Safety & Position Verification: Ensuring machine guards are securely closed before heavy equipment activates is paramount. Sensors detect the metal guard’s position, preventing operation if open. They also confirm the correct positioning of clamps, hydraulic rams, tool holders, or robotic arms.
- Assembly Line Control & Counting: On automated production lines, these sensors detect metal parts for precise sequencing, verifying component presence before assembly, triggering actuators, or accurately counting finished products passing a point.
- Material Handling & Elevation Control: Monitoring fill levels in metal bins or hoppers, detecting the presence or absence of metal pallets on conveyors, and controlling the lift height in fork trucks or automated guided vehicles (AGVs) are common uses.
- Precision Machining: In CNC machining centers and lathes, they verify that raw metal stock (billets, bars) is loaded correctly before machining begins, reducing costly errors and potential damage.
- Packaging Machinery: Detecting metal lids, cans, or foil seals ensures correct placement and triggers sealing operations reliably.
The Compelling Advantages Driving Adoption
Choosing proximity sensors for metal detection delivers tangible benefits that directly impact the bottom line:
- Non-Contact Detection: The fundamental advantage. Eliminating physical wear on both the sensor and the target dramatically extends lifespan and reduces maintenance costs compared to mechanical switches.
- High Reliability & Long Service Life: With no moving parts to fail mechanically, these sensors offer exceptional durability, especially critical in demanding industrial settings involving vibration, dust, or moisture (within specified IP ratings).
- Very High Switching Speeds: Capable of detecting targets and changing output states thousands of times per second, they are perfect for high-speed automation where milliseconds matter.
- Robust Construction: Engineered to withstand industrial rigors, including resistance to common shock, vibration, and environmental contaminants like oils or coolants when correctly rated.
- Output Versatility: Available with various outputs (NPN, PNP, NO, NC, analog, IO-Link) to seamlessly integrate into complex control systems (PLCs, CNC machines, robotics).
Selecting the Optimal Metal Proximity Sensor: Key Factors
Maximizing performance requires careful consideration during sensor selection:
- Required Sensing Distance (Sn): This is the nominal range specified by the manufacturer for detecting a standard steel target. Always verify the Sn for the specific target metal (e.g., aluminum typically reduces the sensing range compared to mild steel). Account for installation clearance needs.
- Target Metal Type & Size: Sensor sensitivity varies. Ferrous metals (iron, steel) are easiest to detect. Non-ferrous metals like aluminum, brass, or copper require sensors specifically designed or adjusted for them. The target’s size and shape also impact detection reliability; excessively small targets might be undetectable at the required distance.
- Operating Environment: Consider ambient temperature extremes, potential exposure to chemicals, oils, coolants, dust, welding spatter, or high-pressure washdowns. Select sensors with the appropriate IP (Ingress Protection) rating and housing material (e.g., stainless steel for corrosive areas). High-vibration areas need rugged designs.
- Electrical Requirements: Match the sensor’s voltage supply (DC or AC), output type (e.g., PNP for “positive switching”), and current capacity to your control system’s requirements.
- Mounting Style: Cylindrical (threaded barrel) sensors are most common, but rectangular, block, or specialized flange-mount designs are available. Ensure the form factor suits the installation space and provides necessary protection.
Ensuring Peak Performance and Longevity
While renowned for durability, proper installation and maintenance are key:
- Secure Mounting: Ensure the sensor is rigidly fixed to prevent vibration-induced movement or damage. Maintain the correct gap between the sensor face and the normal position of the target metal per the Sn specification.
- Electrical Protection: Employ surge suppression on long cable runs or in environments with significant electrical noise. Ensure stable voltage supply within the sensor’s tolerance.
- Environmental Protection: Use sensors rated for the actual environmental conditions. Regularly clean the sensing face to prevent buildup of debris, metal chips, or oils that could impede performance.
- Regular Inspection: Include sensor checks in routine preventative maintenance schedules to identify any physical damage or performance degradation early.
Metal proximity sensors are far more than simple switches. They are sophisticated enablers of automation, providing the essential “eyes” that detect metallic components with unwavering reliability. From safeguarding personnel to ensuring precision assembly and optimizing material flow, their non-contact operation, inherent durability, and speed deliver measurable improvements in operational efficiency, reduced downtime, and lower cost per part. By strategically implementing and maintaining the right sensors for each application, industries consistently achieve smoother operations and a stronger competitive edge. The silent vigilance of these sensors underpins the heartbeat of modern manufacturing.