analog proximity sensor
- time:2025-07-02 00:30:18
- Click:0
Analog Proximity Sensors: The Unsung Heroes of Precise Distance Detection
In a world increasingly driven by digital signals and discrete thresholds, there remains a critical need for the nuanced language of the analog domain. When it comes to sensing the subtle changes in distance between objects – not just whether something is “there” or “not there,” but exactly how far away it is – analog proximity sensors step into the spotlight. These versatile devices translate the physical world’s continuous nature into an equally continuous electrical signal, providing a rich stream of data essential for sophisticated control and monitoring. Forget simple on/off; analog proximity sensors speak the language of gradients, enabling precision in environments where digital sensors fall short.
Beyond the Binary: What Makes a Sensor Analog?
Unlike their digital counterparts that provide a simple “present” or “absent” signal (often a clean 0V or 24V DC), analog proximity sensors output a signal that varies proportionally to the distance between the sensor and the target object. This output is typically:
- Voltage Analog: A DC voltage (e.g., 0-10V or 0.5-4.5V) that changes linearly (or sometimes inversely) as the target moves closer or farther away within the sensor’s sensing range.
- Current Analog (4-20mA): A current loop signal where the magnitude (e.g., 4mA = furthest point, 20mA = closest point) represents the distance. This is highly resistant to electrical noise over long cable runs, making it ideal for industrial settings. Some sensors also offer digital IO-Link outputs carrying analog values.
The key takeaway is continuous measurement. As the target moves, the sensor’s output signal changes smoothly and instantly, reflecting every incremental change in position. This provides a far richer data set than a simple trip point.
The Heartbeat of Sensing: Core Working Principles
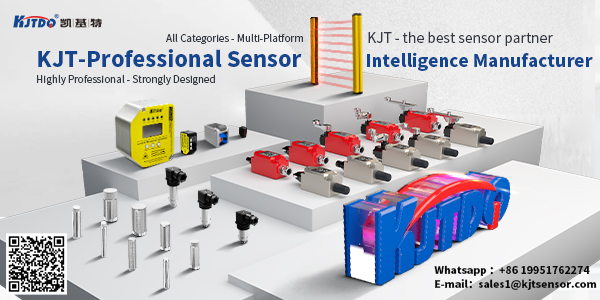
Analog proximity sensors leverage the same fundamental physical principles as digital ones, but their internal circuitry is designed to output a variable signal instead of triggering a switch. The most common types are:
- Analog Inductive Proximity Sensors: Detect metallic targets (ferrous and non-ferrous, though sensitivity varies). They generate an electromagnetic field. When a metal target enters this field, it induces eddy currents within the target. The sensor detects the change in oscillation amplitude or frequency caused by the energy loss from these currents. Crucially, the strength of this effect (and hence the signal change) is proportional to the distance to the target. This continuous change is converted into the analog output voltage or current.
- Analog Capacitive Proximity Sensors: Detect both metallic and non-metallic targets (liquids, plastics, wood, glass, etc.) by measuring changes in capacitance. The sensor forms one plate of a capacitor; the target forms (or influences) the other. As the target approaches, the capacitance increases. The sensor’s circuitry detects the magnitude of this capacitance change proportional to distance and converts it into the analog output signal.
- Analog Photoelectric Sensors (Specific Types): While many photoelectric sensors are inherently digital (object breaks the beam = signal on), certain configurations can provide analog outputs:
- Analog Diffuse Reflective: Output signal strength varies based on the distance to the target or its reflectivity (within the focal point range).
- Distance Measuring (Time-of-Flight / Triangulation): Actively measures the time it takes for a light pulse to return or uses triangulation principles to calculate distance, providing a direct analog output proportional to distance. These are highly precise for position sensing applications.
Why Choose Analog Output? Key Advantages Over Digital
The continuous nature of the analog signal unlocks capabilities digital sensors simply cannot match:
- Precise Position Monitoring: Critical advantage: Determine the exact position of an object within the sensing range. Ideal for monitoring fill levels, checking part dimensions (e.g., height, thickness), verifying precise positioning, or controlling actuators for smooth motion (like guiding robot arms).
- Speed/Distance Measurement: Detect the speed of a moving target passing by the sensor or measure the distance traveled by correlating signal changes over time.
- Material Thickness Detection: Measure the thickness of non-metallic materials (like paper, plastic film, rubber) using capacitive sensors by detecting the distance through the material to a reference point.
- Vibration Monitoring: Detect and measure the amplitude of vibration on machinery by observing the fluctuating analog signal from a target mounted on the vibrating surface.
- End-of-Line Quality Control: Go beyond presence/absence. Ensure a part is seated at the correct depth within an assembly or that a component (like a pin or spring) is present and extended the proper amount.
- Smoother Control: Provides the input needed for proportional-integral-derivative (PID) controllers or other advanced control algorithms requiring continuous feedback, leading to smoother, more stable processes than simple on/off control can achieve.
Where Analog Proximity Sensors Shine: Real-World Applications
The versatility of analog proximity sensors makes them indispensable across numerous sectors:
- Industrial Automation: Monitoring cylinder rod position for precise control, verifying part positioning in fixtures, measuring roll diameters in winding applications, controlling filling levels based on actual distance to liquid, detecting material warp or thickness variations.
- Automotive Manufacturing: Ensuring precise gap and flushness between body panels, verifying door/window positions during assembly, controlling robotic welder paths based on panel contours, monitoring engine component positions.
- Packaging Machinery: Controlling the position of filling heads, monitoring the stack height of products, detecting the thickness of packaging materials (foil, cardboard), ensuring label applicator alignment.
- Material Handling: Measuring roll diameters on conveyors, detecting the position of pallets or lifts, monitoring sag in cables or belts.
- Process Control: Liquid level sensing in tanks (especially with capacitive sensors), monitoring the position of valves, detecting deposits or buildup on walls inside tanks or pipes.
- Mobile Machinery: Monitoring position of hydraulic cylinders for precise implement control, detecting boom extension, measuring suspension travel.
Selecting the Right Analog Proximity Sensor: Key Considerations
Choosing the optimal analog proximity sensor requires careful evaluation:
- Target Material: Metal? Use inductive. Plastic, Liquid, Granular? Use capacitive. Specific reflectivity or needs distance? Consider analog photoelectric.
- Required Sensing Range: How far away does the target need to be detected? Analog sensors have specified linear ranges within their overall sensing distance.
- Desired Output: Voltage (0-10V, 0.5-4.5V) or Current (4-20mA)? 4-20mA is often preferred for noisy environments and long cable runs.
- Accuracy and Linearity: How closely must the output match the actual distance? Check the sensor’s datasheet for linearity specifications (typically ±1% to ±5% of full scale over the linear range).
- Resolution: The smallest detectable change in distance. Determines the fineness of control possible.
- Response Time: How quickly can the sensor reflect a change in distance? Crucial for high-speed applications.
- Environmental Factors: Temperature extremes, chemicals, dust, moisture, vibration? Ensure sensor housing and ingress protection (IP rating) are suitable. High EMI environments favor 4-20mA sensors. Cable length impacts voltage drop for voltage output sensors.
- Mounting and Size: Space constraints? Barrel style (common for inductive/capacitive) or block style?
Conclusion: Embracing the Continuum
While digital sensors excel at discrete detection tasks, analog proximity sensors are the solution when the degree of proximity matters. Their ability to deliver a continuous, proportional output signal provides the granular data necessary for precision positioning, accurate measurement