npn proximity sensor
- time:2025-07-01 14:46:33
- Click:0
NPN Proximity Sensors Unveiled: The Essential Choice for Robust Industrial Detection
Ever wondered how a machine knows a metal part is perfectly positioned before welding, or how a conveyor belt automatically stops when an object is detected? Often, the silent hero enabling this precision and safety is the NPN proximity sensor. These compact, reliable devices are fundamental components in modern automation, playing a critical role in millions of applications worldwide. Understanding what they are, how they function, and why they are so widely specified is key to grasping the backbone of industrial sensing technology.
Decoding Proximity Sensing: The Foundation
Before diving into NPN, let’s establish the basics. A proximity sensor is a non-contact device designed to detect the presence or absence of an object within a specific range without physical touch. They achieve this through various technologies like inductive (for metals), capacitive (for various materials, including liquids), ultrasonic, or photoelectric. Inductive proximity sensors are perhaps the most common in industrial metal detection scenarios and are the primary domain of NPN sensors. They work by generating an electromagnetic field; when a metallic target enters this field, it induces eddy currents within the target, causing a detectable change in the sensor’s own oscillation circuit. This change is then converted into a usable electrical signal.
The Core Concept: Why “NPN”?
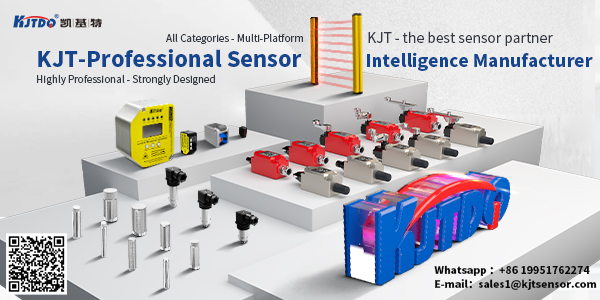
This is where the “NPN” designation becomes crucial. It refers to the type of transistor output used within the sensor’s switching circuit. NPN transistors are a specific type of bipolar junction transistor.
- Inside an NPN Proximity Sensor: The sensor incorporates an NPN transistor as its output switching element. In an NPN switch:
- The Emitter terminal is connected to the Negative (-) voltage supply (commonly 0V or ground).
- The Collector terminal provides the output signal.
- The Base is controlled by the sensor’s internal detection circuitry.
- The Switching Action (Sinking Output): When the sensor detects a target (its active state), the internal circuitry activates the base of the NPN transistor. This “turns on” the transistor, essentially closing a switch between the Collector and Emitter. Since the Emitter is tied to the negative supply, this means the Collector output terminal is effectively pulled down to near 0V (negative). Therefore:
- Detection (Active): Output Signal Sinks to Negative/Ground (Low Voltage).
- No Detection (Inactive): Output is effectively disconnected (Open Circuit / High Impedance).
This behavior defines an NPN proximity sensor as having a Normally Open (NO) configuration from a load perspective and, crucially, a sinking output. It sinks current to the negative supply when active.
Contrast: NPN vs. PNP
Understanding NPN becomes clearer when contrasted with its counterpart, the PNP proximity sensor:
- PNP Sensor: Uses a PNP transistor. Its Emitter is connected to the Positive (+) supply voltage. When active, it sources current from the positive supply out through its output (Collector) to the load. It has a sourcing output. Its inactive state is open circuit.
- Key Difference: NPN sinks current (to negative), PNP sources current (from positive).
Why Choose an NPN Proximity Sensor? Key Advantages
The widespread adoption of NPN proximity sensors isn’t accidental. They offer several compelling benefits:
- Compatibility with Legacy PLCs and DC Sinking Inputs: Many older Programmable Logic Controllers (PLCs) and control systems were designed with DC input modules configured specifically for sinking inputs. An NPN proximity sensor output matches perfectly with these modules – the PLC input expects to see 0V (ground) when the sensor is active, which is exactly what the NPN sensor provides. Connecting a PNP sensor to a sinking input typically requires additional components or isn’t possible without modification.
- Simplified Wiring in Common Negative Systems: In systems where the common point or return path for multiple DC circuits is the negative terminal (0V) – a very common configuration – wiring multiple NPN sensors is straightforward. All sensor outputs (when active) connect directly to this common negative, simplifying the wiring harness. The load (e.g., PLC input) is then connected between the positive supply and the sensor output. The sensor acts as the ground switch for the load.
- Perceived Safety / Fail-Safe Considerations: While both configurations can be made safe with proper design, there can be a perception or historical preference for NPN in certain safety-related contexts. The logic stems from the idea that if a wire breaks in the sensor’s output path or the sensor loses power, an NPN Normally Open (NO) sensor defaults to an “open circuit” (inactive) state. This “fails off” behavior can sometimes be advantageous in signaling the absence of a critical object or the occurrence of a fault. However, true safety always requires certified safety components and dedicated safety circuits.
- Cost and Availability: Due to their long-standing dominance, especially in certain regions and applications, NPN sensors are often readily available and can sometimes be found at slightly lower costs than PNP equivalents, though this gap has narrowed significantly.
- Robustness and Reliability: Like their PNP counterparts, modern NPN proximity sensors are built to withstand harsh industrial environments. Their non-contact operating principle means no moving parts to wear out, leading to exceptionally long service life and minimal maintenance requirements. They are immune to issues like contact bounce and can operate reliably under conditions of dirt, oil, vibration, and temperature extremes.
Typical Applications: Where NPN Proximity Sensors Shine
You’ll find NPN proximity sensors deployed across almost every industrial sector:
- Machine Tooling: Detecting tool position, part presence in fixtures, end-of-travel limits.
- Automated Assembly Lines: Counting parts, verifying component placement, controlling robotic movements.
- Packaging Machinery: Detecting film or carton presence, controlling fill levels (with capacitive types), verifying case sealing.
- Material Handling: Monitoring conveyor belt object detection, pallet positioning, gate control.
- Automotive Manufacturing: Position sensing in welding robots, verifying door or hood closure, detecting chassis position.
- Printing and Paper Processing: Web break detection, roll diameter monitoring, sheet counting.
- General Object Detection in Metal Machinery: Replacing limit switches for position sensing on cranes, lifts, valves, and actuators.
Important Considerations When Using NPN Sensors
- Load Connection: Crucially, the load (PLC input, relay coil, indicator lamp) must be connected between the NPN sensor’s output wire (Brown or Black) and the Positive (+) supply voltage (typically +24V DC). The sensor switches the load’s connection to ground. Connecting the load incorrectly will prevent the sensor from functioning.
- Supply Voltage: Ensure the sensor’s operating voltage (e.g., 10-30V DC) matches your control system’s power supply. Most industrial sensors operate on 12-24V DC.
- Wiring Colors: Standardization exists, but always consult the sensor datas