automation direct proximity sensor
- time:2025-07-01 13:40:24
- Click:0
Automation Direct Proximity Sensors: Streamlining Detection in Modern Automation
In the heart of every efficient factory floor, assembly line, or automated system, silent sentinels work tirelessly. These unsung heroes detect presence, absence, position, and even material composition without physical contact, enabling seamless machine operation and precise control. Among the most reliable and cost-effective solutions powering this critical detection layer are Automation Direct proximity sensors. Understanding their capabilities and how they integrate into the broader Automation Direct ecosystem is key to optimizing performance and reducing downtime.
Demystifying the Proximity Sensor
At its core, a proximity sensor is a non-contact electronic device designed to detect the presence or absence of an object within its sensing field. Unlike mechanical switches, they offer significant advantages: no physical wear from repeated contact, high-speed operation suitable for rapid production lines, immunity to oil, dirt, and vibration in harsh industrial environments, and long operational life.
The most common type found in industrial automation, and a cornerstone of the Automation Direct lineup, is the inductive proximity sensor. These sensors generate an electromagnetic field. When a metallic target (like steel, aluminum, brass, etc.) enters this field, it induces eddy currents within the target. The sensor detects the resulting change in the field’s oscillation and triggers its output switch (solid-state transistor). Key specifications include sensing distance (the range at which it can reliably detect a standard target), output type (typically NPN or PNP, sinking or sourcing), housing material (stainless steel, nickel-plated brass, plastic), and environmental ratings (IP67, IP69K for resistance to water/dust).
The Automation Direct Advantage: Value & Variety
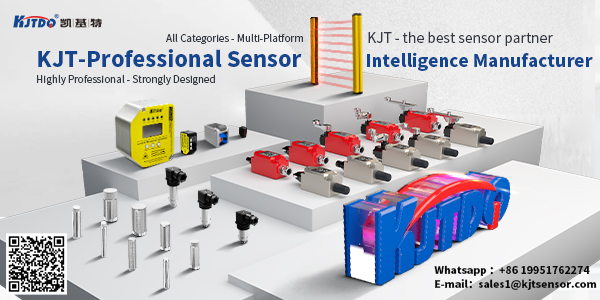
Automation Direct has earned a strong reputation by offering a vast selection of industrial components at competitive prices, backed by excellent technical support. Their proximity sensor range exemplifies this philosophy. You’ll find:
- Extensive Form Factors: From miniature cylindrical sensors (M8, M12, M18, M30) ideal for tight spaces to larger rectangular or block-style sensors for robust applications. Barrel dimensions and mounting styles (threaded, flush/non-flush mountable) cater to diverse installation needs.
- Multiple Sensing Technologies: While inductive sensors dominate for metal detection, Automation Direct also offers:
- Capacitive Proximity Sensors: Detect both metallic and non-metallic objects (liquids, plastics, wood, granules) based on changes in capacitance.
- Ultrasonic Sensors: Measure distance or detect objects using sound waves, effective for clear objects and level sensing.
- Photoelectric Sensors (Though technically different, often grouped): Use light beams (visible, infrared, laser) for long-range detection or specific object characteristics.
- Diverse Output Configurations: Options include:
- 2-wire AC/DC: Simplifies wiring but has leakage current considerations.
- 3-wire DC (NPN or PNP): The most common, offering sinking or sourcing outputs compatible with most PLCs (like Automation Direct’s popular Productivity, Do-more, or CLICK series).
- 4-wire (Dual Output): Combining both NPN and PNP outputs in one device.
- Analog Output: Providing a continuous signal proportional to the distance to the target.
- IO-Link: Enabling advanced diagnostics, parameterization, and seamless integration into smart factories.
- Robust Construction: Emphasis on IP67 and IP69K ratings ensures sensors withstand washdowns, dust, oils, and typical industrial abuse. Stainless steel housings offer superior corrosion resistance.
- Cost-Effectiveness: Automation Direct consistently provides high-quality sensors at accessible price points, making automation upgrades or new projects more feasible without sacrificing reliability.
Driving Application Success: Where Proximity Sensors Shine
The applications for Automation Direct proximity sensors are virtually limitless within industrial automation:
- Position Verification: Confirming a part is present on a fixture, pallet, or conveyor at a specific workstation.
- End-of-Travel Detection: Sensing when a cylinder piston or linear actuator has fully extended or retracted.
- Object Counting: Tallying products, bottles, or packages moving past a point on a conveyor.
- Speed Monitoring: Detecting teeth on a gear or shaft rotation for RPM calculation.
- Material Handling: Confirming bin levels (capacitive), pallet presence, or robotic gripper closure.
- Machine Safety: Serving as part of interlocks to confirm guards are closed or safety zones are clear before machine start.
- Sorting Systems: Identifying different types of materials (metal vs. non-metal) using inductive or capacitive sensors.
Selecting the Right Automation Direct Proximity Sensor
Choosing the optimal sensor involves carefully assessing your application demands:
- Target Material: Metal? Inductive. Non-metal/liquid? Capacitive or Ultrasonic. Specific color/contrast? Photoelectric.
- Required Sensing Distance: How far away does the target need to be detected? Remember the rated sensing distance is for mild steel; different metals and sensor types (flush vs. non-flush) affect actual range.
- Environment: Exposure to chemicals, water jets, high temperatures, or intense vibration necessitates specific IP ratings and housing materials. Automation Direct sensors clearly list these specs.
- Output Compatibility: Match the sensor’s output type (NPN, PNP) and voltage level (commonly 10-30V DC) with your PLC or controller input module requirements. Automation Direct PLC inputs are well-documented for easy matching.
- Physical Size & Mounting: Consider available space and the most secure mounting method (threaded, bracket, etc.).
- Special Features: Need analog feedback for distance measurement? Require IO-Link for diagnostics? Automation Direct offers these advanced options.
Installation & Best Practices: Maximizing Reliability
Proper installation is crucial for optimal proximity sensor performance and longevity:
- Avoid Sensing Interference: Mount sensors away from large metal objects (like machine frames) within their sensing field. Follow recommended lateral and axial spacing guidelines between multiple sensors.
- Consider Target Approach: For inductive sensors, approach the target perpendicular to the sensing face for maximum range. Note the difference between flush-mountable (can be embedded in metal) and non-flush mount sensors.
- Secure Wiring & Protection: Use conduit or cable carriers to protect wiring from damage. Ensure connections are tight and follow correct polarity for 3-wire DC sensors. Employing Automation Direct’s cable management solutions can enhance organization.
- Verify Operation: Always test the sensor with the actual target material under real operating conditions (speed, temperature) after installation.
Troubleshooting Common Issues
Even robust Automation Direct sensors can encounter problems. Common issues and fixes:
- No Output: Check power supply voltage and polarity. Verify wiring connections and cable integrity. Ensure the target is within the sensing range and made of detectable material. Test the sensor independently if possible.
- Intermittent Output: Often caused by loose wiring, unstable power supply, vibration causing movement, target alignment issues, or insufficient sensing range for the application speed.
- Sensor Triggering Without Target: Look for nearby metal causing interference, electrical noise coupling into the signal lines (ensure proper shielding/grounding), or a failing sensor. Sometimes environmental factors like metal dust buildup can cause this.
By strategically deploying Automation Direct proximity sensors, engineers and maintenance professionals leverage a powerful toolset for enhancing reliability, increasing throughput, and reducing maintenance costs across countless automated processes. Their combination of performance, durability, variety, and Automation Direct’s hallmark value makes them an indispensable component in the modern industrial landscape.