laser proximity sensor
- time:2025-07-01 12:34:05
- Click:0
Laser Proximity Sensors: Precision Detection for Modern Automation
Imagine a sleek robotic arm assembling a smartphone. It moves with lightning speed, placing microscopic components onto a circuit board. Inches away, another arm precisely welds a car chassis. How do these machines avoid catastrophic collisions and achieve near-impossible accuracy? The unseen heroes are often laser proximity sensors, silently orchestrating precise and reliable non-contact distance measurement. These sophisticated devices are fundamental pillars in modern industrial automation, quality control, and countless other fields where knowing exactly how far, fast, or present something is makes all the difference.
So, What Exactly is a Laser Proximity Sensor?
At its core, a laser proximity sensor (LPS) is a non-contact device that detects the presence, absence, or position of a target object and measures its distance by emitting a focused laser beam. Unlike mechanical limit switches or basic photoelectric sensors, LPS harnesses the unique properties of laser light – primarily its coherence, monochromaticity, and ability to be focused into an extremely narrow beam. This allows for unparalleled precision over significant distances.
The sensor operates by projecting this concentrated laser spot onto a target. Reflected light from the target is then captured by a receiver within the sensor. The critical measurement occurs by analyzing the characteristics of this returned light beam. Two primary principles dominate how LPS determine distance:
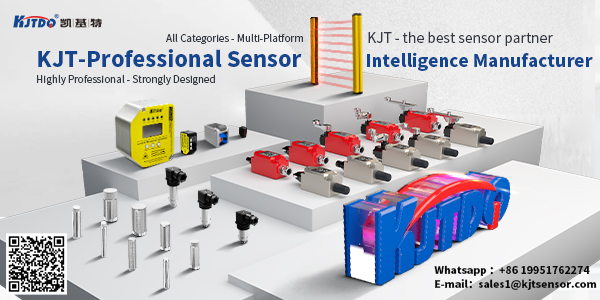
- Time-of-Flight (ToF): This method is conceptually simple but requires high-speed electronics. The sensor precisely measures the time delay between emitting the laser pulse and receiving its reflection. Since the speed of light is constant, this time difference directly translates into the distance to the target (
Distance = (Speed of Light × Time Delay) / 2
). ToF sensors excel in longer-range applications.
- Triangulation: More common for shorter, high-precision needs. Here, the emitted laser beam and the receiver lens are intentionally offset. The position where the reflected beam strikes a dedicated detector (like a Position-Sensitive Device - PSD or CMOS array) changes depending on the target’s distance. Using trigonometric principles, the sensor calculates the distance based on the detected spot position on the receiver. This method provides exceptional resolution at close quarters.
The Hallmarks of Laser Proximity Sensors: Key Capabilities
LPS offer a constellation of advantages that make them indispensable across sectors:
- Exceptional Precision and Resolution: Their focused laser spot enables detection and measurement with resolutions down to micrometers, far surpassing ultrasonic or diffuse photoelectric sensors. This is critical for applications like semiconductor wafer alignment or micromachining.
- High Accuracy: Advanced electronics and stable laser sources deliver highly reliable and repeatable measurements, essential for processes demanding tight tolerances.
- Operation at Significant Standoff Distances: Depending on the model and principle, LPS can accurately measure targets from a few millimeters up to several meters away, providing flexibility in system design.
- Non-Contact Measurement: This is paramount. LPS exert no physical force on delicate targets, prevent wear and tear on both sensor and object, and are unaffected by target surface texture in many modes (except diffuse reflection types, which rely on scattered light). Non-contact operation ensures longevity and avoids contamination.
- Small Target Detection: The tiny laser spot allows detection of very small objects, thin wires, or precise edges that larger beam sensors might miss.
- High Speed: Capable of extremely fast response times, LPS are perfect for high-speed automation lines, robotics, and dynamic position tracking.
- Excellent Background Suppression: The focused beam and specific receiver optics make LPS highly resistant to interference from ambient light or background objects, ensuring reliable operation in complex environments. Hysteresis (the difference between the switch-on and switch-off points) is also typically very low and adjustable for precise control.
- Solution for Diverse Surfaces: While highly reflective or mirror-like targets can pose challenges (requiring specific sensor models or setup), LPS generally perform well across a wide range of materials – metal, plastic, wood, glass, and more.
Where Laser Proximity Sensors Shine: Core Applications
The unique blend of precision, speed, and non-contact operation drives LPS adoption in numerous critical areas:
- Industrial Automation & Robotics: This is arguably the largest domain. LPS provide precise positioning feedback for robotic arms (end-effector guidance), detect part presence/absence on conveyors (even small or transparent items), control automated guided vehicles (AGVs), ensure parts are correctly seated in fixtures, and oversee high-speed assembly processes. They are vital for collision avoidance within robotic workcells.
- Material Handling & Logistics: LPS monitor object height on pallets for stacking/unstacking robots, control filling levels in containers (especially where non-contact is vital), detect package jams on sorting lines, and guide automated cranes.
- Precision Manufacturing & Machining: Quality control is paramount. LPS measure dimensions (thickness, width, height, diameter) of parts with micron-level accuracy on production lines. They monitor vibration in machinery for predictive maintenance, control tool position on CNC machines, and inspect surface profiles.
- Automotive Industry: From controlling robot welders and verifying door gap dimensions to checking component alignment on the assembly line and inspecting paint thickness, LPS are ubiquitous in modern car manufacturing for precision positioning and quality assurance.
- Electronics & Semiconductor: Handle delicate components with non-contact sensors. LPS ensure accurate placement of chips on PCBs, measure wafer thickness and bow, control wire bonding machines, and verify the position of microscopic components.
- Packaging & Printing: Used to precisely control web tension, detect splices, monitor fill levels in bottles/cans without contact, and verify label placement accuracy.
Why Choose Laser Over Other Proximity Technologies?
While inductive sensors are great for metal, capacitive for non-metalls, and ultrasonic for longer range or harsh environments, laser proximity sensors fill a critical niche:
- Versatility: Detect nearly any material type.
- Highest Precision: Unmatched resolution and accuracy for demanding tasks.
- Smallest Spot Size: Essential for detecting tiny objects or precise edges.
- Excellent Background Suppression: Superior in cluttered environments compared to diffuse photoelectric sensors.
- Long, Focused Range: Maintain high resolution over distances where other optical sensors blur.
Implementing Laser Proximity Sensors: Key Considerations
To maximize LPS effectiveness:
- Target Surface: Highly reflective or dark/absorbent surfaces may require specific sensor models (e.g., with background suppression or longer ranges) or setup adjustments (gain tuning). Optimal performance is usually on matte, diffusely reflecting surfaces.
- Environment: While robust, excessive dust, steam, or airborne particles can scatter or block the laser beam. Protective air curtains or specific sensor housings might be needed. Intense ambient light can also interfere, though most LPS have strong ambient light immunity.
- Mounting & Alignment: Precise alignment is crucial, especially for triangulation sensors. Stable mounting prevents vibration causing measurement drift. Ensure the beam path is unobstructed.
- Sensor Selection: Carefully match the sensor’s range, spot size, accuracy, response time, output type (analog, digital, IO-Link), and environmental rating to the specific application demands.
From the intricate world of microchip fabrication to the powerful movements of industrial robots and the relentless pace of packaging lines, laser proximity sensors are the silent guardians of precision and efficiency. Their ability to deliver non-contact distance measurement with high precision, exceptional speed, and remarkable reliability cements their role as a cornerstone technology driving innovation and quality in countless modern processes. Understanding their principles and capabilities allows engineers and designers to unlock new levels of performance in automation and measurement tasks.