prox 2000 proximity sensor
- time:2025-07-01 02:02:35
- Click:0
The PROX 2000 Proximity Sensor: Precision Detection Powerhouse for Demanding Automation
In the intricate dance of modern manufacturing and automation, countless unseen components orchestrate flawless operation. Among these unsung heroes are proximity sensors, the silent sentinels detecting presence, absence, or position without physical contact. When reliability and precision are paramount, the PROX 2000 proximity sensor emerges as a trusted and versatile solution for a wide spectrum of industrial challenges. This inductive powerhouse delivers consistent, non-contact detection crucial for optimizing processes, enhancing safety, and minimizing downtime.
Understanding the Inductive Advantage
At the heart of the PROX 2000 lies inductive sensing technology. This principle relies on generating a high-frequency electromagnetic field from the sensor’s face. When a metallic target (typically ferrous metals like steel or iron, though some sensors detect non-ferrous metals) enters this field, it induces small electrical currents called “eddy currents” within the target. These eddy currents absorb energy from the sensor’s oscillating field. The PROX 2000 meticulously monitors this energy loss, triggering a clean, solid-state output signal once a predefined threshold is crossed. This entire process happens without any physical contact, eliminating wear and tear on both the sensor and the target.
This inherent non-contact operation is a cornerstone benefit. It translates directly to exceptional longevity, reduced maintenance requirements, and immunity to issues like dirt, dust, oil, and grease that plague mechanical switches. Whether submerged in cutting fluid, coated in wood chips, or exposed to vibration, the PROX 2000 reliably performs, making it a robust solution for harsh industrial environments.
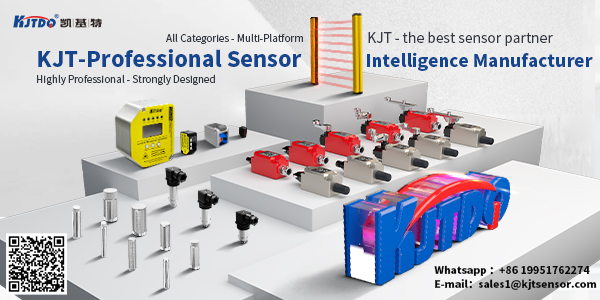
Key Capabilities of the PROX 2000
Engineered for demanding applications, the PROX 2000 series typically offers features that solidify its position in automation:
- Rugged Construction: These sensors are often built with robust stainless steel or nickel-plated brass housings, featuring high Ingress Protection (IP) ratings (commonly IP67 or IP68). This means they shrug off high-pressure washdowns, resist corrosive chemicals to a significant degree, and operate reliably in wet, dusty, or oily conditions.
- Shielded vs. Unshielded Options: Many PROX 2000 variants come in both shielded and unshielded configurations.
- Shielded (Flush Mountable): The sensing field is focused primarily forward. This allows the sensor to be mounted flush into metal brackets without causing interference, ideal for space-constrained installations.
- Unshielded (Non-Flush Mountable): Offers a longer sensing range but requires space around the sensor face (free of metal) to function correctly.
- Adjustable Sensing Range: While specific ranges vary by model, the PROX 2000 series often provides adjustable sensing distances. This crucial feature allows fine-tuning during installation to accommodate slight variations in target positioning or mounting tolerances, ensuring reliable triggering.
- Reliable Outputs: Equipped with solid-state NPN (sinking) or PNP (sourcing) transistor outputs (typically 3-wire DC configurations), the PROX 2000 provides fast, bounce-free switching signals compatible with Programmable Logic Controllers (PLCs), counters, timers, and other control systems.
- LED Status Indicator: An integrated LED visibly signals the sensor’s operational status (power on/target detected), significantly simplifying installation, commissioning, and troubleshooting.
Where the PROX 2000 Proximity Sensor Excels - Real-World Applications
The combination of robustness, non-contact sensing, and reliability makes the PROX 2000 indispensable across diverse sectors:
- Machine Tooling: Accurately detecting tool position (presence/absence), monitoring coolant levels, confirming chuck clamping, verifying part presence before machining, and controlling turret indexing on CNC machines. Precision is non-negotiable here.
- Material Handling: Counting products on conveyors (bottles, boxes, parts), detecting pallet presence at transfer points, verifying container positioning for filling or labeling, and monitoring position on automated guided vehicles (AGVs) or lifts. High-speed, reliable counting is essential.
- Packaging & Bottling: Verifying cap placement, detecting filled vs. empty bottles/cans, controlling carton erectors, confirming case sealing, and monitoring film/web breaks. High-cycle operations demand consistent performance.
- Automotive Manufacturing: Monitoring robotic arm positions, detecting parts on assembly lines (e.g., engines, doors, wheels), confirming fixture clamping, sensing end-of-travel on actuators, and controlling welding operations. Ruggedness is critical in these environments.
- Food & Beverage Processing: Detecting metal lids, controlling filling levels (metal containers), monitoring conveyor chain movement, and verifying position on food processing machinery – all while resisting washdown chemicals and moisture. High IP ratings are vital.
- General Factory Automation: Position sensing for cylinders, end-of-stroke detection, part presence verification in assembly jigs, speed monitoring on rotating shafts (using gear teeth as targets), and safeguarding access to dangerous machinery (safety interlocks – often requiring specific certified safety sensors, but standard PROX can be part of safety circuits).
Selecting and Installing Your PROX 2000 for Optimal Performance
Choosing the right PROX 2000 involves considering several factors:
- Target Material: Primarily ferrous steel? Or non-ferrous metals like aluminum or brass? Standard inductive models excel with ferrous targets; special variants may be needed for reliable non-ferrous detection.
- Required Sensing Distance: Select a model whose nominal or adjustable range comfortably exceeds your actual application gap. Include a safety margin!
- Mounting Constraints: Does it need to be flush-mounted (choose shielded), or is there sufficient clearance (unshielded offers longer range)?
- Environmental Conditions: Assess the presence of water, chemicals, temperature extremes, and vibration. Match the sensor’s IP rating, temperature specification, and housing material (stainless steel for harsher conditions) accordingly.
- Electrical Requirements: Ensure compatibility with your control system voltage (commonly 10-30V DC) and required output type (NPN or PNP).
Installation is typically straightforward. Secure the sensor using its threaded barrel (M8, M12, M18, M30 are common sizes), ensuring proper orientation and achieving the correct gap between the sensor face and the target. Fine-tune the sensing distance using the adjustment screw (if equipped) during commissioning. Always power down the circuit before wiring, carefully connecting the brown wire (+V), blue wire (0V/GND), and black wire (output signal) as per the manufacturer’s datasheet and your control system requirements.
The Unseen Backbone of Efficiency
While they operate silently and often out of sight, proximity sensors like the PROX 2000 are fundamental to the smooth, efficient, and safe operation of modern industrial systems. Their ability to provide non-contact, wear-free detection of metallic objects in challenging environments makes them an invaluable asset. By understanding the technology, key features, and diverse applications of the PROX 2000 inductive proximity sensor, engineers and maintenance personnel can leverage its capabilities to enhance automation reliability, improve productivity, and reduce costly downtime. When consistent, precise metallic object detection is required under tough conditions, the PROX 2000 delivers proven performance.