u type photoelectric sensor
- time:2025-07-26 02:17:50
- Click:0
U-Type Photoelectric Sensors: Streamlining Object Detection on the Factory Floor
Imagine a bustling factory assembly line suddenly grinding to a halt. Bottles pile up, misaligned parts cause jams, and productivity vanishes. What silent sentry failed? Often, it’s a simple photoelectric sensor – specifically, the reliable U-type photoelectric sensor – that plays the crucial, unseen role in keeping automated processes flowing smoothly. These compact workhorses are fundamental components in countless industries, providing fast, precise, and non-contact detection essential for modern manufacturing and logistics.
Understanding the U-Type Photoelectric Sensor
At its core, a U-type photoelectric sensor, often referred to colloquially as a “fork sensor,” is a self-contained optical sensing unit. Its defining characteristic is its physical shape: a sturdy U-shaped housing that integrates both a light emitter (typically an infrared LED) on one “arm” and a light receiver (a phototransistor or photodiode) directly opposite on the other arm. This precise, fixed alignment creates a narrow detection gap or “slot” between the two arms.
The fundamental operating principle is straightforward:
- Emission: The integrated LED emits a beam of modulated light (usually infrared to minimize interference from ambient light).
- Transmission: This light beam travels directly across the gap to the receiver.
- Reception & Signal Processing: The receiver continuously monitors the intensity of the incoming light.
- Detection Logic: When an opaque object enters the gap, it interrupts the light beam. The receiver detects this sudden drop in light intensity and triggers the sensor’s output circuit. Conversely, when the beam is uninterrupted, the output state remains unchanged (or vice-versa, depending on sensor configuration – Light ON or Dark ON).
The Distinct Advantages of the U-Shape Design
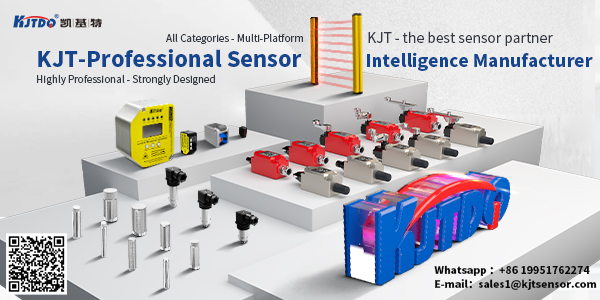
This integrated emitter-receiver design within a rigid U-frame offers several compelling benefits over other photoelectric sensor types like through-beam or diffuse-reflective sensors:
- Simplified Alignment & Installation: This is the key advantage. Since the emitter and receiver are pre-aligned and fixed within a single housing, installation is incredibly simple. There’s no need for time-consuming and precise alignment of separate units across a conveyor or machine frame. Simply mount the U-sensor bracket, and it’s ready to detect objects passing through its gap. This drastically reduces setup time and complexity.
- Exceptional Reliability & Stability: The fixed alignment virtually eliminates the risk of misalignment caused by vibration, thermal expansion, or accidental bumps – a common issue with separate-emitter/receiver through-beam setups. Once installed, U-type sensors offer rock-solid detection stability.
- Compactness: Integrating both optical components into one compact unit saves valuable space in crowded machinery or tight assembly lines.
- Fast Response Times: U-type sensors are renowned for their high-speed detection capabilities. They can reliably sense objects moving at very high speeds, making them ideal for high-throughput packaging, bottling, printing, and assembly applications.
- Handling Small Objects: The precise gap allows for the detection of very small objects, threads, wires, or components that might be difficult for other sensor types to reliably spot.
- High Resolution: Due to the close proximity of emitter and receiver and the focused beam, U-type sensors offer excellent resolution for detecting fine details or the edges of objects.
Where U-Type Sensors Shine: Core Applications
Their unique design makes U-type photoelectric sensors the preferred choice in numerous scenarios:
- Object Presence/Absence Detection: Fundamentally, confirming if an item is present at a specific point on a conveyor belt or assembly line.
- Counting: Accurately tallying products (bottles, cans, boxes, pills, components) as they pass through the sensor gap.
- Position Verification: Ensuring parts or products are correctly positioned before subsequent operations like labeling, filling, or sealing.
- Jam Detection: Identifying pile-ups or blockages on conveyors by detecting the absence of expected gaps between objects.
- Edge Guiding/Detection: Verifying the edge position of materials like paper, film, fabric, or metal sheets in web processing.
- Speed Monitoring: Calculating the speed of moving objects or rotating shafts equipped with flags that break the beam.
- Security: Detecting door or gate closures, or the presence of objects in restricted areas.
U-Type vs. Fork Sensors vs. Slot Sensors: Terminology Clarification
You’ll often hear the terms “U-type,” “fork sensor,” and “slot sensor” used interchangeably, and for good reason. They essentially describe the same core concept:
- “U-Type” refers to the physical shape resembling the letter “U.”
- “Fork Sensor” is a colloquial term emphasizing the fork-like structure where objects pass between the tines.
- “Slot Sensor” highlights the narrow detection slot or gap between the emitter and receiver arms.
While subtle variations in housing design might exist (e.g., some may have a slightly more squared-off “C” shape, but functionally identical), they all share the critical defining features: an integrated emitter-receiver pair within a rigid housing forming a fixed detection gap.
Choosing the Right U-Type Sensor: Key Considerations
Selecting the optimal U-type sensor for your application involves evaluating several factors:
- Gap Size: The physical width between the emitter and receiver arms determines the maximum size of the objects it can detect (or the minimum gap required to sense them). Choose a gap slightly wider than your typical object.
- Minimum Detectable Object: The smallest opaque object the sensor can reliably detect when it breaks the beam. Manufacturers specify this based on beam width and sensitivity.
- Response Frequency / Switching Speed: How rapidly the sensor can detect objects passing through the gap. Crucial for high-speed lines.
- Light Source: Infrared is most common, but red light versions exist for visual alignment verification.
- Output Type: NPN/PNP transistors, relay contacts, analog outputs, or IO-Link for digital communication. Match to your controller input.
- Output Logic: Light Operate (output ON when beam is interrupted) or Dark Operate (output ON when beam is not interrupted).
- Environmental Rating (IP Rating): Essential for harsh environments. IP67 (dust-tight and protected against immersion) is very common for industrial U-sensors.
- Connection Type: Pre-wired cables or quick-disconnect connectors (M8, M12).
- Special Features: Options like built-in amplifiers reducing the need for external controllers, sensitivity adjustment, or failsafe operation ensuring safety outputs trigger on sensor failure or beam block (critical for safety-related functions).
Feature |
U-Type / Fork Sensor |
Separate Emitter/Receiver Through-Beam |
Diffuse Reflective |
Emmitter/Receiver |
Integrated in one housing |
Separate units |
Integrated unit |
Installation |
Simple, no alignment |
Complex, precise alignment needed |
Simple mounting |
Alignment Stability |
Excellent |
Vulnerable to misalignment |
Less vulnerable |
Detection Range |
Very short (fixed gap) |
Very long |
Short to medium |
Detection Principle |
Beam interruption |
Beam interruption |
Reflection off object |
Object Color/Finish |
Unaffected |
Unaffected |
Affected (less reliable on dark/absorbent) |
Best For |
High-speed counting, small objects, presence in confined space |
Long-range detection, large areas |
Non-interruptive detection, varied surfaces |
**Conclusion: The Ubiquitous Enabler of Automation