rectangular photoelectric sensor
- time:2025-07-25 04:10:09
- Click:0
Unveiling the Rectangle: Why Rectangular Photoelectric Sensors Are Automation Cornerstones
Imagine thousands of items flawlessly gliding down a high-speed conveyor belt. A robotic arm, with uncanny precision, picks and places each one. Critical safety barriers silently monitor for human presence. At the heart of this intricate dance of modern automation lies a deceptively simple hero: the rectangular photoelectric sensor. Far more than just a boxy component, its unique shape and function make it an indispensable workhorse in countless applications demanding reliable, non-contact object detection.
Beyond the Basic Beam: Defining the Rectangular Photoelectric Sensor
At its core, a photoelectric sensor detects the presence, absence, or distance of an object using light. A rectangular photoelectric sensor specifically describes the physical housing shape of this device, distinct from cylindrical or block-style sensors. This rectangular form factor isn’t merely aesthetic; it’s intrinsically linked to key performance advantages. Inside that robust, often metal or rugged plastic casing reside the essential components: an emitter (typically an LED or laser diode generating the light beam) and a receiver (a phototransistor or photodiode that detects changes in the received light). The magic happens when an object interrupts or reflects this light beam, triggering the sensor’s output signal.
The Structural Advantage: Why the Rectangle Reigns Supreme
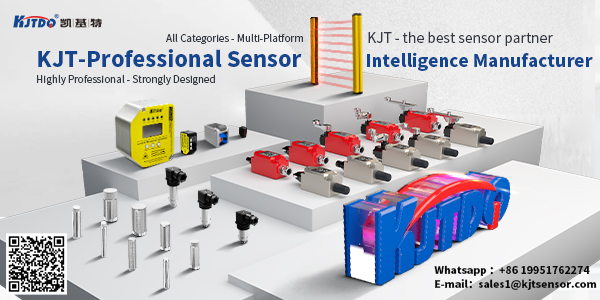
The rectangular design offers several critical benefits that make it a preferred choice in demanding industrial environments:
- Maximized Sensing Surface: Compared to a cylinder of similar width, the rectangular profile provides a significantly larger aperture area for the emitter and receiver lenses. This larger “window” translates directly to:
- Enhanced Light Gathering: The receiver can capture more of the emitted light (in reflective modes) or detect weaker beams more reliably (in through-beam setups), boosting sensing range and stability.
- Greater Tolerance for Misalignment: In applications where perfect sensor-to-target alignment is challenging (think vibrating machinery or thermal expansion), the larger receiver area offers more forgiveness. Minor shifts won’t immediately cause detection failure.
- Improved Detection of Small or Low-Contrast Objects: Smaller objects are more likely to fully interrupt the broader beam profile. Similarly, detecting clear bottles, glossy films, or thin wires becomes more feasible with the increased light interaction area.
Optimized Mounting and Protection: The flat surfaces of the rectangular housing are inherently easier to mount securely using standard brackets. Its shape also lends itself naturally to rugged designs featuring IP67, IP68, or IP69K ratings, providing exceptional resistance against dust, high-pressure water jets, and harsh washdown chemicals – crucial in food & beverage, pharmaceutical, and outdoor applications. The robust structure better protects internal components from shock and vibration compared to some slimmer designs.
Intrinsic Beam Shaping: While cylindrical sensors often require external mounting accessories to create a narrow slit beam, the rectangular shape naturally facilitates generating a focused, rectangular beam profile. This is particularly advantageous:
- For Edge Detection: Ensuring precise triggering when the edge of an object breaks the beam.
- For Ignoring Background: Minimizing false triggers from reflective surfaces beyond the target object.
- For Detecting Thin Materials: Like sheets of paper, foil, or thin wires crossing the beam path.
Principles in Action: How Rectangular Sensors Work
Like all photoelectric sensors, rectangular types operate based on three fundamental principles:
- Through-Beam: Emitter and receiver are housed in separate rectangular units, facing each other. Detection occurs when the object blocks the light beam traveling directly between them. This mode offers the longest sensing ranges and highest immunity to object surface color or reflectivity. It’s ideal for high-speed counting, precise positioning over long distances, and detecting opaque objects reliably.
- Retro-Reflective: The emitter and receiver are combined in one rectangular housing. A specialized reflector (corner-cube reflector) bounces the emitted light directly back to the receiver. Detection occurs when an object breaks this reflected beam. This provides simpler wiring (only one sensor unit mounted) and good range, though slightly less than through-beam. Works well for pallet presence, door open/close detection, and conveyor gaps.
- Diffuse (Proximity Mode): Emitter and receiver are again housed together in the rectangular unit. The sensor detects light reflected directly off the target object itself. Detection range is shortest and highly dependent on the object’s size, color, and surface texture (matte vs. shiny). The large aperture of the rectangular sensor significantly enhances performance here, allowing longer diffuse sensing ranges and better detection of dark or non-reflective targets compared to smaller apertures. Ideal for short-range presence detection, label sensing, or bottle cap verification.
Where the Rectangle Shines: Key Applications
The unique strengths of rectangular photoelectric sensors make them ubiquitous across automation:
- Manufacturing & Assembly Lines: Detecting parts on conveyors, verifying component placement, monitoring robotic arm paths, ensuring correct jig or pallet loading, counting products. Their ruggedness handles the industrial environment.
- Packaging Machinery: Ensuring film/web presence, verifying case flaps are closed, detecting filled vs. unfilled containers, controlling label application, checking seal integrity. Washdown models excel in hygiene-critical areas.
- Material Handling & Logistics: Monitoring pallet flows, detecting parcels on sorters, verifying box dimensions at gates, presence detection on automated guided vehicles (AGVs).
- Printing & Converting: Precisely detecting sheet edges for registration, verifying web breaks, counting printed items, monitoring roll diameters.
- Food & Beverage Processing: Detecting bottles/cans on high-speed fillers, checking cap application, verifying package fill levels, presence sensing in wet and washdown areas. IP69K rated sensors are essential.
- Automotive: Part verification in assembly robots, monitoring component feeds, detecting vehicle presence on lifts or in automated systems.
Conclusion
The rectangular photoelectric sensor is far more than a simple geometric choice in sensor design. Its shape is a powerful engineering solution, delivering tangible benefits through a larger sensing aperture, superior mounting stability, inherent ruggedness, and natural beam-shaping capabilities. From exceeding alignment tolerance demands to reliably detecting the trickiest targets in the harshest conditions, the rectangular form factor proves its worth daily on the factory floor. When robust, reliable, and high-performance non-contact detection is paramount for automation success, the rectangular photoelectric sensor consistently delivers, solidifying its role as a foundational technology in modern industrial sensing. Its unique geometry continues to unlock precision and reliability where it matters most.