stronger photoelectric sensor
- time:2025-07-25 02:02:28
- Click:0
Stronger Photoelectric Sensors: Redefining Reliability in Modern Automation
Imagine a critical production line humming along at peak efficiency. Suddenly, a false trigger from a photoelectric sensor halts everything. Downtime costs mount, technicians scramble, and deadlines slip. This frustrating scenario highlights a crucial, often overlooked, demand in industrial automation: the need for genuinely stronger photoelectric sensors. But “stronger” in this context transcends mere brute force; it signifies sensors engineered for unwavering performance and resilience in the face of relentless industrial challenges.
For decades, photoelectric sensors have been the backbone of automation, detecting presence, absence, position, and distance of objects using light beams. While precision and sensing range were paramount, today’s harsh, high-demand environments demand more. The stronger photoelectric sensor represents an evolution – one focused on environmental toughness, electrical stability, longevity, and resistance to interference, ensuring consistent, reliable operation where ordinary sensors falter.
What Makes a Photoelectric Sensor “Stronger”?
Moving beyond basic detection capabilities, a robust photoelectric sensor is defined by several critical attributes that enhance its “strength”:
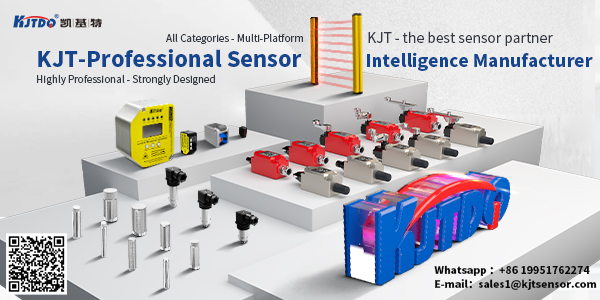
- Ruggedized Construction & Environmental Resilience: This is foundational. Stronger sensors boast:
- Superior Enclosures: Heavy-duty metal or exceptionally tough engineering plastics (like PBT) provide resistance against impact, crushing forces, and vibration common in material handling, packaging, or heavy machinery.
- Enhanced Sealing: Advanced IP ratings (IP67/IP68/IP69K) are non-negotiable. IP69K protection, in particular, signifies the ability to withstand high-pressure, high-temperature washdowns, making them ideal for food & beverage, pharmaceutical, and chemical processing. This environmental sealing protects against dust ingress, oils, coolants, and aggressive cleaning chemicals.
- Temperature Tolerance: Extended operating ranges (e.g., -40°C to +70°C or beyond) ensure reliable function in foundries, freezers, or outdoor applications where thermal cycling occurs.
- Electrical Stability & Noise Immunity: Electrical noise, voltage fluctuations, and surges are silent killers of sensor reliability. A stronger sensor incorporates:
- Robust Circuitry: Designed to withstand voltage spikes, transients (surges), and drops without damage or erratic behavior.
- Advanced Noise Rejection: Immunity to electromagnetic interference (EMI) and radio frequency interference (RFI) is critical, especially near VFDs, motors, welders, or radio equipment. This prevents false triggers and signal corruption.
- Wide Voltage Ranges: Ability to operate reliably across broad DC voltage inputs (e.g., 10-30 VDC), accommodating unstable power supplies common in some industrial settings.
- Optical Excellence & Contamination Resistance: A strong beam and clear “vision” are essential:
- High-Power LEDs & Optics: Brighter LEDs provide greater excess gain, allowing the sensor to see through light contamination like dust, steam, or condensation on lenses, or detect objects at greater distances reliably. Precision optics ensure a stable, well-defined beam.
- Lens Design & Coatings: Anti-glare coatings, hydrophobic coatings (repelling water), and scratch-resistant lenses maintain optical clarity and performance over time despite harsh conditions.
- Advanced Algorithms: Some sensors employ background suppression techniques or sophisticated signal processing to ignore ambient light fluctuations or differentiate target objects from background interference more effectively.
- Long-Term Reliability & Connectivity: Strength is measured in years, not months:
- High MTTFd (Mean Time To Dangerous Failure): A key safety and reliability metric, especially for functionally safe applications requiring SIL or PL ratings. A high MTTFd indicates a lower probability of dangerous failure over the sensor’s operational life.
- Durable Connectors & Cabling: M12 connectors with secure locking and rugged, oil-resistant PUR cabling prevent connection failures and cable damage, common points of weakness.
- IO-Link Capability: While not solely about ruggedness, IO-Link integration enhances “strength” by enabling remote diagnostics, parameter setting, and condition monitoring. This proactive insight allows predictive maintenance, preventing unexpected failures and maximizing uptime – a crucial aspect of operational strength.
Why Demand Stronger Photoelectric Sensors?
The push for more rugged photoelectric sensors isn’t arbitrary; it’s driven by tangible operational imperatives:
- Minimizing Costly Downtime: Sensor failure is a primary cause of unplanned production stoppages. Stronger sensors fail less often, directly boosting overall equipment effectiveness (OEE) and saving significant revenue lost during downtime.
- Reducing Maintenance Burden: Sensors constantly needing cleaning, repositioning, or replacement drain maintenance resources. Durable sensors require less frequent intervention, freeing up technicians and lowering lifecycle costs.
- Ensuring Safety: In safety-critical applications (e.g., light curtains for machine guarding perimeter detection, safety door monitoring), sensor reliability is paramount. Failure here can have severe consequences. High MTTFd and proven resilience are essential.
- Expanding Application Scope: Environments previously deemed too harsh – intense washdown, extreme temperatures, heavy vibration zones, areas with significant EMI – become viable with tougher sensors, unlocking new automation possibilities.
- Improving Product Quality: Consistent, reliable detection prevents errors in positioning, counting, or assembly that could lead to defective products or process inefficiencies.
Selecting the Strongest Photoelectric Sensor for Your Needs
When specifying a sensor, move beyond basic function and range. Ask the critical questions:
- What are the environmental hazards? (Chemicals, washdown pressure/temperature, dust levels, operating temps, impact/vibration risk)
- What is the electrical environment like? (Presence of VFDs, large motors, welding equipment, potential for power surges?)
- What are the consequences of failure? (Safety critical? High downtime cost?)
- Is remote monitoring or configuration beneficial? (IO-Link requirement?)
- What are the industry or safety standards that must be met? (e.g., IP69K, specific material approvals like FDA, SIL/PL ratings)
Prioritize sensors engineered explicitly for industrial durability. Look for certifications like IP69K, wide temperature ratings, high vibration/shock resistance specs, explicit EMI/RFI immunity claims, and high MTTFd values relevant to your safety needs. Reputable manufacturers invest heavily in testing (temperature cycling, shock/vibration, ingress protection, EMC) to validate the “strength” of their offerings.
The Future is Resilient
The evolution towards industrial-grade photoelectric sensors that are fundamentally stronger is not a luxury; it’s a necessity for modern, efficient, and reliable automation. As factories become smarter, faster, and operate in increasingly demanding conditions, the resilience of core components like sensors becomes a critical competitive advantage. Investing in sensors built to withstand the test of their environment ensures smoother operations, protects your bottom line, and provides the robust foundation required for the automated future. The strongest sensor isn’t just about detection; it’s about unwavering dependability where it matters most.