laser photo sensor
- time:2025-07-25 00:10:16
- Click:0
Laser Photo Sensors: Unlocking Precision in the World of Light Sensing
Imagine a factory floor where robotic arms move with millisecond precision, or a conveyor belt sorting millions of items flawlessly. Behind this seamless operation often lies a critical, unsung hero: the laser photo sensor. These sophisticated devices harness the power of focused light to detect objects, measure distances, and ensure processes run smoothly, safely, and efficiently. Understanding their workings is key to appreciating their transformative impact across countless industries.
At its core, a laser photo sensor (often called a laser photoelectric sensor) is a type of photoelectric sensor. It operates on a fundamental principle: it emits a highly focused, coherent beam of laser light towards a target and then detects either the presence of that beam (if interrupted) or its reflection. The core distinction from standard photoelectric sensors lies precisely in this coherent, collimated laser beam. This focus offers significant advantages:
- Exceptional Precision & Small Spot Size: The tight, narrow beam allows for detecting very small objects or precise edges that diffuse light sources might miss. This is crucial in applications like micro-component assembly or high-resolution positioning.
- Long Sensing Ranges: The coherent nature of laser light minimizes dispersion over distance. This enables reliable detection at ranges far exceeding those possible with standard LED-based sensors, sometimes reaching tens of meters.
- Improved Signal-to-Noise Ratio: The intense, focused beam provides a strong signal for the receiver, making these sensors highly resistant to interference from ambient light – a common challenge in industrial environments.
- Accurate Alignment: The visible (often red) laser spot allows for easy and precise alignment during installation and troubleshooting, reducing setup time significantly.
How Does a Laser Photo Sensor Work?
The fundamental operation involves three key components integrated within the sensor housing:
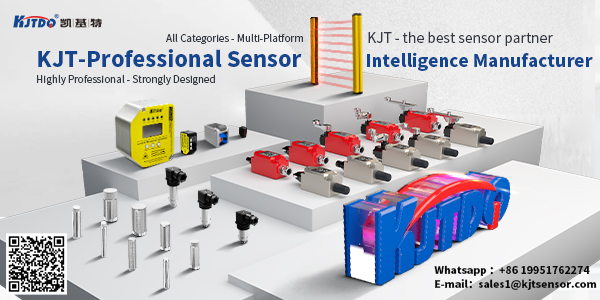
- Laser Emitter (Diode): This generates the coherent, monochromatic laser beam. Red lasers (e.g., 650 nm) are common for visibility and cost, but infrared (IR) is also widely used for specific applications or where the visible beam might be distracting.
- Receiver: This is typically a photodiode or phototransistor designed to be sensitive to the wavelength of the emitted laser light.
- Control Circuitry: This sophisticated electronics package processes the signal from the receiver, comparing it against thresholds to determine the output state (ON/OFF).
Laser photo sensor apply several detection modes, chosen based on the application:
- Through-Beam (Opposed Mode): The emitter and receiver are housed in separate units facing each other. An object is detected when it interrupts the beam traveling between them. This mode offers the longest possible range and highest reliability but requires installing two physical units. Ideal for counting small parts at high speed or detecting transparent objects.
- Retroreflective Mode: The emitter and receiver are housed together. The emitted beam strikes a specialized reflector (like a prismatic reflector or reflective tape) placed opposite the sensor and bounces directly back to the receiver. An object breaks this reflected beam, triggering detection. This simplifies wiring compared to through-beam but requires mounting a reflector. Excellent for pallet detection or conveyor entry/exit points.
- Diffuse (Proximity) Mode: Here, both emitter and receiver are in a single unit. The emitted beam strikes the target object. The sensor detects the diffused reflection of the laser light bouncing off the object back towards the receiver. Detection range is generally shorter than the other modes and depends heavily on the target’s color, reflectivity, and surface texture. Widely used for object presence on conveyors, level control, or detecting non-reflective objects without needing a separate reflector.
Where Laser Precision is Indispensable
The unique capabilities of laser photo sensors make them indispensable in demanding environments:
- Industrial Automation & Manufacturing: Precise positioning of components on assembly lines, high-speed counting of small parts (pills, electronic components), web edge guiding control, fill level detection in transparent bottles, robot cell safety curtains.
- Logistics & Material Handling: Pallet detection, package dimensioning and sorting on high-speed conveyors, presence verification at loading docks, automatic door operation.
- Packaging Machinery: Label placement verification, cap detection on bottles, carton sealing confirmation, film registration control.
- Elevator & Escalator Systems: Door safety monitoring, leveling control, passenger detection.
- Medical & Laboratory Equipment: Precise fluid level sensing, microplate handling, component positioning in diagnostic devices.
- Semiconductor Manufacturing: Ultra-precise wafer positioning and handling in cleanroom environments.
Choosing the Right Sensor: Key Considerations
Selecting the optimal laser photo sensor requires evaluating several factors:
- Application Need: What exactly needs detecting? (Presence, size, distance, transparency?)
- Required Sensing Range & Spot Size: How far away is the target? How small is the feature needing detection?
- Target Properties: What is the material, color, surface finish (shiny, matte)? Does it reflect well? Is it transparent?
- Operating Environment: Dust, moisture, temperature extremes, vibration, ambient light levels? (Look for appropriate IP ratings - Ingress Protection).
- Detection Mode: Which operational mode (Through-Beam, Retroreflective, Diffuse) best suits the physical constraints and goal?
- Output Type: Is a simple ON/OFF digital signal (PNP/NPN) sufficient, or is an analog output (e.g., for distance measurement) needed? Some advanced models offer analog outputs proportional to the distance or reflected signal intensity.
- Special Features: Time-of-Flight (ToF) capabilities for distance measurement, background suppression for reliable detection against busy backgrounds, synchronization features to avoid crosstalk in dense sensor arrays.
Why Laser Sensors Often Prevail
While other sensor types exist (inductive, capacitive, ultrasonic), laser photo sensors offer a compelling combination. They provide non-contact detection, exceptional precision and range capabilities, and excellent resistance to environmental interference like dust or light. While cost may be slightly higher than basic photoelectric sensors, the enhanced performance, reliability, and reduced downtime often deliver a significant return on investment in complex or demanding applications. Their ability to handle tasks involving transparent objects, small targets, or long ranges is often unmatched.
From the intricate dance of robotics to the smooth flow of packaging lines, laser photo sensors are fundamental elements enabling modern automation. Their focused beam cuts through complexity, providing the reliable, high-precision detection that powers efficiency and safety across a staggering array of industries. Understanding their principles and capabilities is the first step to harnessing their power in optimizing your own processes.