ifm capacitive proximity sensor
- time:2025-07-12 03:10:04
- Click:0
Unlock Precision Detection: Mastering IFM Capacitive Proximity Sensors
In the intricate dance of modern industrial automation, precise and reliable detection is non-negotiable. Whether it’s ensuring bottles are filled to the correct level, verifying the presence of packaging material, or safeguarding against spills and overflows, sensors are the silent sentinels. Among these, ifm capacitive proximity sensors stand out as versatile and robust solutions, particularly adept at handling challenges where other sensor types falter. Understanding their operation, strengths, and optimal applications is key to unlocking significant efficiency and reliability gains on your production floor. IFM, a global leader in industrial automation, offers a range of capacitive sensors renowned for their performance and durability.
At their core, capacitive proximity sensors operate on a simple yet powerful principle. Unlike their inductive counterparts which detect metallic objects, capacitive sensors sense changes in an electrical field. They contain an oscillator circuit that generates a high-frequency electromagnetic field emanating from their active face. When any material (solid, liquid, granular, or powder) enters this field, it causes a detectable change in the field’s capacitance. This change triggers the sensor’s output circuit, signaling the presence of the target. This fundamental mechanism grants capacitive sensors their unique versatility.
What truly sets ifm capacitive proximity sensors apart? IFM engineers these sensors to excel in demanding industrial environments. Key advantages include:
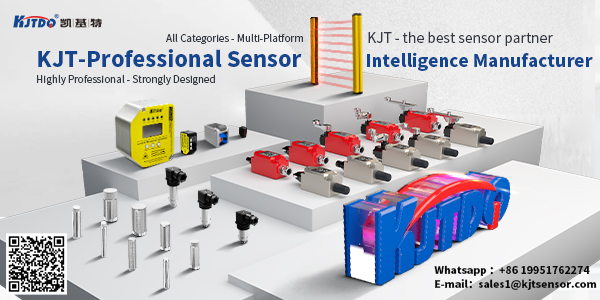
- Material Agnostic Detection: Their core strength. They reliably detect a vast array of non-metallic materials – plastics, glass, wood, cardboard, paper, oils, water, adhesives, grains, powders, and even materials through thin non-metallic walls. This makes them indispensable on lines handling diverse product packaging.
- Robust Performance in Challenging Conditions: Equipped with durable stainless steel or robust plastic housings (often PBT/PPS), IFM capacitive sensors withstand harsh realities: dust, dirt, moisture, aggressive cleaning agents, and wide temperature fluctuations. Many feature exceptional temperature stability, minimizing drift and ensuring reliable readings even in extreme environments.
- Overcoming Surface Contaminants: A significant advantage for food & beverage or pharmaceutical applications. They can reliably detect levels of liquids like milk, juice, or syrup, even when significant foam or residue builds up on tank walls or sensor faces – a scenario where ultrasonic sensors or simple float switches often struggle.
- Precise Level Control: Their ability to detect liquids and bulk solids through container walls makes them ideal for level monitoring in tanks, silos, and hoppers, preventing overflows or dry running. IFM offers variants specifically tailored for these critical tasks.
- Advanced Features: Modern IFM capacitive sensors often incorporate IO-Link communication, enabling remote configuration, real-time diagnostic data access (operating hours, temperature, switch cycles), and simplified parameter setting. Features like extra-long sensing ranges, adjustable sensitivity (crucial for tuning out background interference), and specialized hygienic designs with FDA-compliant materials further enhance their applicability.
Typical Applications Showcasing IFM Capacitive Sensor Prowess:
- Packaging Industry: Detecting plastic bottles, glass containers, cardboard boxes, foil lids, label presence, and adhesive layers on production lines.
- Food & Beverage Processing: Monitoring levels of liquids (with/without foam), pastes, powders, grains, and sauces in tanks, mixers, and filling machines. Critical for ensuring consistent product quality and preventing spills.
- Woodworking & Furniture: Detecting wood panels, MDF, plywood, sawdust levels, and glue application points.
- Chemical & Pharmaceutical: Level control of aggressive chemicals, solvents, or pharmaceutical solutions within sealed containers; verifying the presence of plastic or glass vials.
- Bulk Material Handling: Monitoring levels of plastic pellets, granules, flour, sugar, sand, and other bulk solids in silos, bins, and conveyors.
- General Automation: Presence detection of non-metallic parts, liquid leak detection, paper roll monitoring, and end-of-roll sensing.
Selecting and Implementing Your IFM Capacitive Sensor:
Choosing the right ifm capacitive proximity sensor ensures optimal performance:
- Target Material: Be specific about what you need to detect. Is it a liquid, granular solid, plastic part, or film?
- Sensing Distance: Capacitive sensors have defined nominal sensing ranges (Sn). Consider the required distance and potential temperature influences. IFM datasheets provide clear specifications, often including reduction factors for various materials.
- Environment: Assess exposure to dust, moisture, cleaning chemicals, temperature extremes, and mechanical stress. Choose the appropriate housing material (e.g., stainless steel V4A/316L for harsh chemical or washdown areas, PBT/PPS for general use).
- Mounting: Ensure correct mounting (flush or non-flush) as specified. Surrounding metallic objects can influence the sensing field.
- Electrical Requirements: Match the output type (PNP/NPN, NO/NC), voltage rating, and current load to your control system. Consider the convenience of IO-Link models for advanced functionality and diagnostics.
- Special Requirements: Need detection through thick walls? Hygienic design? Resistance to heavy vibration? IFM often offers specialized variants (e.g., the MT or Y series) for these demanding scenarios. Features like high resistance to coating buildup are vital in sticky applications.
Tuning for Success: Most ifm capacitive proximity sensors feature a potentiometer or teach-in button for adjusting sensitivity (Switching Threshold). This is crucial. Fine-tuning allows the sensor to reliably detect the desired target material while ignoring background interference from the mounting bracket, conveyor structure, or adjacent materials. Take the time to properly adjust the sensitivity during commissioning for trouble-free operation.
IFM capacitive proximity sensors are powerful tools in the automation engineer’s toolkit. Their unique ability to detect virtually any material, combined with IFM’s commitment to robustness, reliability, and advanced features, makes them the go-to solution for countless detection challenges, particularly involving non-metallics and liquids. By understanding their operating principles, strengths, and selection criteria, you can leverage these sensors to significantly enhance process reliability, efficiency, and safety on your production line. When precise, versatile, and reliable non-metallic detection is paramount, ifm capacitive sensors consistently deliver.