inductive magnetic sensor
- time:2025-07-11 02:13:41
- Click:0
The Inductive Edge: How Magnetic Sensors Power Modern Automation
Imagine a machine seamlessly assembling parts, a car sensing gear position for smooth shifting, or factory robots moving safely around humans. Hidden within these marvels of modern engineering are tiny, unsung heroes: inductive magnetic sensors. These robust and highly reliable devices are fundamental to countless applications requiring contactless position sensing, speed detection, or proximity detection. Understanding their operation and advantages reveals why they are a cornerstone of industrial automation and beyond.
At their core, inductive magnetic sensors work by detecting changes in a magnetic field, translating that change into an electrical signal. Unlike sensors relying on light or physical contact, they excel in harsh environments – think oil, dust, dirt, or vibration – where traditional methods falter. Their operation hinges on a fundamental principle: electromagnetic induction.
Here’s a simplified breakdown of their working principle:
- The Oscillator & Coil: Inside the sensor lies an electronic oscillator circuit connected to a wire coil wound around a ferrite core. This coil generates a high-frequency, alternating electromagnetic field that extends beyond the sensor’s active face.
- The Magnetic Field Interaction: When a ferromagnetic target (like iron or steel) enters this field, it causes perturbations. For inductive proximity sensors (a major subtype), the target induces eddy currents within itself. These eddy currents generate their own opposing magnetic field.
- Change in Inductance: The interaction (eddy current generation or simple ferromagnetic attraction) alters the effective inductance (L) of the sensor’s coil circuit. This is the inductive aspect.
- Signal Processing: The sensor’s built-in electronics continuously monitor the amplitude or frequency of the oscillator circuit. The change in inductance directly affects this oscillation.
- Output Trigger: Once the change reaches a predefined threshold (indicating the target is close enough), the sensor triggers its output. This output is typically a simple on/off switch signal (digital) used to control machinery, count objects, or signal position.
Why Choose Inductive Magnetic Sensors? Key Advantages
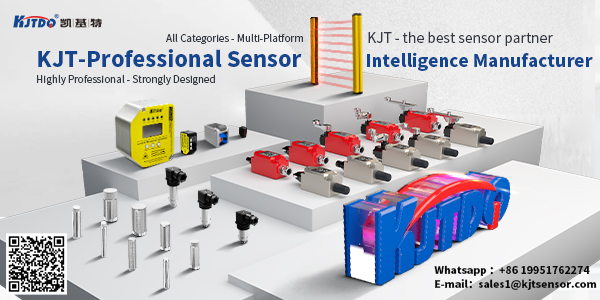
- Exceptional Robustness: Their non-contact nature and sealed construction (IP67/IP68 ratings are common) make them highly resistant to dirt, dust, moisture, oils, and chemicals. They are workhorses in demanding industrial settings like manufacturing plants, heavy machinery, and automotive underhood applications.
- No Physical Wear: Since there’s no contact between the sensor and the target, inductive proximity sensors experience virtually zero mechanical wear, leading to incredibly long lifespans and minimal maintenance.
- High Switching Frequencies: Capable of detecting targets moving at very high speeds, they are ideal for speed detection tasks like monitoring shaft rotations or conveyor belt speeds.
- Intrinsically Simple & Reliable: The fundamental operating principle leads to a relatively simple design, translating to high reliability and consistent performance.
- Cost-Effective: For applications needing robust position sensing or object detection of metallic targets, they offer an excellent balance of performance, durability, and price.
Differentiating Inductive from Other Sensor Types
It’s crucial to understand what inductive magnetic sensors don’t do:
- Not Hall Effect Sensors: While both detect magnetic fields, Hall sensors rely on the Hall effect in semiconductors and primarily sense the presence and strength of a permanent magnet’s field. Inductive magnetic sensors generate their own field and react to the disturbance caused by any ferromagnetic material, not requiring an attached magnet (though magnets are sometimes used as targets).
- Not Capacitive Sensors: Capacitive sensors detect the presence of any material (metal, plastic, liquid, wood) by measuring changes in capacitance. Inductive sensors are specifically tuned for conductive metals, particularly ferrous metals.
- Not Optical Sensors: They are immune to ambient light conditions, smoke, or dust that would typically disrupt optical sensors (like photoelectric eyes).
Ubiquitous Applications: Sensing the World Around Us
The versatility of inductive magnetic sensors ensures their presence in a staggering array of industries:
- Factory Automation: The undisputed king for proximity detection: sensing robotic arm positions, detecting metal parts on conveyors, monitoring cylinder positions in pneumatic/hydraulic systems, and counting metallic objects.
- Automotive: Critical for position sensing of crankshafts, camshafts, transmissions, and throttle valves. Used in anti-lock braking systems (ABS) for wheel speed detection. Also found in seat position detection, tailgate latches, and EV charging system interlocks.
- Consumer Electronics: Detecting flip/slide mechanisms in phones and laptops, sensing lid closure on appliances (e.g., washing machines).
- Material Handling & Logistics: Detecting metal pallets, monitoring conveyor belt speeds, and ensuring correct positioning in sorting systems.
- Aerospace: Used in landing gear position sensing, door closure detection, and engine monitoring systems where reliability is paramount.
- Machine Tooling: Precise position sensing for tool changers, spindle positioning, and workpiece clamping.
Looking Ahead: Continuous Improvement
While mature technology, inductive magnetic sensors continue to evolve. Advancements focus on:
- Miniaturization: Shrinking sensor sizes to fit into increasingly compact devices.
- Increased Sensing Distances: Achieving reliable detection at greater ranges from the target.
- Enhanced Immunity: Further improving resistance to electromagnetic interference (EMI) in electrically noisy environments.
- Integration: Combining sensing elements with more sophisticated on-board signal processing and diagnostics (IO-Link compatibility is a growing trend).
- Specialized Form Factors: Developing sensors specifically designed for unique mounting challenges or target types.
From the factory floor to the family car and countless devices in between, inductive magnetic sensors provide the invisible, reliable feedback essential for precision, safety, and efficiency. Their unique blend of ruggedness, contactless operation, and cost-effectiveness ensures they will remain a vital sensing technology, quietly shaping the automated world around us for years to come. As demands for smarter machines and harsher operating conditions grow, so too will the capabilities of these indispensable components.