ir proximity sensor distance
- time:2025-07-11 00:28:13
- Click:0
Mastering IR Proximity Sensor Distance: Precision, Factors & Applications
We interact with them dozens, perhaps hundreds, of times a day, often without a second thought. That automatic faucet switching on as you wave your hand? The elevator door pausing safely? Your smartphone screen dimming mid-call? The silent sentinel enabling these interactions is typically an Infrared (IR) Proximity Sensor. At the heart of its functionality lies its ability to detect distance – understanding how far an object is from its lens. Mastering IR proximity sensor distance detection is crucial for reliable performance across countless applications. This article delves into the science, influencing factors, and optimization strategies for this fundamental capability.
The Fundamental Mechanism: Light, Reflection, and Calculation
At its core, an IR proximity sensor operates using a simple yet effective principle:
- Infrared Light Emission: An integrated Infrared Light Emitting Diode (IR LED) emits a beam of invisible near-infrared light (typically in the 850nm or 940nm wavelength range). This light is invisible to the human eye.
- Reflection and Reception: When an object enters the sensor’s field of view, a portion of this emitted IR light reflects off its surface.
- Signal Conversion and Analysis: A photodetector (like a photodiode or phototransistor) within the sensor detects this reflected light and converts it into an electrical current. The intensity of this current is proportional to the amount of reflected light reaching the detector.
- Distance Inference: The core principle for determining distance relies on the inverse-square law: the intensity of reflected light diminishes rapidly as the distance to the reflecting object increases. In simpler terms, a closer object reflects significantly more light back to the sensor than a distant one. By precisely measuring the strength of the received signal (photocurrent), the sensor (or its connected system) can estimate the object’s distance. More advanced sensors, especially those designed for longer ranges or higher precision, often employ triangulation principles for even more accurate distance calculation.
Key Factors Influencing Distance Detection Accuracy
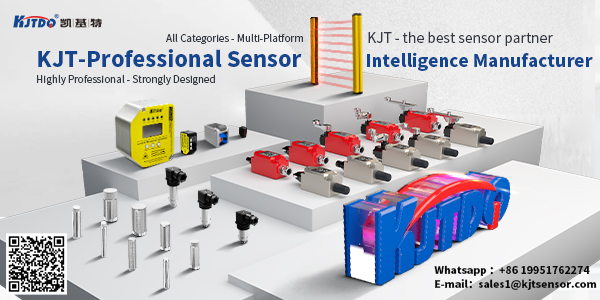
While the underlying principle seems straightforward, several critical factors influence the accuracy and effective range of IR proximity sensor distance measurement:
- Target Object Characteristics:
- Reflectivity: This is arguably the most significant external factor. Materials like glossy white plastic or metal reflect IR light exceptionally well, yielding a strong signal and enabling detection at longer distances. Conversely, dark, matte, soft, or transparent materials (like dark fabric, black rubber, or glass) absorb or scatter most of the IR light, resulting in a weak or non-existent return signal. Calibration must often account for expected surface types.
- Size: Larger objects present a bigger target to reflect light, generally producing a stronger return signal than smaller objects at the same distance.
- Angle: The angle at which the IR beam hits the object (angle of incidence) and the angle at which the reflection is captured (angle of reflection) significantly impact the received signal strength. Objects directly facing the sensor perpendicularly reflect the most light back towards the detector.
Ambient Light Interference: Environmental IR pollution is a major challenge. Sunlight, incandescent bulbs, and other heat sources emit significant amounts of infrared radiation. This ambient IR light can flood the sensor’s photodetector, overwhelming the relatively weak reflected signal from the target object. This “noise” drastically reduces the effective range and accuracy. Sophisticated sensors employ techniques like modulation (pulsing the IR LED at a specific frequency) and synchronous demodulation (tuning the receiver to only detect that specific frequency) to filter out DC ambient light and other noise sources significantly. Selecting sensors with a higher signal-to-noise ratio (SNR) is vital for robust operation in bright environments.
Sensor Design and Optics:
- Emitter Power: A stronger IR LED output generates a more intense beam, leading to potentially stronger reflections over longer distances.
- Detector Sensitivity: A highly sensitive photodetector can detect weaker reflected signals.
- Optical Design: The lenses covering the IR LED and photodetector focus the emitted beam and shape the receiver’s field of view (FOV). Careful optical design ensures optimal overlap between the emitted cone and the receiver’s view (especially critical for triangulation sensors) and minimizes stray light paths that could cause false triggers. A narrower FOV often enables longer detection ranges but covers less area, while a wider FOV covers more area but typically has shorter range.
- Wavelength: 940nm IR LEDs are generally less susceptible to interference from ambient light (like sunlight) than 850nm LEDs, as the Earth’s atmosphere absorbs some solar IR at 940nm. However, 850nm LEDs are often slightly more efficient.
- Sensor Electronics and Processing: The quality of the analog front-end (amplifying and conditioning the weak photodetector signal) and the algorithms used to convert the photocurrent into a distance value are critical. Noise reduction techniques, temperature compensation circuits, and intelligent calibration routines are essential for stable and accurate distance readings.
Practical Applications Leveraging Distance Sensing
The ability to measure or detect proximity based on distance underpins a vast array of applications:
- Industrial Automation & Safety: Precision object detection on assembly lines, robotic arm collision avoidance, material level sensing (e.g., bins, tanks), and safety guards preventing machine operation if personnel are too close.
- Consumer Electronics: Automatic screen on/off during phone calls (saving battery), touchless gesture control, automatic faucets, soap dispensers, hand dryers, presence detection in laptops/smart displays.
- Robotics & Drones: Obstacle avoidance, cliff detection (preventing falls), terrain following, docking assistance.
- Building Automation: Automatic door openers (ensuring safe passage), lighting control (turning lights on/off based on occupancy), smart toilets.
- Vehicular Systems: Park assist sensors (often using ultrasonic primarily, but IR can be used in some contexts), cabin occupancy detection.
- Appliance Control: Touchless control panels on ovens, microwaves, etc.
Optimizing for Reliable Distance Measurement
To achieve the best possible IR proximity sensor distance performance:
- Select the Right Sensor for the Job: Match the sensor’s specified range, sensitivity, FOV, and immunity to ambient light with your specific application environment and target object properties. Consider sensors with built-in algorithms providing calibrated distance outputs.
- Calibrate in Context: Calibrate the sensor using representative objects under conditions (especially ambient light levels) resembling the actual operating environment.
- Manage Ambient Light: Whenever possible, shield the sensor from direct, intense ambient light sources. Utilize sensors with strong ambient light rejection capabilities (high SNR, modulation/demodulation).
- Optimize Sensor Placement: Ensure the emitter beam can effectively illuminate the target area, and the detector has a clear line of sight for reflections. Maintain alignment. Avoid mounting near reflective surfaces that could cause crosstalk within the sensor itself.
- Understand Limitations: Acknowledge that IR sensors work best with diffusely reflective objects within their specified range. Avoid applications requiring distance detection on highly transparent, deeply black, or polished metal surfaces without significant testing and validation. Surface texture also plays a role – rough surfaces scatter light differently than smooth ones.
- Signal Processing: Implement effective filtering (e.g., moving averages) on the output signal to reduce noise and jitter. Adaptive thresholding can improve detection consistency as ambient conditions fluctuate.
The precision offered by IR proximity sensors in gauging distance is both fascinating and foundational. Its seemingly simple operation conceals a complex interplay of physics, optics, and electronics. By thoroughly understanding the factors that influence distance