flush non flush sensor
- time:2025-07-10 03:58:49
- Click:0
Flush vs. Non-Flush Sensors: Mastering Installation for Optimal Performance
Imagine this: you’ve meticulously installed a new sensor on your high-speed packaging line, confident it will detect every carton flawlessly. Yet, inexplicably, it misses critical faults or triggers false alarms, grinding production to a halt. The culprit? It might not be the sensor itself, but how it was mounted. Understanding the crucial distinction between flush and non-flush installation is often the key to unlocking reliable, high-performing sensing in demanding industrial environments. This choice fundamentally impacts sensing range, reliability, and application suitability.
Decoding the Mounting Mystery: Flush vs. Non-Flush
At its core, the flush vs. non-flush designation refers to how the active sensing face of a proximity sensor (commonly inductive or capacitive) is positioned relative to the surrounding mounting surface. This seemingly small detail has significant operational consequences:
- Flush Mounting (Shielded Sensors):
- Installation: The sensor is mounted so that its sensing face sits perfectly level (flush) with the surface of the mounting bracket or surrounding metal.
- Key Characteristic: The sensor incorporates an internal electromagnetic shield (often a metal band around the sensing face).
- Effect: This shield focuses the sensing field directly in front of the sensor face. It significantly reduces lateral sensitivity.
- Primary Advantage: Immunity to nearby metal. Flush-mountable sensors are ideal when installed near other metal structures (like brackets, machine frames, or adjacent sensors). The shielding prevents the sensor from accidentally detecting this surrounding metal instead of its intended target.
- Trade-off: Reduced Sensing Range. The focused field inherently limits the maximum distance at which the sensor can reliably detect a target. They typically offer shorter nominal sensing ranges (Sn) compared to non-flush versions.
- Visual Clue: These sensors can be mounted “embedded” in metal without causing interference.
- Non-Flush Mounting (Unshielded Sensors):
- Installation: The sensor protrudes slightly from the mounting surface. Its sensing face is not surrounded by metal.
- Key Characteristic: They lack the internal electromagnetic shield around the sensing face.
- Effect: The sensing field extends both forward and radially around the sensing face. This creates a larger, more expansive detection zone.
- Primary Advantage: Extended Sensing Range. Unshielded sensors offer a significantly longer nominal sensing range (Sn) compared to their shielded, flush-mountable counterparts. This makes them suitable for applications requiring detection at greater distances.
- Trade-off: Susceptibility to surrounding metal. Because the field extends radially, metal objects adjacent to the sensor (mounting nuts, brackets, machine frames) can interfere, potentially causing false triggering or reduced effective range. They require a specific minimum clearance zone around the sensor body (usually specified by the manufacturer as 1x or 2x the sensor diameter) free of metal to operate correctly.
- Visual Clue: These sensors must protrude and have clearance space around them when mounted; embedding them flush in metal will cause malfunctions.
Why Does Flush vs. Non-Flush Matter So Much? Choosing Wisely
Selecting the wrong mounting type is a common source of sensor failure, downtime, and frustration. Getting it right is critical for:
- Reliable Detection: Eliminating false positives (detecting something it shouldn’t) and false negatives (missing the intended target).
- Maximizing Equipment Uptime: Preventing unnecessary stoppages due to sensor errors.
- Optimizing Performance: Ensuring the sensor operates at its specified range and sensitivity.
- Preventing Premature Failure: Incorrect installation can cause physical damage or electrical issues over time.
Applications: Where Flush and Non-Flush Shine
Understanding typical applications highlights the practical importance:
Flush-Mountable (Shielded) Sensor Applications:
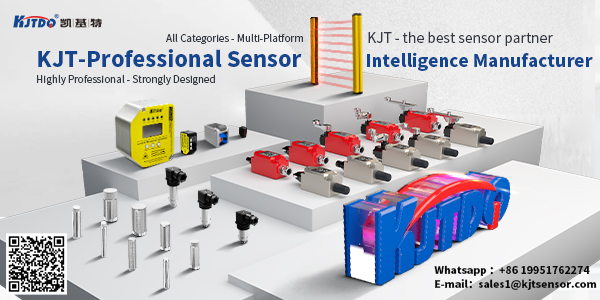
Tight Spaces: Where sensors are mounted close together or near structural metal. Think robotic arms or compact assembly stations.
Embedded Mounting: When the sensor needs to be protected or mounted within a metal housing or frame. Common in valves or actuators.
Detection Through Non-Metallic Materials: Flush capacitive sensors are excellent for detecting fill levels through plastic or glass tank walls without being influenced by the mounting bracket behind them.
Metal Backgrounds: Applications where the target passes close to a metal backing plate or conveyor structure. The shielding prevents detection of the background.
High-Vibration Environments: The flush installation often provides better mechanical stability.
Non-Flush (Unshielded) Sensor Applications:
Long-Range Detection: Any application requiring the maximum possible sensing distance from the target. Monitoring object presence on wide conveyors is a classic example.
Situations with Ample Mounting Clearance: Where there’s sufficient space around the sensor to meet the required metal-free zone. Overhead detection points often meet this criteria.
Detecting Smaller Targets: The larger, less focused field might make it easier to detect very small objects within its extended range zone.
Modern Flexibility: Sensors Bridging the Gap
Recognizing the importance of installation flexibility, many modern sensor manufacturers now offer proximity sensors designed for both flush and non-flush mounting, sometimes termed “factor 1” sensors. These hybrid designs incorporate shielding but achieve sensing ranges closer to traditional unshielded sensors. However, it’s crucial to consult the datasheet carefully. While offering versatility, the optimal performance (maximum range vs. best immunity) might still favor one mode over the other in extreme conditions. Understanding the datasheet specifications for sensing range (Sn) under both mounting conditions is essential.
Key Considerations for Selection Beyond Mounting Type
While flush vs. non-flush is paramount, it’s part of a broader selection process:
- Target Material: Inductive sensors detect metals; capacitive sensors detect almost any material (including liquids, powders, plastics, wood).
- Required Sensing Range (Sn): Always confirm the effective range under your chosen mounting condition from the datasheet.
- Environmental Factors: Temperature extremes, humidity, dust, chemicals, washdown requirements (IP rating), and potential impacts. IP67/IP68/IP69k ratings are vital for harsh industrial or food-grade environments.
- Electrical Specifications: Operating voltage (e.g., 10-30V DC), output type (PNP/NPN, NO/NC), current rating, and connection type (cable or connector).
- Mounting Constraints: Available space, material of the mounting surface, and proximity to potential interference sources.
Implementing with Confidence: Best Practices
- Read the Datasheet First: Never assume. Verify the sensor’s specifications, especially the sensing range for your desired mounting method (flush or non-flush) and the required clearance zones for non-flush models.
- Respect Clearance Zones: For non-flush (unshielded) sensors, meticulously ensure the specified radial clearance (typically 1x or 2x the sensor diameter) is free of any metal. Even a washer or bolt head too close can cause interference.
- Secure Mounting: Ensure the sensor is firmly fixed to prevent vibration-induced movement or damage. Proper torque on mounting nuts is crucial.
- Precision Alignment: Align the sensor correctly with its target path to ensure reliable detection within the specified operating range.
- Verify in Operation: After installation, rigorously test the sensor under all expected operating conditions to confirm reliable detection and the absence of false triggers.
The strategic choice between flush and non-flush sensor mounting is far more than a mechanical detail; it’s a fundamental decision impacting performance, reliability, and system uptime. By deeply understanding the principles of electromagnetic field behavior – how shielding focuses the field for nearby immunity in flush mounting, and its absence enables longer range in non-flush mounting – engineers and technicians can select and install the optimal sensor for the task.