displacement position and proximity sensors
- time:2025-07-09 00:21:13
- Click:0
Precision in Motion: How Displacement, Position, and Proximity Sensors Power Modern Automation
Imagine an assembly line where robotic arms assemble intricate electronics with sub-millimeter accuracy, or a high-speed train maintaining perfect alignment on its track. This remarkable precision hinges on a critical, often unseen, technology trio: displacement sensors, position sensors, and proximity sensors. These sophisticated devices form the sensory foundation of modern automation, manufacturing, and countless other industries. Understanding their distinct roles and capabilities is key to appreciating the invisible intelligence driving efficiency and innovation today.
While the terms are sometimes used loosely, displacement, position, and proximity sensors serve fundamentally different, though complementary, functions:
- Displacement Sensors: Measuring Movement
- Core Function: Displacement sensors measure the distance an object moves from a reference point – essentially, how far it has traveled along a straight line (linear displacement) or rotated (angular displacement). They provide continuous, dynamic feedback on movement.
- Principle & Types: They utilize diverse physical principles:
- LVDTs (Linear Variable Differential Transformers): Highly accurate displacement transducers using electromagnetic induction, ideal for demanding industrial metrology.
- Laser Displacement Sensors: Offer non-contact, high-speed, and high-resolution distance measurement using triangulation or time-of-flight principles.
- Potentiometers: Simple contact-based sensors providing voltage proportional to wiper position.
- Eddy Current Sensors: Detect conductive target displacement through induced eddy currents, excellent for vibrating or rotating machinery.
- Key Applications: Monitoring vibration in turbines, controlling hydraulic/pneumatic cylinder stroke, precision machining feedback, material thickness gauging, wear measurement in bearings.
- Position Sensors: Pinpointing Location
- Core Function: Position sensors determine the absolute or relative location of an object within a defined coordinate system or relative to a specific point. They answer “Where is the object?”
- Principle & Types:
- Encoders (Rotary & Linear): Provide digital or analog signals representing rotational angle or linear distance traveled. Absolute encoders give a unique position value even after power loss, while incremental encoders measure relative movement.
- Resolver: Robust analog devices similar to an LVDT but for rotational position, highly reliable in harsh environments.
- Magnetic Position Sensors (Hall Effect, AMR): Detect the presence and strength of magnetic fields to determine the linear or angular position of a magnet.
- GPS/GNSS: For global position tracking.
- Key Applications: Robot joint angle control, CNC machine tool axis positioning, valve position feedback, antenna pointing, stage positioning in semiconductor manufacturing, vehicle navigation.
- Proximity Sensors: Detecting Nearby Presence
- Core Function: Proximity sensors detect the presence (or absence) of an object within a defined sensing range without physical contact. They answer “Is an object nearby?” or “How close is it?”. They typically provide a simple on/off signal when an object enters the detection zone.
- Principle & Types: Rely on non-contact detection methods:
- Inductive Proximity Sensors: Detect metallic objects by disturbing an electromagnetic field. The backbone of factory automation for metal detection.
- Capacitive Proximity Sensors: Detect both metallic and non-metallic objects (liquids, plastics, wood) by altering an electrostatic field.
- Ultrasonic Proximity Sensors: Measure distance or detect presence using sound wave reflection times. Effective for diverse materials and challenging environments (dust, fog).
- Photoelectric Sensors: Use light beams (visible, infrared) to detect object presence, interruption, or reflection. Versatile for many shapes, sizes, and materials.
- Magnetic Proximity Sensors (Reed Switches): Detect the presence of a magnetic field, often used for door/window security or piston position in cylinders.
- Key Applications: Object detection on conveyors, part counting, level detection in tanks, security systems, end-of-travel detection in machinery, safety interlocks on guards.
The Synergy of Sensing: Precision, Safety, and Efficiency
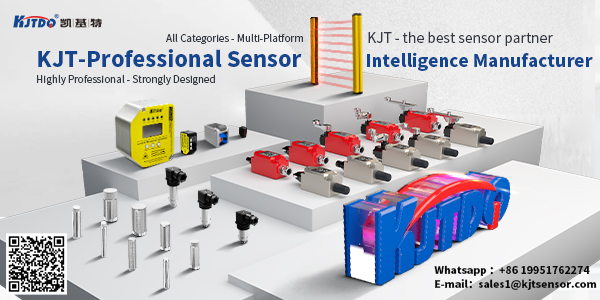
While distinct, these sensor categories often work in concert within complex systems. For instance:
- A robotic arm might use proximity sensors to safely detect nearby workers or objects (safety), position sensors (encoders) in its joints to know its exact configuration (location), and a displacement sensor (LVDT or laser) on its gripper to precisely measure how far it needs to close to grasp a part (movement distance).
- In an automated guided vehicle (AGV), position sensors (encoders on wheels, IMUs) track its movement and location within a facility, while proximity sensors (ultrasonic, lidar) continuously scan for obstacles to prevent collisions.
Choosing the Right Tool:
Selecting the optimal sensor type depends heavily on the specific requirements:
- What needs to be measured? Distance moved? Absolute location? Simple presence?
- Required Precision: Micron-level accuracy or just presence detection?
- Range: Millimeter detection or multi-meter distance?
- Environment: Exposure to oil, dust, vibration, extreme temperatures, or electromagnetic interference?
- Target Material: Metal, plastic, liquid? Magnetic?
- Contact vs. Non-contact: Can the sensor touch the object?
- Output Signal: Analog voltage/current for continuous measurement, or digital on/off for presence?
- Speed: How fast is the target moving or how quickly must detection occur?
Driving Innovation Across Industries
The pervasive application of displacement, position, and proximity sensors underpins advancements in:
- Industrial Automation: Foundational for robotics, CNC machining, assembly line control, and predictive maintenance.
- Automotive: Engine control (crankshaft/camshaft position), suspension control, driver assistance systems (parking sensors, adaptive cruise control using proximity/distance sensing), transmission control.
- Aerospace & Defense: Flight control surfaces, landing gear position, navigation, missile guidance.
- Consumer Electronics: Touchscreen position detection, hinge angle in foldable phones, vibration measurement.
- Medical Devices: Precision positioning in surgical robots, fluid level detection, patient monitoring equipment.
- Energy: Monitoring turbine shaft displacement, valve position control in refineries, pipeline inspection gauges.
From the subtle vibration monitoring ensuring a power plant’s safe operation to the precise alignment enabling smartphone screen manufacturing, displacement, position, and proximity sensors are the fundamental technologies translating the physical world into actionable data. Their continuous evolution in accuracy, reliability, miniaturization, and cost-effectiveness is pushing the boundaries of what’s possible in automation and control, making them indispensable tools in the relentless pursuit of efficiency, quality, and safety.