dual proximity sensor
- time:2025-07-09 00:07:11
- Click:0
Unlocking Efficiency: How Dual Proximosity Sensors Revolutionize Industrial Sensing
Imagine a critical production line suddenly halting because a single proximity sensor failed to detect a component’s presence. Downtime costs mount, efficiency plummets, and reliability is questioned. This vulnerability is precisely where dual proximity sensor configurations step in, transforming basic detection into a pillar of robust, intelligent automation. Far more than just ‘two sensors,’ this strategic setup is a sophisticated answer to demanding industrial challenges.
Single proximity sensors, though fundamental, have inherent limitations. They represent a single point of failure – if one malfunctions or misses a detection due to dirt, misalignment, or unexpected object variations, the entire process can be derailed. Their sensing range and positional accuracy might also be insufficient for complex or safety-critical applications. Dual-sensor systems, however, introduce redundancy and enhanced capabilities, effectively mitigating these risks and elevating performance.
The Core Advantages: Beyond Simple Redundancy
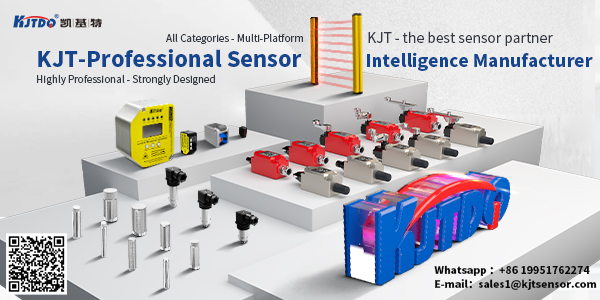
The implementation of dual proximity sensing delivers tangible, system-wide benefits crucial for modern operations:
- Enhanced Reliability & Safety Through Redundancy: This is the most fundamental strength. If one sensor in the pair fails or provides an ambiguous signal, the control system can leverage the reading from the second sensor. This prevents catastrophic failures and unplanned stops, especially vital in safety-critical applications like guarding hazardous machinery zones or ensuring robotic arm positioning during human interaction. Fail-safe operation becomes achievable.
- Superior Detection Accuracy & Resolution: Two sensors provide more positional information than one. Strategically placed, they can significantly boost sensing accuracy. For instance:
- Object Differentiation: Sensors placed on either side of a conveyor can reliably detect objects of varying heights or irregular shapes that a single, top-mounted sensor might miss.
- Edge Detection/Presence Confirmation: Positioned opposite each other, they can definitively confirm an object has fully passed a specific point or entered a processing zone, eliminating “false presence” or “false absence” signals common with single sensors near object edges.
- Distance Verification: In some configurations, comparing signals from two sensors can offer a rudimentary form of distance measurement or position verification beyond simple presence/absence.
- Expanded Coverage & Complex Geometries: A single sensor has a finite, often cone-shaped detection field. Deploying two sensors allows engineers to cover wider areas, monitor complex profiles, or detect objects approaching from multiple angles without resorting to more expensive and complex solutions like vision systems. This is invaluable for large machinery, wide conveyors, or intricate assembly stations.
- Robustness Against Environmental Factors: Mounting sensors in slightly different locations or utilizing different sensing principles (e.g., combining inductive and capacitive) within the dual setup makes the system less susceptible to common issues. Dirt accumulation affecting one sensor might not impact the second. Electromagnetic interference hitting one location might leave the other unaffected. This inherent resilience improves overall system uptime.
Real-World Industrial Applications
The versatility of dual proximity sensing makes it indispensable across numerous sectors:
- Robotics & Automated Assembly: Ensuring precise gripper positioning before closing, confirming part presence and orientation before insertion (e.g., using sensors on opposite sides of a fixture), and verifying tool changes reliably.
- Material Handling & Logistics: Detecting pallet presence at loading docks/stations using sensors at corners, verifying carton position on conveyors, confirming bin filling levels from multiple points, and monitoring for jams.
- Machine Safety: Creating robust safety light curtains or presence-sensing mats with redundant detection channels, or monitoring guard door closures from two distinct positions to prevent hazardous machine start-up.
- Packaging & Filling Lines: Verifying bottle/cap presence and alignment before capping or filling operations, detecting label position, and ensuring case sealing completeness.
- Automotive Manufacturing: Confirming precise component placement (e.g., engine blocks on assembly lines), verifying door/window positioning during automated installation, monitoring robotic welding paths for unexpected obstructions.
- Automated Parking Systems: Detecting vehicle presence accurately within parking bays or guiding vehicles using side-mounted sensors to prevent collisions.
Implementing Dual Sensor Systems Effectively
While powerful, deploying dual proximity sensors requires careful planning:
- Sensor Selection: Choose the right type (inductive, capacitive, photoelectric) and specific model based on the target object material, required sensing distance, environmental conditions (heat, dust, moisture), and required output type (NPN/PNP, NO/NC).
- Strategic Placement: The position and orientation of each sensor relative to the target object and to each other are paramount. Consider the detection field overlap, potential interference, accessibility for maintenance, and the specific detection goal (e.g., presence, edge, orientation).
- Logic Integration: The control system (PLC, microcontroller) must be programmed with appropriate logic to interpret the combined signals from both sensors. This might involve simple AND/OR gates for redundancy, or more complex routines for position verification or fault detection.
- Diagnostics & Maintenance: Ideally, the system should incorporate diagnostic features to alert operators if one sensor deviates significantly from its expected state or if discrepancies arise between the pair signals, enabling proactive maintenance and preventing masked failures.
Dual proximity sensor configurations represent a significant leap beyond basic object detection. By harnessing the power of redundancy, enhanced accuracy, wider coverage, and superior reliability, they provide the robust sensing foundation required for maximizing uptime, optimizing efficiency, and ensuring safety in increasingly sophisticated industrial environments. Moving beyond a single point of failure, this dual-sensing strategy unlocks new levels of performance and resilience crucial for modern automation.