capacitive type proximity sensor
- time:2025-07-08 02:28:03
- Click:0
Unseen Sensitivity: The Core Principles and Applications of Capacitive Proximity Sensors
That phone unlocking as you glance at it? The faucet turning on without a touch? The machine safeguarding your fingers? These modern conveniences often rely on an unseen technological marvel: the capacitive type proximity sensor. Operating without physical contact, these sensors detect the presence, absence, or composition of objects through subtle changes in an electrical field. Let’s delve into the fundamental principles, operational characteristics, and diverse applications that make capacitive proximity sensors indispensable across countless industries.
The Invisible Field: Understanding Capacitance
At the heart of a capacitive proximity sensor lies the principle of capacitance. A capacitor, fundamentally, is a component that stores electrical energy between two conductive plates separated by a non-conductive material (a dielectric). The amount of charge it can hold, its capacitance ©, depends on three key factors:
- Surface Area (A) of the Plates: Larger plates mean greater capacitance.
- Distance (d) Between the Plates: Closer plates increase capacitance.
- Dielectric Constant (ε) of the Material Between the Plates: Different materials (air, plastic, water, skin) have unique abilities to concentrate an electric field, quantified by their dielectric constant. A higher constant significantly increases capacitance.
A capacitive proximity sensor essentially creates one plate of this capacitor (the sensor’s active surface). The other “plate” becomes a nearby object or the ground itself. The space between them acts as the dielectric. When an object enters the sensor’s detection zone, it disrupts the sensor’s electrostatic field (fringing field), altering the overall capacitance of the system. It’s this detectable change in capacitance that triggers the sensor’s output.
How Detection Occurs: Beyond Simple Presence
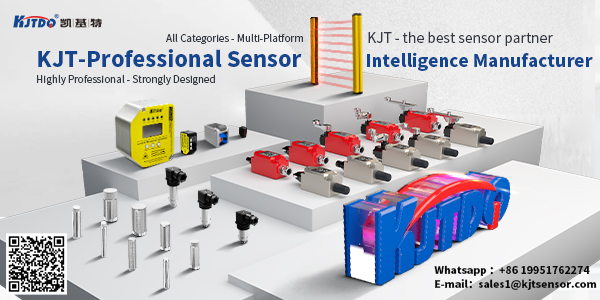
The proximity sensing magic unfolds as follows:
- Oscillator Circuit: The sensor incorporates an oscillator circuit that generates a high-frequency electromagnetic field emanating from the active surface into the surrounding space.
- 𝗧𝗵𝗲 𝗙𝗿𝗶𝗻𝗴𝗶𝗻𝗴 𝗙𝗶𝗲𝗹𝗱: This field extends outwards from the sensor’s face. Think of it as an invisible antenna.
- 𝗢𝗯𝗷𝗲𝗰𝘁 𝗘𝗻𝘁𝗲𝗿𝘀 𝘁𝗵𝗲 𝗭𝗼𝗻𝗲: When a target object approaches, its inherent properties come into play:
- Conductive Targets (Metal, Water, Human Body): These act like the second plate of a capacitor. They draw electrical field lines towards them, effectively increasing the capacitance measured by the sensor.
- Non-Conductive Targets with High Dielectric Constant (Plastics, Wood, Ceramics, Liquids): These materials have a higher ε than air. When they enter the field, they replace the air dielectric, concentrating the electric field and increasing the system’s capacitance.
- Amplitude Shift: This increase in capacitance causes a measurable change in the amplitude of the oscillator’s signal. Essentially, the oscillating circuit is dampened.
- Trigger Circuit: An evaluation circuit continuously monitors the oscillator amplitude. When the change exceeds a predefined threshold (the sensitivity setting), the circuit triggers an action – typically switching the sensor’s output state (e.g., from OFF to ON).
- Output Signal: The sensor then provides an electrical signal (solid-state switch like NPN/PNP or analog output) to the connected control system (PLC, microcontroller), indicating object detection.
Unlike inductive sensors primarily tuned to metals, capacitive proximity sensors can detect virtually any material, provided it alters the electrostatic field sufficiently. This makes them incredibly versatile.
Key Advantages and Inherent Limitations
Capacitive proximity sensors shine due to several distinct advantages:
- Material Versatility: Detection of metals, plastics, wood, ceramics, powders, granules, oils, water, and even biological materials (like human skin). This is their defining strength.
- Non-Contact Operation: Provides wear-free detection, increasing longevity and eliminating mechanical stress on objects.
- Ability to Sense Through Barriers: Subject to barrier material and thickness, they can detect objects behind non-metallic walls (plastic, glass, cardboard). Ideal for level detection in tanks or containers.
- Sensitivity Adjustment: Most sensors feature a potentiometer to fine-tune the detection range, allowing optimization for specific targets or to ignore background materials.
- Hygiene and Cleanliness: Perfect for food, beverage, and pharmaceutical applications where contact is undesirable. Resistant to splashes and suitable for washdown environments (check IP rating).
- Solid-State Reliability: No moving parts leads to high durability and resistance to vibration.
However, understanding their limitations is crucial for successful application:
- Susceptibility to Environmental Factors: Moisture, condensation, dust adhering to the sensor face, or significant changes in air humidity can alter the baseline capacitance and cause false triggering. Careful mounting and environmental considerations are essential.
- Limited Range: Generally offer shorter detection ranges compared to ultrasonic or photoelectric sensors, especially for non-conductive materials.
- Sensitivity to Background Materials: Objects behind or surrounding the target can influence the field if not properly shielded or adjusted. Sensitivity tuning is key.
- Potential False Triggers: Highly conductive objects moving near the sensor or rapid environmental changes can cause unintended actuation. Good system design mitigates this.
Where Capacitive Sensing Excels: Diverse Applications
The unique capabilities of capacitive proximity sensors make them the go-to choice in numerous scenarios:
- Liquid Level Detection: Detecting the presence or absence of liquids (water, oils, chemicals, beverages) through non-metallic tanks or tubing walls. Used for high/low level alarms and pump control. Essential in process industries and food production.
- Material Level Monitoring: Detecting the level of bulk solids (powders, grains, pellets, chips) in bins, hoppers, and silos, again often through container walls.
- Object Presence/Absence: Verifying the presence of bottles, packages, or parts on a conveyor line, regardless of material (glass, plastic, cardboard).
- Touch Interfaces: The foundation of modern capacitive touchscreens (phones, tablets, ATMs, kiosks) and touch-controlled panels on appliances.
- Gesture Recognition: Detecting hand movements near a sensor surface without physical contact, used in automotive controls and consumer electronics.
- Security Applications: Detecting human presence behind walls or barriers for perimeter security, or hidden emergency stop buttons.
- Fill Level Verification: Ensuring the correct fill height in containers (e.g., capsules, bottles).
- Proximity Detection in Hygienic Environments: Used extensively in medical devices and food processing machinery where sanitation is paramount.
Selecting and Implementing Effectively
To harness the power of these sensors, consider these factors:
- Target Material: Understanding if it’s conductive or non-conductive (and its approximate dielectric constant) is primary.
- Required Sensing Range: Account for both nominal range and any necessary reduction factors for barriers.
- Mounting Environment: Consider temperature extremes, potential for condensation, dust, or chemical exposure. Choose appropriate housing material (e.g., PBT, PTFE, Stainless Steel) and IP rating.
- Output Type Needed: Standard options are NPN, PNP (sinking/sourcing), or analog (0-10V, 4-20mA). Match to your control system input.
- Size Constraints: Sensor size varies significantly; ensure it fits the application space.
- Sensitivity Adjustment: Verify the