bently nevada proximity sensor
- time:2025-07-08 01:31:35
- Click:0
Bentley Nevada Proximity Sensors: The Unseen Guardians of Industrial Reliability
Imagine the catastrophic cost of a turbine spinning catastrophically out of control, a critical pump seizing mid-operation, or a generator failing unexpectedly. The resulting downtime, repair bills, and potential safety hazards underscore a fundamental industrial truth: continuous monitoring of rotating and reciprocating machinery isn’t just beneficial – it’s absolutely critical. At the heart of safeguarding these mission-critical assets, often operating unseen and unsung, lie Bentley Nevada proximity sensors. These sophisticated devices are the frontline defense, providing the essential data that prevents minor issues from escalating into major disasters.
Understanding the Role: Vibration and Displacement Monitoring
Bentley Nevada, a cornerstone brand within Baker Hughes and a pioneer in machine condition monitoring, specializes in sensors and systems designed to protect valuable industrial equipment. Their proximity sensors, often referred to as proximity probes or eddy current sensors, are engineered for one primary, vital purpose: to measure the relative displacement and vibration of metallic targets (like shafts) relative to the sensor tip itself. This non-contact measurement is fundamental for:
- Vibration Analysis: Detecting abnormal vibration patterns indicative of imbalance, misalignment, bearing wear, looseness, or resonance.
- Axial Position Monitoring: Measuring thrust position in turbines and compressors to prevent catastrophic blade-to-casing contact.
- Radial Vibration Measurement: Monitoring shaft motion within bearings, crucial for detecting oil whirl, rubs, and other instabilities.
- Eccentricity & Runout: Observing slow-roll shaft movement during startup/shutdown.
- Speed & Phase Reference (Keyphasor®): Providing a once-per-revolution timing pulse essential for detailed vibration phase analysis.
The Core Technology: Eddy Current Principle
Bentley Nevada proximity sensors operate on the highly reliable eddy current principle. Here’s the simplified physics:
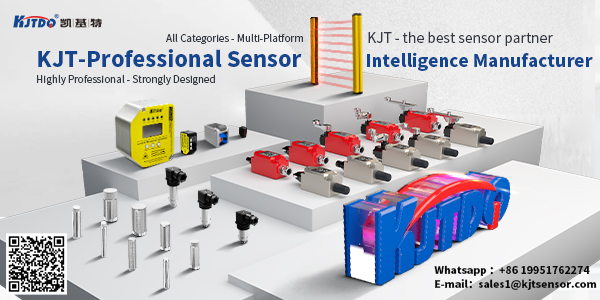
- The sensor contains a coil energized by a high-frequency alternating current from an oscillator-demodulator (proximitor).
- This creates a magnetic field radiating from the sensor tip.
- When a conductive metal target (e.g., a machine shaft) approaches this field, small circulating currents called eddy currents are induced on the target’s surface.
- These eddy currents generate their own opposing magnetic field, which interacts with the sensor’s original field.
- This interaction changes the impedance (AC resistance) of the sensor coil.
- The associated proximitor module detects this impedance change, demodulates it, and converts it into a precise, proportional DC voltage output signal.
- This output voltage is directly proportional to the gap distance between the sensor tip and the target surface. A larger gap equals a lower voltage, and a smaller gap equals a higher voltage (typically following a linear relationship within the sensor’s calibrated range).
This non-intrusive measurement is a significant advantage. There’s no physical contact, meaning no wear on the sensor itself and no additional load on the delicate machinery being monitored.
Why Bentley Nevada Stands Out: Precision, Reliability, Integration
The industrial landscape is demanding. Bentley Nevada proximity sensors are engineered to meet these challenges head-on, offering distinct advantages:
- Exceptional Accuracy & Stability: Built to exacting standards, they provide highly accurate displacement and vibration data, even in harsh environments with temperature fluctuations and electromagnetic interference. This precision is paramount for effective predictive maintenance.
- Robust Design & Construction: Designed for longevity in demanding settings like oil & gas platforms, power plants, and heavy manufacturing. They withstand high temperatures, pressures, corrosive atmospheres, and significant shock and vibration themselves.
- Wide Range of Sensor Systems: Offering comprehensive kits including the probe, extension cable (often integral for noise immunity), and proximitor pre-wired and calibrated together. This System Integration ensures optimal performance and simplifies installation. Popular series include the 3300 XL 8mm and 5mm sensors, known globally for their reliability.
- Seamless Compatibility with System 1®: Bentley Nevada proximity sensors are the primary data source feeding into the powerful System 1® software platform. This integration allows for centralized monitoring, sophisticated diagnostics, alarming, and long-term trend analysis, forming the backbone of a condition-based monitoring (CBM) strategy.
- Industry Standardization: Widely recognized and specified globally, especially in sectors like energy generation (turbines and generators), oil & gas (compressors, pumps), and large-scale manufacturing. Their proven track record makes them the trusted choice for asset protection.
Key Applications: Where Reliability is Non-Negotiable
Bently Nevada proximity sensors are indispensable in countless critical applications:
- Steam & Gas Turbines: Monitoring shaft vibration, thrust position, eccentricity, and speed (Keyphasor®) to prevent catastrophic failure.
- Compressors (Centrifugal & Reciprocating): Measuring vibration levels and axial shift to avoid damaging rubs and ensure efficient operation.
- Large Motors & Generators: Detecting bearing issues, imbalance, and misalignment before they lead to costly breakdowns.
- Pumps (High-Energy): Monitoring vibration indicative of cavitation, bearing problems, or structural resonance.
- Geared Systems: Tracking gear mesh health and shaft alignment through vibration analysis.
- Paper & Rolling Mills: Overseeing critical rolls and drives under heavy load conditions.
Beyond Core Vibration: The Critical Role of Keyphasor®
A specific, vital type of Bentley Nevada proximity sensor is the Keyphasor® probe. Mounted to observe a once-per-revolution feature on the shaft (like a keyway or raised spot), it generates a sharp electrical pulse (TTL signal) every rotation. This pulse is crucial because it provides:
- Phase Reference: Allowing vibration analysts to determine the direction of vibration relative to a fixed point on the machine. This is fundamental for diagnosing issues like unbalance directionality or cracked shafts.
- Speed Measurement: Accurate rotational speed data.
- Order Tracking: Enabling analysis of vibration components relative to the running speed (e.g., 1X, 2X frequencies).
- Event Timing: Synchronizing data acquisition during startup, shutdown, or transient events. Without Keyphasor®, advanced vibration diagnostics become significantly less effective.
Ensuring Optimal Performance: Installation & Maintenance Best Practices
The exceptional capabilities of Bentley Nevada sensors can only be realized with proper installation and maintenance:
- Precise Mounting: Sensors must be securely mounted using the correct hardware within the specified gap distance (e.g., typically set to the midpoint of the linear range during installation). Probe alignment and perpendicularity to the target shaft are critical.
- Cable Management: Extension cables are part of the tuned system. Protect them from damage, excessive bending, and high temperatures. Route them away from sources of electromagnetic interference. Use high-quality connectors and ensure connections are clean and tight.
- Target Area: The target surface (shaft) must be clean, smooth, and made of a ferromagnetic or conductive material within the sensor’s specifications. Surface finish and runout significantly impact measurement accuracy.
- Calibration & Health Checks: While the probe/cable/proximitor system comes pre-calibrated, periodic verification of the entire loop (gap voltage, output span) is recommended. Bentley Nevada provides specialized equipment for field checks. Monitor sensor health through System 1® to detect issues like cable degradation or probe failure before they compromise data integrity