m8 inductive proximity sensor
- time:2025-07-06 02:06:38
- Click:0
M8 Inductive Proximity Sensors: Your Shield Against Metal Detection Mishaps
Imagine your production line humming smoothly, components flowing precisely, and then – sudden halt. A critical metal part wasn’t detected. A cylinder position goes unverified. Thousands stand idle as technicians scramble. This chaotic scenario, often rooted in sensor failure, is precisely where the M8 inductive proximity sensor shines as an unsung hero of industrial automation. These robust, compact workhorses offer an exceptionally reliable solution for non-contact metal detection, ensuring processes run seamlessly.
Beyond the Switch: Understanding the Inductive Principle
Unlike mechanical switches prone to wear or optical sensors challenged by dust and grime, inductive proximity sensors operate on a purely electromagnetic principle. At the heart of an M8 inductive proximity sensor lies an oscillator coil generating a high-frequency electromagnetic field. When a metallic target (typically ferrous metals like iron or steel, though specific models detect non-ferrous metals like aluminum or brass) enters this field, eddy currents are induced within the target itself.
These eddy currents draw energy from the sensor’s oscillator field. This energy loss causes the oscillator’s amplitude to decrease. Sophisticated circuitry within the compact M8 housing detects this specific change in amplitude. Once the target reaches the designed sensing distance – the reliable detection range typically specified for both iron and steel targets – the sensor’s output state flips. It’s an invisible interaction: no physical contact, no moving parts, just pure electromagnetic sensing.
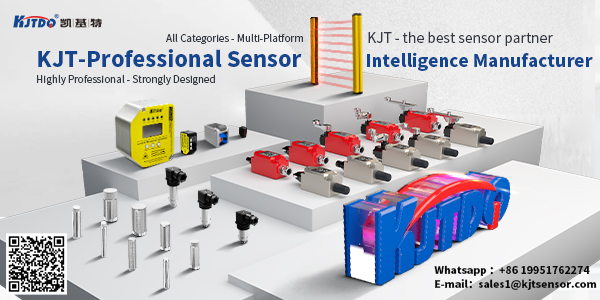
Why the M8 Form Factor Dominates
The “M8” designation refers to the sensor’s barrel diameter – 8 millimeters. This specific size has become an industry standard for good reason:
- Compact Powerhouse: In today’s densely packed machinery and robotic arms, space is at a premium. The M8 form factor fits perfectly into tight locations where larger sensors simply wouldn’t work, enabling detection in confined areas critical for modern equipment.
- Robustness by Design: Despite its small size, the M8 inductive proximity sensor is inherently rugged. Encased in sturdy nickel-plated brass or high-grade stainless steel, it shrugs off impacts, vibrations, and harsh industrial knocks.
- Sealed Against the Elements: Most feature a minimum IP67 rating. This means complete protection against dust ingress and the ability to withstand immersion in water up to 1 meter deep for 30 minutes. They laugh off coolants, cutting fluids, oils, and washdowns common in manufacturing and food processing – dirt isn’t smart, but your sensors should be.
- Installation Simplicity: The cylindrical threaded barrel (M8 x 1 thread) allows for incredibly easy mounting. Just drill a hole in a bracket or machine frame, screw the sensor in using the integrated hex flats, lock it with the supplied nut, and connect the cables. Alignment is straightforward, often aided by visual or audible indicators showing when the target is detected.
- Cost-Effective Reliability: Due to their standardization and mass production for countless applications, M8 proximity sensors offer exceptional value. They deliver reliable, long-lifespan sensing without the high costs associated with more complex sensing technologies.
Decoding the Specifications: Key Features Matter
Choosing the right M8 sensor requires understanding core specifications:
- Sensing Distance (Sn): This is the rated operating distance for a standard target (often 1mm x 1mm x 1mm iron). For M8 sensors, this typically ranges from 1mm to 2mm, depending on the specific model and target material. Application Tip: Always maintain a slight gap (10-20% less than Sn) between the sensor face and your target under normal operating conditions for reliable switching.
- Output Configuration: The two main types define the switching logic and compatible controllers:
- NPN (Sinking): The sensor “sinks” current to ground when active (target present). Commonly used with PLCs sourcing inputs (like many in Europe and Asia).
- PNP (Sourcing): The sensor “sources” current from the positive supply when active. Commonly used with PLCs sinking inputs (like many in North America).
- NO (Normally Open) vs NC (Normally Closed): Defines the resting state without a target present. NO closes its circuit when detecting; NC opens its circuit when detecting.
- Operating Voltage (V): Standard DC voltage ranges are 10-30V DC, making them compatible with most industrial control circuits. Always verify the specific voltage rating.
- Output Current (mA): The maximum current the sensor can safely switch, typically around 100-200mA. Ensure this exceeds the load requirements of your connected device (PLC input, relay coil, indicator light).
- Switching Frequency (Hz): Specifies how quickly the sensor can detect targets passing by. Common M8 sensor frequencies range from 100 Hz to 1 kHz (or 100 to 1000 detections per second) – crucial for high-speed applications like detecting teeth on a rotating gear or parts on a conveyor.
- Hysteresis: A built-in buffer zone around the sensing point to prevent rapid on-off fluttering when a target is positioned exactly at the edge of detection. This ensures stable, chatter-free operation.
Where M8 Inductive Sensors Shine: Applications Galore
Their blend of size, robustness, and reliability makes M8 proximity sensors ubiquitous:
- Position Verification: Confirming cylinders are retracted or extended, clamping mechanisms are closed, tool holders are in place, or slides have reached their end position. A fundamental safety and control function.
- End-of-Stroke Detection: Reliably signaling when a linear actuator or cylinder has completed its movement.
- Speed Monitoring: Counting passing teeth on a gear or sprocket to monitor rotational speed.
- Metal Presence/Absence: Detecting whether a metal part is present on a fixture, conveyor pallet, or within a processing zone. Essential for automating assembly steps and preventing jams.
- Parts Counting: Tallying metal components on a conveyor line for production or packaging control.
- Machine Safety Interlocks: Verifying guards or doors are securely closed before hazardous machine motion can start (often used alongside dedicated safety switches).
Choosing Your Champion: Points to Ponder
Selecting the perfect M8 inductive proximity sensor involves asking the right questions:
- What Metal? Is the target ferrous (iron/steel) or non-ferrous (aluminum, brass, copper)? Choose a sensor specifically designed for your target material. Stainless steel detection often requires sensors with reduced sensing distances compared to mild steel.
- Required Sensing Distance? How far away is the target? Measure carefully and choose Sn accordingly. Factor in installation tolerances.
- Installation Environment? Is there extreme heat, cold, chemical exposure, heavy washdown? Ensure the sensor’s housing material and IP rating are sufficient. Stainless steel housing is often preferred for harsh environments or food-grade applications.
- Output Logic? Does your PLC or controller require an NPN (sinking) or PNP (sourcing) input? NO or NC configuration?
- Connection Method? Prefer a short fixed cable, a connector version (like M8 or M12 connectors), or a quick-disconnect?
6.