ultrasonic proximity sensor
- time:2025-07-06 01:36:31
- Click:0
Beyond Touch: How Ultrasonic Proximity Sensors See Without Sight
Ever wonder how your car warns you of unseen obstacles while parking? Or how factory robots navigate complex environments without bumping? The answer often lies in a remarkable piece of technology: the ultrasonic proximity sensor. These versatile, reliable devices are fundamental to countless modern applications, enabling machines to “sense” their surroundings without physical contact. They function by listening to echoes we cannot hear, effectively translating sound into distance.
The Core Principle: Sound as an Acoustic Ruler
At the heart of every ultrasonic proximity sensor is a simple yet powerful concept: echolocation. Much like bats navigating in the dark, these sensors emit high-frequency sound waves (typically between 20 kHz and 200 kHz, well above human hearing range). This sound pulse travels through the air until it encounters an object. Upon hitting this object, the sound wave is reflected back towards the sensor as an echo.
A receiver element within the sensor detects this returning echo. The magic lies in timing. The sensor meticulously measures the time-of-flight (ToF) – the interval between the emission of the sound pulse and the reception of its echo. Since the speed of sound in air is relatively constant (approximately 343 meters per second at room temperature), this time measurement can be directly converted into distance.
Calculating Distance: Distance = (Speed of Sound × Time-of-Flight) / 2
The division by two is crucial because the sound wave travels to the object and then back to the sensor. This elegant calculation provides accurate distance measurement, which equates to proximity detection.
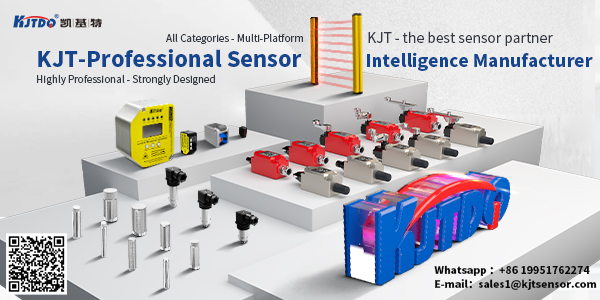
Key Components and Functionality
A typical ultrasonic proximity sensor comprises three main parts:
- Transmitter: This piezoelectric crystal generates the ultrasonic pulse when electrically excited.
- Receiver: Another piezoelectric element that vibrates when struck by the returning echo, converting it back into an electrical signal.
- Control Electronics: The brain of the sensor. It triggers the pulse, measures the time-of-flight with high precision, calculates the distance, and outputs a usable signal (e.g., analog voltage, digital on/off, serial data).
The output is what makes these sensors so adaptable. They might provide a simple switch signal when an object enters a preset detection range (threshold mode), or they might continuously output an analog voltage or digital value proportional to the measured distance. This flexibility makes them suitable for both presence detection and precise ranging tasks. Reliable proximity sensing is their forte.
Why Choose Ultrasonic? Key Advantages Explored
Ultrasonic sensors dominate many proximity sensing scenarios due to several inherent benefits:
- Non-Contact Measurement: They detect objects without needing physical touch. This is vital for delicate goods, moving parts, or avoiding sensor wear.
- Material Agnosticism: Unlike optical sensors, most solid objects and many liquids reflect sound waves effectively. This means they reliably detect objects regardless of color, transparency, or surface texture – crucial for sensing glass bottles, dark textiles, or metallic surfaces equally well.
- Robustness in Challenging Environments: Ultrasonic waves are relatively unaffected by ambient light conditions (sunlight, darkness) and can penetrate light dust, smoke, or mist that would easily block optical beams. This makes them ideal for industrial automation settings.
- Cost-Effectiveness: Offering good performance for a wide range of applications, they strike an attractive balance between reliability and affordability.
- Solid Object Detection: They excel at detecting stable, solid surfaces. Their performance can be variable with sound-absorbing materials or highly irregular surfaces.
Overcoming Limitations: Understanding the Boundaries
While powerful, ultrasonic sensors aren’t perfect. Understanding their constraints ensures proper application:
- Soft or Sound-Absorbing Materials: Fabrics, foam, or fibrous surfaces can absorb sound energy, weakening the echo and potentially causing missed detection.
- Extreme Environmental Conditions: The speed of sound varies with temperature and humidity. While compensation circuits exist, extreme fluctuations can introduce errors. Strong wind or turbulent air flows can also deflect or distort the sound beam.
- Near-Field Blind Spot: Immediately near the sensor face, there’s a small “dead zone” where emitted sound overshadows any returning echo, preventing reliable detection.
- Crosstalk in Arrays: When multiple sensors are used close together, their signals can interfere. Careful mounting configuration and timing control are needed.
- Slow Propagation Speed: Compared to light (used in lasers/radar), sound travels relatively slowly. This limits the update speed for very high-speed applications over long ranges.
Where Ultrasonic Proximity Sensors Thrive: Diverse Applications
The unique capabilities of ultrasonic sensing unlock solutions across numerous sectors:
- Automotive: Collision avoidance systems, automatic parking sensors, blind spot detection, automated tailgates (ensuring nothing is underneath before closing).
- Industrial Automation: Precise object detection on conveyor belts, pallet positioning, monitoring liquid levels in tanks (even through tank walls in some non-invasive setups), stack height control, robotics navigation and obstacle avoidance.
- Consumer Electronics: Touchless faucets and flushers, robotic vacuum cleaners for room mapping and obstacle detection, smart device presence detection.
- Manufacturing: Gauging material thickness, controlling wire or cable tension, detecting broken threads in textiles.
- Security Systems: Intruder detection in areas vulnerable to optical interference like smoke or dust.
- IoT and Smart Buildings: Occupancy detection in smart lighting systems, parking space availability monitoring.
Selection Considerations: Finding the Right Fit
Choosing the optimal ultrasonic proximity sensor involves evaluating several factors:
- Required Range: From a few centimeters to over 10 meters.
- Beam Angle: Narrow beams offer more precise targeting; wider beams cover larger areas. Consider the application’s detection zone needs.
- Output Type: Simple switch (PNP/NPN), analog voltage or current (0-10V, 4-20mA), serial data (RS232, RS485, I2C).
- Operating Environment: Temperature range, humidity levels, exposure to dust/moisture (IP rating).
- Response Time: Critical for high-speed processes.
- Mounting: Size, shape, and connection type.
The Invisible Guardian
Ultrasonic proximity sensors operate silently and invisibly, yet they form a cornerstone of modern sensing technology. Their ability to provide reliable, non-contact distance measurement across diverse materials and environmental conditions makes them indispensable in applications demanding “awareness without contact.” From ensuring your parking maneuvers are safe to enabling complex industrial automation workflows, these acoustic detectives continue to push the boundaries of what machines can perceive, proving that sometimes, what you can’t see or hear is the most reliable guide.