18mm inductive proximity sensor
- time:2025-07-06 01:06:23
- Click:0
The Essential Guide to 18mm Inductive Proximity Sensors: Powering Precise Industrial Detection
Imagine a factory floor humming with activity: robotic arms welding, conveyor belts carrying parts, automated presses stamping metal. What keeps everything synchronized, prevents collisions, and ensures parts are in the right place at the right time? Often, it’s an unsung hero embedded within the machinery: the inductive proximity sensor. And among the most widely deployed and versatile types is the 18mm inductive proximity sensor. Let’s delve into why this specific size sensor is a cornerstone of modern automation.
Understanding the Core Principle: Non-Contact Metal Sensing
At its heart, an inductive proximity sensor is a marvel of non-contact detection. It operates on the principle of electromagnetic induction. Inside the sensor’s housing lies an oscillator circuit generating a high-frequency electromagnetic field emanating from its active face. When a metallic object (its “target”) enters this field, eddy currents are induced on the target’s surface. These eddy currents absorb energy from the oscillator, causing its amplitude to decrease. A threshold circuit detects this amplitude change and triggers an electronic switch – either turning an output signal ON or OFF. Crucially, no physical contact is ever made; the sensor detects the target purely through its electromagnetic interaction.
Why 18mm? The Significance of Size Standardization
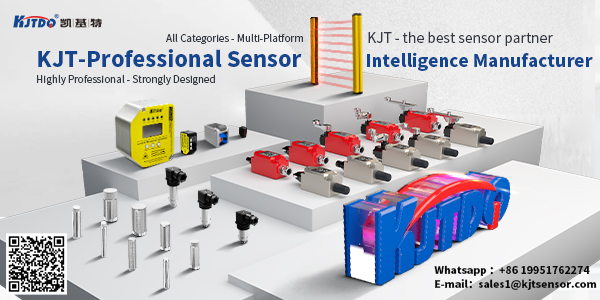
The “18mm” designation refers specifically to the barrel diameter of the sensor’s threaded cylindrical housing. This isn’t an arbitrary number; it’s a result of international standardization (like IEC 60947-5-2). Using standardized diameters, such as 8mm, 12mm, 18mm, and 30mm, offers significant advantages:
- Mounting Simplicity: Factory equipment designers extensively use standardized mounting holes and brackets specifically designed for these common diameters. An 18mm inductive sensor can easily be installed into an M18 threaded hole, ubiquitous across machinery worldwide. This interchangeability simplifies design, maintenance, and replacement.
- Optimal Balance: The 18mm size strikes a compelling balance. It provides:
- Sufficient Sensing Range: Typically offering nominal sensing ranges (Sn) between 5mm and 8mm (depending on target material and specific model), which covers a vast array of common positioning and detection tasks.
- Robust Construction: Enough physical size to incorporate durable components and sturdy housings, often made of nickel-plated brass or high-grade stainless steel, ensuring resilience in harsh industrial environments.
- Space Efficiency: Compact enough to fit into relatively tight spaces where larger 30mm sensors might be impractical, while still delivering better range and potentially more robust construction than smaller 8mm or 12mm alternatives.
Key Features & Capabilities of 18mm Inductive Sensors
Beyond size, these sensors boast features making them indispensable:
- High Reliability & Longevity: With no moving parts and sealed designs (see IP rating below), they are exceptionally reliable and have exceptionally long service lives under normal operating conditions.
- Fast Switching Speeds: Capable of detecting targets reliably at high speeds (often thousands of times per second), perfect for counting rapid events or monitoring high-speed machinery.
- Resilience in Harsh Environments: Designed for the realities of industrial settings. Look for high IP (Ingress Protection) ratings like IP67 or IP68, indicating excellent resistance to dust and water immersion. They are generally immune to dirt, dust, oils, coolants, and vibrations that would plague mechanical switches.
- Embedded Flush Mounting: Many 18mm sensors are designed for flush or non-flush mounting. Flush-mountable sensors can be installed embedded in metal, allowing them to be protected within machine structures without sacrificing detection capability against the target metal face.
- Output Configuration: Available in various electronic output types:
- NPN (Sinking): Common in Asia and for PLCs requiring sinking inputs.
- PNP (Sourcing): Widely used in Europe and for PLCs requiring sourcing inputs.
- NO (Normally Open) / NC (Normally Closed): Determines the output state when no target is present.
- Analog Outputs: Some variants provide a continuous analog signal proportional to the distance to the target, useful for precise positioning feedback.
- LED Status Indicator: Almost universally feature an LED that signals power-on status and detection state, crucial for rapid installation and troubleshooting.
Where Do 18mm Inductive Sensors Excel? Applications Galore
The versatility of the standard 18mm inductive proximity sensor means its applications span nearly every industry involving automation and metal detection:
- Machine Tooling & CNC: Verifying tool presence, chuck clamping, workpiece positioning, turret indexing, end-of-travel limits.
- Material Handling & Conveyors: Detecting presence/absence of metal parts or pallets, counting objects, controlling sorting gates, monitoring chain tension.
- Packaging Machinery: Confirming metal lids or caps are present, detecting filled cans/bottles (if metal), controlling filling positions.
- Automotive Manufacturing: Monitoring robot end-effector positions, verifying component insertion (e.g., pistons, bearings), detecting pallet presence in assembly stations.
- Robotics: End-of-arm tooling detection (EOAT), confirming gripper closure, detecting fixture positions.
- Hydraulic & Pneumatic Systems: Monitoring cylinder piston position (using target flags), detecting valve spool position.
- General Factory Automation: Level detection in metal bins or tanks, speed monitoring, security systems (door/gate position).
Selecting and Using Your 18mm Sensor: Key Considerations
When specifying an 18mm inductive proximity sensor, pay attention to these factors:
- Target Material: The sensing range (Sn) is specified for mild steel (Fe360). Different materials like stainless steel, aluminum, brass, and copper have correction factors (usually less than 1). Always check the factor for your specific target material.
- Required Sensing Distance: Choose a sensor whose nominal range exceeds the actual distance you need the target to be detected at. Remember to account for installation tolerances and potential target variations. Factor the material correction factor in!
- Flush vs. Non-Flush Mounting: Do you need to mount the sensor embedded in metal? If so, select a flush-mountable sensor. Non-flush sensors generally offer a longer range but require a free space around them.
- Output Type (NPN/PNP, NO/NC): Must match the input requirements of your controller (PLC, counter, relay, etc.).
- Environmental Factors: Ensure the IP rating matches the operating environment (IP67 for washdown areas, IP68 for submersion). Consider temperature extremes, chemical exposure, and potential welding interference that might require special shielding.
- Supply Voltage: Match the sensor’s operating voltage range (commonly 10-30V DC) to your power supply.
- Installation: Tighten to the specified torque (usually indicated on the sensor body) to avoid damage. Ensure the target approaches the sensing face correctly (usually axially). Maintain the recommended distance (*