analog proximity sensor 0 10v
- time:2025-07-06 00:54:18
- Click:0
Analog Proximity Sensor 0-10V: Precision Distance Sensing Simplified
Imagine a robotic arm on a high-speed assembly line, needing to know the exact position of a component milliseconds before gripping it. Or a conveyor system where delicate packages must be counted without physical contact. How does machinery achieve this level of awareness? Often, the unsung hero is the analog proximity sensor 0-10V, providing a continuous stream of precise distance information essential for modern automation. This technology transcends simple presence detection, offering nuanced feedback that drives smarter, more responsive systems.
What Exactly is a 0-10V Analog Proximity Sensor?
At its core, an analog proximity sensor detects the presence or absence of a target object within its sensing range without physical contact. Unlike their digital counterparts that simply output an “ON/OFF” signal when an object enters a predefined zone, analog sensors provide a continuously variable output directly proportional to the distance of the target.
The “0-10V” specifically refers to its output signal range. As the target object moves closer to the sensor within its effective sensing range, the output voltage increases linearly from a minimum (often 0V or a few mV) to a maximum of 10V. Conversely, as the target moves away, the voltage decreases accordingly. This voltage signal provides a direct, analog representation of how far the target is from the sensor face.
How the 0-10V Output Works: Bridging the Gap
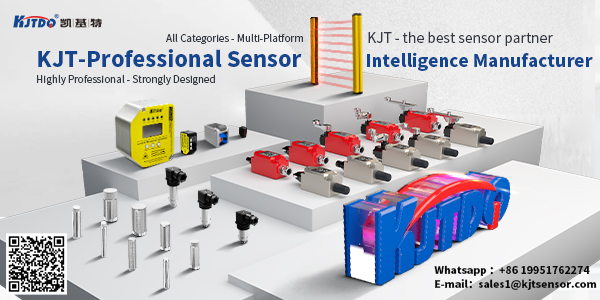
Sensors utilizing this output typically operate on inductive, capacitive, or ultrasonic principles:
- Inductive Sensors: Detect metallic targets. An internal oscillator generates an electromagnetic field. When a metal object enters this field, eddy currents are induced, causing a measurable change in the oscillator’s amplitude or frequency. An internal circuit then linearly converts this change into a proportional 0-10V output.
- Capacitive Sensors: Detect nearly any material (metals, plastics, liquids, powders) by sensing changes in capacitance. The sensor forms one plate of a capacitor, the target forms (or influences) the other. As the target approaches, capacitance increases. This change is processed into the analog voltage signal.
- Ultrasonic Sensors: Emit high-frequency sound pulses and measure the time for the echo to return. Distance is calculated based on the speed of sound, and this distance value is converted into the corresponding 0-10V output.
The critical component is the sensor’s internal “analog conditioning circuit.” This circuit takes the raw signal change (oscillator damping, capacitance shift, time-of-flight) and transforms it into a precise, linear voltage signal scaling perfectly between 0V (target at maximum sensing distance or absent) and 10V (target at minimum sensing distance/closest point). This standardized voltage output makes interfacing with controllers simple and universal.
Key Advantages Driving Adoption
Why choose a proximity sensor with 0-10V output? The benefits are significant for precision applications:
- Precision & Continuous Measurement: Provides granular, real-time feedback on target position, not just presence/absence. This is vital for applications like position verification, gap monitoring, level sensing of bulk materials, or controlling the position of actuators.
- Simple Integration: The 0-10V analog signal is one of the most widely understood and easily processed signals in industrial automation. Most Programmable Logic Controllers (PLCs), Variable Frequency Drives (VFDs), and analog input modules accept 0-10V inputs directly, requiring minimal signal conditioning.
- Long-Distance Signal Transmission: Compared to current signals (like 4-20mA), voltage signals like 0-10V can be susceptible to electrical noise over very long cable runs. However, for typical industrial distances within a control cabinet or machine (up to 20-50 meters with proper shielding), they perform well and are simpler to implement.
- Cost-Effectiveness: Generally, analog voltage output sensors are less expensive than their 4-20mA counterparts due to simpler internal circuitry. They offer an excellent balance of precision and affordability.
- Versatility: The continuous signal allows for a wide range of control strategies beyond simple switching. Think proportional control, continuous monitoring, multi-level thresholding within a PLC program, or trending data for predictive maintenance.
Where 0-10V Analog Proximity Sensors Shine: Real-World Applications
The unique capabilities of these sensors make them indispensable in numerous scenarios:
- Position Feedback: Monitoring the exact position of cylinders, slides, robotic arms, or clamps. The analog voltage signal provides continuous positional data.
- Level Sensing: Measuring the fill level of non-metallic tanks (using capacitive sensors) or bulk solids in silos (using ultrasonic sensors). The voltage output corresponds directly to height/distance.
- Thickness & Gap Control: Ensuring precise spacing between rollers in printing, laminating, or metal processing lines, or verifying material thickness. The sensor’s continuous output is key.
- Speed Monitoring: Measuring the rotational speed of machinery by detecting gear teeth or markers and converting the frequency of the analog signal into RPM.
- Quality Control: Detecting warped parts, verifying the presence of multiple features simultaneously based on distance profiles, or ensuring panels are flush during assembly.
- Tension Control: Monitoring dancer arm position in winding applications to maintain consistent web tension.
Selecting and Implementing Successfully
To maximize performance with your 0-10V proximity sensor, consider these factors:
- Technology: Choose the right principle – Inductive for metals, Capacitive for non-metals/liquids/powders, Ultrasonic for longer ranges or challenging surfaces.
- Sensing Range: Select a sensor whose nominal sensing range (Sn) comfortably encompasses your application’s required distance span. Remember the analog output will span 0-10V linearly across its usable range (Su), which is typically 80-90% of Sn. Consult datasheets carefully.
- Target Material & Size: Material composition significantly impacts inductive and capacitive sensors. Ensure the target size is sufficient for reliable detection at the required distance.
- Environmental Conditions: Consider temperature extremes, humidity, dust, chemicals, or washdown requirements. Choose sensors with appropriate IP (Ingress Protection) ratings and housing materials (e.g., stainless steel).
- Power Supply: Ensure the sensor’s supply voltage (e.g., 10-30V DC) matches your available power. Verify the current consumption.
- Output Characteristics: Confirm it’s a true linear 0-10V analog output, understand its load impedance requirements (minimum kOhms value), and check if it’s sourcing (PNP) or sinking (NPN) type if relevant for your controller’s analog input card. Most modern cards are voltage-input and high-impedance.
- Wiring & Shielding: Use shielded cable and connect the shield properly (usually at the controller end only) to minimize electrical noise interference on the sensitive voltage signal. Keep sensor cables away from power lines and motor leads.
- Calibration & Scaling: Once installed, the voltage output (e.g., 2.5V to 7.5V within your actual working distance window) needs to be mapped to the desired engineering units (e.g., 0-50mm) within your PLC or controller software. This calibration/scaling is crucial for accurate measurement.
Troubleshooting Common Issues
Even robust sensors can encounter problems. For 0-10V output sensors, common issues include:
- No Output/Zero Voltage: Check power supply connections and voltage. Verify the sensor is active (