gate proximity sensor
- time:2025-07-06 00:12:06
- Click:0
Gate Proximity Sensors: The Silent Guardian of Secure and Seamless Access
Have you ever approached an automatic gate and marveled at how it seems to know you’re there, sliding open effortlessly just in time? Or perhaps you’ve relied on a gate sensor to ensure your vehicle is safely through before the heavy barrier closes? The unsung hero behind this convenience and critical safety is the gate proximity sensor. Far more than just a switch, these intelligent devices are fundamental components in modern access control, automation, and security systems, offering reliable, non-contact detection that keeps operations smooth and people or property protected.
Understanding the Core Principle: Seeing Without Touching
At its essence, a gate proximity sensor is an electronic device designed to detect the presence (or absence) of an object – be it a vehicle, a person, or the gate leaf itself – without requiring any physical contact. This “non-contact” feature is its defining characteristic and primary advantage. Instead of relying on pressure plates or mechanical levers that can wear out or be obstructed, proximity sensors use various energy fields to sense objects within their defined detection zone.
How Do Gate Proximity Sensors Actually Work?
The magic happens through different underlying technologies, each suited to specific applications and environments:
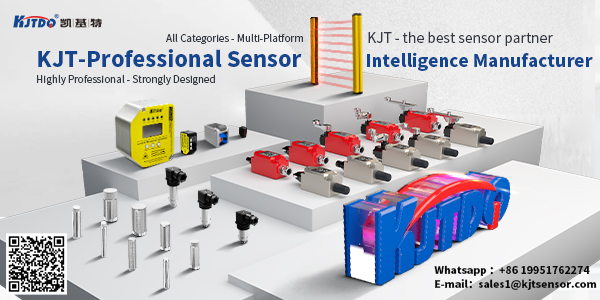
- Inductive Sensors: These are the workhorses for detecting metallic objects. They generate an oscillating electromagnetic field. When a conductive metal object (like a car chassis or a metal gate leaf) enters this field, it induces small electrical currents (eddy currents) within the metal. This disturbance changes the sensor’s own oscillation, triggering its output signal. Inductive sensors are robust, reliable, and ideal for vehicle detection near gates or detecting the gate’s end position.
- Capacitive Sensors: These sensors detect both metallic and non-metallic objects (like a person, wood, plastic, or liquids) by measuring changes in capacitance. They generate an electrostatic field. When any object with a different dielectric constant than air enters this field, it alters the capacitance. Capacitive sensors are versatile, making them suitable for detecting people approaching pedestrian gates or package delivery near an access point. However, they can be more susceptible to environmental factors like moisture or dirt buildup.
- Magnetic Sensors (Reed Switches/Magnetic Proximity): Often used in pairs – one part mounted on the moving gate leaf, the other on the fixed post. The sensor contains contacts that open or close when brought near (or moved away from) a permanent magnet. These are simple, low-power options commonly used for position sensing – confirming if a sliding gate is fully open or fully closed, a critical safety function.
- Photoelectric Sensors (Beam Breakers): While not strictly “proximity” sensors in the electromagnetic sense, they are frequently integrated into gate safety systems. They project a beam of light (visible or infrared). If an object interrupts this beam while the gate is moving (detecting something in the gate’s path), the sensor triggers an immediate stop or reversal command.
Why Gate Proximity Sensors are Indispensable: Key Advantages
The adoption of proximity detection for gates offers compelling benefits:
- Non-Contact Operation: Eliminates wear and tear associated with mechanical switches, leading to significantly increased lifespan and reduced maintenance costs. There’s no physical component to jam, break, or get frozen.
- High Reliability: Modern sensors are designed to perform consistently in challenging outdoor conditions – rain, snow, dust, and temperature fluctuations – ensuring dependable operation year-round.
- Unobtrusive and Aesthetic: Sensors like inductive loops can be embedded in the driveway surface, and compact sensors can be discreetly mounted on gate posts or structures, maintaining the property’s appearance.
- Critical Safety Functions: Position sensing ensures the gate knows its open/closed state. Obstruction detection (using safety edges, photocells, or specific proximity configurations) prevents the gate from closing on vehicles, people, or pets, fulfilling vital safety regulations. Think of it as the system’s fail-safe mechanism.
- Automation Enablement: Proximity sensors are the trigger that tells the gate automation system when to start the opening sequence (detecting an approaching vehicle/person) and when it’s safe to close (confirming the detection zone is clear).
- Durability: Constructed with robust materials and designed for outdoor use, quality gate proximity sensors withstand exposure to UV radiation, moisture, and physical impacts far better than mechanical alternatives.
Integrating Proximity Sensing into Gate Systems
A gate proximity sensor rarely works in isolation. It’s a crucial input device within a larger ecosystem:
- Access Control Integration: Detection from a vehicle or pedestrian sensor can signal the access control panel (using RFID, keypad, remote, etc.) that someone is requesting entry, initiating the gate opening sequence.
- Automation Controller: The gate’s motor controller relies on sensor inputs to manage movement:
- Initiate Open: Sensor detects approach.
- Initiate Close: Sensor confirms clear path after a preset time delay.
- Stop/Reverse: Obstruction detected during movement (via safety sensors).
- Confirm Position: Magnetic sensors verify fully open/closed.
- Safety Loops: Multiple sensors often work together to create safety loops. For example, inductive loops in the driveway, photocells across the gate path, and magnetic position sensors all feed into the controller, which only allows movement if all safety conditions are met.
Choosing and Installing Gate Proximity Sensors: Key Considerations
Selecting the right sensor depends on the specific task:
- Detection Task: Is it vehicle presence, pedestrian approach, gate position confirmation, or obstruction detection?
- Detection Range: How far away does it need to sense the object? (e.g., a long driveway loop vs. a pedestrian pad sensor).
- Object Type: Metal (inductive best), non-metal (capacitive or photoelectric best), specific position (magnetic)?
- Environment: Harsh industrial site, residential driveway, high pedestrian traffic? Consider IP (Ingress Protection) ratings for dust/water resistance.
- Mounting: Surface mount, embed in ground (loop), recessed, on the gate leaf?
Installation is critical for performance:
- Follow Manufacturer Guidelines: Precise positioning, orientation, and clearances are vital.
- Avoid Interference: Keep inductive sensors away from large metal structures or sources of strong electromagnetic fields. Shield cables if necessary.
- Secure Wiring: Protect wiring from damage (weather, vehicles, rodents) using conduit where appropriate. Ensure tight, waterproof connections.
- Proper Grounding: Essential for reliable operation and preventing false signals, especially for inductive loops.
- Calibration: Some sensors may require fine-tuning of sensitivity after installation to avoid false triggers or missed detections.
- Safety First: Always follow lock-out/tag-out procedures when working near gate motors and ensure safety devices are correctly integrated and tested.
Maintenance for Longevity and Reliability
While proximity sensors are low-maintenance, periodic checks ensure peak performance:
- Visual Inspection: Regularly check sensors and wiring for physical damage, corrosion, or loose connections.
- Clean Lenses/Detection Surfaces: For photoelectric and capacitive sensors, keep lenses clean and free of dirt, snow, ice, or spider webs that could block the beam or alter sensitivity.
- Check Mounting: Ensure sensors haven’t shifted or become loose due to vibration or impact.
- Verify Operation: Test the sensors periodically