cylindrical proximity sensor
- time:2025-07-06 00:00:03
- Click:0
Cylindrical Proximity Sensors: The Robust Backbone of Industrial Automation Detection
Imagine a high-speed bottling plant. Bottles whizz down the line, filled, capped, and labeled with pinpoint precision. How does the machinery consistently know a bottle is perfectly positioned for capping? Or in a demanding automotive assembly line, how is the exact presence of a metal car part confirmed before welding begins? Often, the unsung hero enabling this reliable, non-contact detection is the cylindrical proximity sensor. These ubiquitous, tube-shaped sensors form a critical layer of sensing technology, providing robust and dependable object detection without physical touch in countless industrial and manufacturing environments.
Understanding the Core Principle: Non-Contact Object Detection
At its essence, a proximity sensor detects the presence or absence of an object within a specific range without requiring physical contact. Cylindrical proximity sensors achieve this primarily through either inductive or, less commonly, capacitive sensing principles.
- Inductive Sensors: The predominant technology in cylindrical housings. These generate an oscillating electromagnetic field from the sensor’s face. When a metallic object enters this field, it induces small electrical currents (eddy currents) within the object, absorbing energy from the sensor’s field. This energy loss causes a measurable change in the sensor’s oscillation – its amplitude or frequency – which is processed internally. Once the change exceeds a predefined threshold, the sensor’s internal electronic switch changes state (e.g., from OFF to ON or vice-versa).
- Capacitive Sensors: These generate an electrostatic field. The presence of any object (metal, plastic, wood, liquid) within this field alters its capacitance. This change is detected, triggering the sensor’s output. While available in cylindrical form, inductive sensors are far more common due to their specific suitability for metal detection. Cylindrical proximity sensors are overwhelmingly inductive devices.
Why Cylindrical? The Advantages of the Classic Design
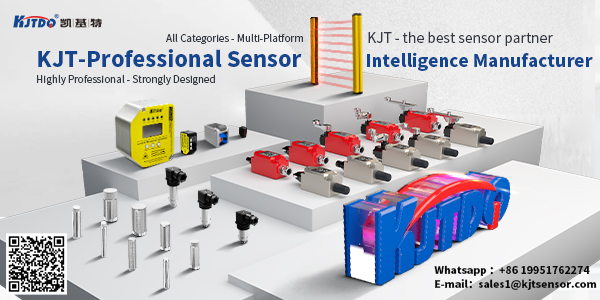
The cylindrical form factor, typically made of robust materials like nickel-plated brass or stainless steel, isn’t arbitrary. It offers several significant advantages:
- Robustness and Durability: The thick metal housing provides exceptional physical protection against impact, crushing forces, and vibration – common hazards in industrial settings. They are built to withstand demanding environments.
- Environmental Protection: Cylindrical sensors are renowned for their high sealing standards, easily achieving ratings like IP67, IP68, or IP69K. This makes them resistant to dust ingress, high-pressure water jets, cleaning chemicals, oils, and coolants, essential for washdown areas or dirty workshops.
- Heat Dissipation: Metal housings efficiently dissipate heat generated by internal electronics, contributing to stable operation and longer lifespan.
- Standardized Installation: Their shape allows for easy and secure mounting using standard nuts. They can be smoothly inserted into precisely drilled holes on machine frames, brackets, or fixtures. Options for flush mounting (where the sensor face is level with the mounting surface) or non-flush mounting (where the sensor protrudes) provide flexibility depending on application needs and available space.
- Reliable Sensing: The contained design helps focus the electromagnetic field, providing consistent and repeatable detection ranges and minimizing false triggers. The switching frequency – how quickly they can detect objects passing by – is crucial for high-speed applications, and cylindrical inductive sensors typically offer excellent performance here.
Key Performance Parameters: What to Consider
Selecting the right cylindrical proximity sensor involves understanding several critical specifications:
- Sensing Range: The maximum distance at which the sensor can reliably detect its target material. This is nominal and can be influenced by target size, shape, and material properties.
- Target Material: Crucially, inductive sensors detect ferrous metals (like iron, steel) at their longest nominal range. Non-ferrous metals (like aluminum, brass) and stainless steel usually have significantly shorter sensing ranges. Capacitive sensors detect a wider range of materials.
- Output Configuration: This defines how the sensor signals detection:
- NPN vs. PNP: Refers to the transistor type used for switching the load (e.g., PLC input, relay). PNP (sourcing) is more common in Europe/Asia, NPN (sinking) in North America, though both are globally available.
- NO (Normally Open) vs. NC (Normally Closed): Describes the output state when no target is present (NO = open circuit, NC = closed circuit). Output changes state upon detection.
- Operating Voltage: The DC voltage range (commonly 10-30V DC) required to power the sensor.
- Connection Type: Options include pre-wired cables (2m or 5m common), or quick-disconnect (QD) connectors (M8 and M12 sizes are industry standard).
- Switching Frequency: How fast the sensor can react to targets passing by, measured in Hertz (Hz). Critical for high-speed counting or positioning.
- Hystereses: The difference between the switch-on point (when the target approaches) and the switch-off point (when the target moves away). This prevents output chattering if the target lingers near the sensing threshold.
- Environmental Rating (IP Code): Essential for ensuring suitability for the application’s environmental conditions.
Ubiquitous Applications: Where Cylindrical Proximity Sensors Shine
The combination of robustness, reliability, and non-contact operation makes cylindrical inductive proximity sensors indispensable across numerous sectors:
- Factory Automation & Machinery: Position verification of parts, end-of-travel detection for cylinders or slides, presence detection for machining processes, object counting on conveyors, rotational speed monitoring.
- Material Handling & Packaging: Bottle/can presence on fillers and cappers, carton detection, palletizing position control, level detection in bins/hoppers (using capacitive variants).
- Automotive Manufacturing: Detecting metal components on assembly lines, verifying robot tool positions, confirming part presence before welding or assembly, door/payload detection.
- Food & Beverage Processing: Monitoring presence of metal lids, tools, or containers (using hygienic stainless steel variants with appropriate IP69K ratings for washdown).
- Machine Tools: Tool position verification, spindle orientation, chuck open/close confirmation, coolant level monitoring.
Installation Best Practices: Ensuring Optimal Performance
Correct installation is paramount for reliable detection and longevity:
- Mount Securely: Use the supplied mounting nuts to ensure the sensor is tightly fixed and vibration-resistant.
- Consider Mounting Style: Choose flush mounting where possible if the surrounding material is metal, as it minimizes side interference. Non-flush mounting offers a longer sensing range but requires sufficient clearance around the sensor face.
- Respect Sensing Range: Ensure targets reliably enter the sensor’s specified detection zone. Account for material type!
- Check Clearance: Maintain adequate space around the sensor (especially non-flush types) to prevent false triggering by adjacent metal objects. Refer to manufacturer specs for minimum clearance distances.
- Mind the Environment: Ensure the sensor’s IP rating is suitable for the ambient conditions (dust, moisture, chemicals, temperature).
- Verify Wiring: Double-check connections (Supply+, Supply-, Output) according to the sensor’s datasheet and the connected controller (PLC input module compatibility with PNP/NPN).
- Avoid Over-Tightening: While secure mounting is vital, excessive force on the housing or threads can damage the sensor.
From the relentless pace of automotive assembly lines to the precise demands of pharmaceutical packaging, cylindrical proximity sensors serve as the dependable workhorse of industrial sensing. Their robust metallic enclosure shields sophisticated inductive electronics, allowing them to deliver critical non-contact detection in environments where lesser sensors would fail