omron prox sensor
- time:2025-07-05 00:06:07
- Click:0
OMRON Proximity Sensors: Precision & Reliability for Industrial Automation
In the intricate dance of modern manufacturing and automation, countless components work unseen, ensuring smooth operation and product quality. Among these silent performers, OMRON proximity sensors stand out as fundamental building blocks. These ingenious devices, operating without physical contact, provide the essential “eyes” for machines, detecting the presence or absence of objects with remarkable accuracy and speed. Understanding their capabilities is crucial for optimizing efficiency, enhancing safety, and achieving the high levels of reliability demanded in today’s industrial landscape.
So, what exactly is an OMRON proximity sensor? At its core, it’s a non-contact switching device. It detects the presence of a metallic (typically ferrous) or sometimes non-metallic target within its sensing range – without needing to touch it. This non-contact nature is a game-changer:
- Eliminates Wear and Tear: No physical impact means significantly reduced mechanical failure and vastly extended service life.
- Enables High-Speed Detection: Capable of detecting objects moving at high velocities, far exceeding the capabilities of mechanical switches.
- Works in Harsh Environments: Immune to issues like dust, oil, vibration, and moisture (depending on IP rating) that plague contact-based solutions. OMRON offers sensors with exceptional IP67, IP68, and even IP69K ratings for demanding conditions.
- Consistent Performance: Provides highly repeatable and reliable detection, critical for precision automation.
How OMRON Proximity Sensors Work: The Core Principles
The most common type is the inductive proximity sensor, OMRON’s flagship technology for detecting metal objects. Here’s a simplified breakdown of its operation:
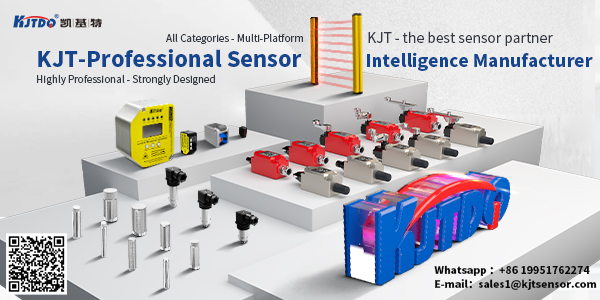
- Generating the Field: An internal oscillator circuit generates a high-frequency alternating electromagnetic field emanating from the sensor’s active face.
- Target Disturbance: When a conductive metal target enters this electromagnetic field, eddy currents are induced on the surface of the target.
- Damping Effect: These eddy currents draw energy from the oscillator circuit, effectively “damping” its oscillation amplitude.
- Signal Processing & Output: An internal threshold circuit monitors the oscillator state. When the damping exceeds a pre-set level (indicating a target is sufficiently close), the sensor triggers its solid-state output switch (usually NPN or PNP transistors). This switches the connected load (like a PLC input, relay, or indicator light) ON or OFF.
Beyond standard inductive sensors, OMRON provides specialized variants:
- All-Metal Detection Sensors: Tuned to reliably detect non-ferrous metals like aluminum and copper.
- Factor 1 Sensors: Feature uniform sensing distance regardless of the target material (ferrous or non-ferrous).
- DC 3-Wire Sensors: Offer enhanced noise immunity and longer wiring capabilities compared to their 2-wire counterparts.
Why Choose OMRON? Hallmarks of Excellence
OMRON didn’t become a global leader in factory automation by accident. Their proximity sensors consistently deliver due to several key advantages:
- Uncompromising Reliability & Longevity: Engineered for millions of operations in tough industrial settings. Robust housings, high-quality internal components, and rigorous manufacturing standards ensure minimal downtime.
- Outstanding Precision & Repeatability: Tight tolerances guarantee that the sensing distance is consistent and reliable, even for high-precision positioning tasks. This accuracy is vital for processes demanding exact registration.
- Superior Environmental Resistance: As mentioned, OMRON sensors excel in challenging conditions. Whether facing cutting fluids, welding sparks, extreme temperatures, or powerful washdowns, specific series are built to endure. IP ratings are clearly specified, allowing for confident selection.
- Broad Range of Models & Configurations: OMRON offers an incredibly diverse portfolio. You’ll find sensors in various cylindrical (M8, M12, M18, M30) and block (rectangular) styles, shielded or unshielded, with diverse connection types (pre-wired, quick-disconnect), and output configurations (NPN/NO/NC, PNP/NO/NC). This ensures the perfect sensor exists for virtually any mounting constraint or electrical requirement within your control panel or machine.
- Advanced Features: Many modern OMRON sensors incorporate features like:
- Short-Circuit Protection: Safeguards the sensor and circuit from wiring errors.
- Surge Protection: Guards against voltage spikes common in industrial environments.
- Reverse Polarity Protection: Prevents damage if power wires are accidentally reversed.
- Diagnostic LEDs: Visible status indicators simplify installation and troubleshooting.
- IO-Link Capability: Enables advanced communication for sensor data monitoring, parameter configuration, and predictive maintenance in Industry 4.0 setups.
- Global Support & Availability: OMRON’s extensive distribution network ensures ready availability and reliable technical support worldwide. Industry-standard mounting simplifies replacement and sourcing.
Key Applications Across Industries
The versatility of OMRON proximity sensors makes them ubiquitous:
- Position Verification: Confirming parts are present on pallets, fixtures, or conveyors. Essential for reliable production line sequencing.
- End-of-Travel Detection: Limiting movement of cylinders, slides, or actuators. Critical for machine safety and preventing damage.
- Count Objects: Tracking products, bottles, or components moving past a point.
- Speed Monitoring: Sensing gear teeth or shaft rotation for RPM calculation.
- Level Control: Detecting the presence of material in tanks or hoppers (when using special float targets).
- Machine Tooling: Tool break detection, turret indexing, spindle orientation.
- Packaging Machinery: Film presence, carton flap position, lid closure detection.
- Material Handling: Pallet presence, gate position, conveyor jam detection.
- Robotics: End-effector position, workpiece presence, safety zone monitoring.
Selecting the Right OMRON Sensor: Key Considerations
To maximize performance, consider these factors:
- Target Material: Is it ferrous (iron/steel), non-ferrous (aluminum, brass, copper), or something else? This defines whether you need a standard inductive sensor or an all-metal/factor 1 type. Some OMRON series detect specific non-metals using capacitive technology.
- Required Sensing Distance: How far away does the sensor need to detect the target? Ensure the nominal sensing distance (Sn) of the chosen sensor meets or exceeds your application needs, factoring in any necessary safety margin. Remember shielded sensors have a shorter range than unshielded ones but allow flush mounting.
- Operating Environment: Temperature range, presence of chemicals, oils, coolants, dust, water, or potential physical impact? Choose the appropriate housing material (stainless steel often recommended for harsh environments) and IP rating.
- Electrical Requirements: Supply voltage (DC 10-30V is common), required output type (NPN sinking, PNP sourcing), load current, and wiring configuration (2-wire, 3-wire, quick-disconnect).
- Mounting Constraints: Available space dictates the sensor size (M8, M12, block style) and whether shielded (flush mountable) or unshielded is needed.
- Special Features: Is short-circuit protection crucial? Need IO-Link for smart connectivity? Require high resistance to welding fields?
Choosing OMRON proximity sensors translates directly into enhanced productivity, reduced maintenance costs, and improved system uptime. Their reputation for delivering consistent, high-performance detection under demanding industrial conditions makes them an intelligent, reliable choice for designing and maintaining efficient automation systems. From simple presence checks to complex positioning tasks, OMRON provides the robust, precise sensing solution required to keep your operations running smoothly and reliably, day in and day out.