4mm proximity sensor
- time:2025-07-04 02:06:42
- Click:0
Unlocking Precision Detection: The Critical Role of 4mm Proximity Sensors
Introduction:
In the intricate dance of modern automation, where machines execute tasks with superhuman speed and accuracy, reliable sensing is the unsung hero. Detecting the presence, absence, or position of objects – often without physical contact – is fundamental to efficiency and safety. Amidst the diverse range of proximity sensors available, those with a 4mm sensing range have carved out a uniquely vital niche. They represent a powerful equilibrium, offering an ideal blend of precision, compactness, and versatility that makes them indispensable across countless industrial and embedded applications. Understanding why the 4mm proximity sensor is such a crucial component unlocks insights into optimized automation design.
How Proximity Sensors Work (The Core Principle)
Before diving into the specifics of the 4mm range, it’s essential to grasp the underlying technology. Proximity sensors, fundamentally, are devices that detect the presence of a nearby object without requiring physical contact.
- Inductive Proximity Sensors: The most common type for detecting metal objects. They generate an electromagnetic field. When a metallic target enters this field, it induces eddy currents within the metal, causing a detectable change in the sensor’s own electromagnetic oscillation. The sensor interprets this change as a detection event. Their key advantage is robustness – impervious to dust, oil, and many harsh environmental factors.
- Capacitive Proximity Sensors: These generate an electrostatic field. Any object (metal, plastic, wood, liquid, etc.) entering this field alters its capacitance. The sensor detects this change. While more versatile regarding target material, they can be more susceptible to environmental influences like moisture or accumulated grime compared to inductive models.
- Other Types: While inductive and capacitive dominate the market for general proximity detection, technologies like photoelectric (light beams), ultrasonic (sound waves), and Hall Effect (magnetic fields) also exist, each suited to specific scenarios, but the core non-contact principle remains.
Why 4mm? The Sweet Spot for Sensing Distance
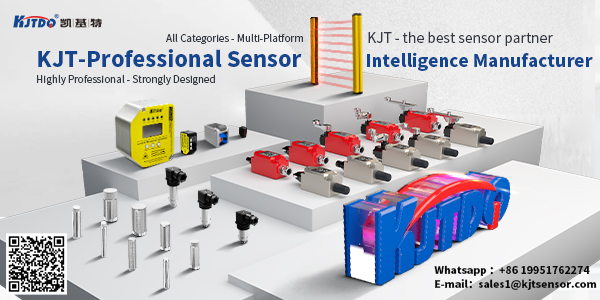
Sensing range is a defining characteristic of any proximity switch. So why has the 4mm proximity sensor become so prevalent?
- Optimal Precision vs. Practicality: Shorter ranges (e.g., 1-2mm) demand extremely precise mounting and alignment, increasing installation complexity and potential for failure. Longer ranges (e.g., 10-30mm) offer more mounting flexibility but can lead to less precise position detection and potentially false triggers from unintended objects in the broader detection zone. 4mm strikes the perfect balance. It provides sufficient distance to accommodate typical mounting tolerances and target approach angles while maintaining excellent positional accuracy. This precision is crucial for tasks like verifying part placement, detecting end-of-travel positions, or counting objects on a conveyor.
- Compact Design: Achieving a reliable 4mm sensing range allows manufacturers to create remarkably compact sensors. This miniaturization is critical for modern machinery where space is at an absolute premium. A 4mm sensor can be installed in tight confines where larger sensors simply wouldn’t fit – inside robotic grippers, on compact assembly modules, or within intricate tooling. Small size doesn’t equate to fragility; many robust 4mm sensors are rated for demanding industrial environments.
- Versatility in Application: The 4mm distance is highly practical for a vast array of common tasks. Whether it’s:
- Verifying the presence of a small component on a PCB assembly line.
- Detecting the position of a pneumatic cylinder piston.
- Confirming metal gear teeth rotation for speed monitoring.
- Sensing the closed position of a small door or guard.
- Counting metallic objects passing on a tight-spaced conveyor.
The 4mm sensing range proves consistently effective and reliable.
- Cost-Effectiveness: Due to their high volume production and standardized design, 4mm proximity sensors generally offer an excellent price-to-performance ratio. They deliver reliable detection capabilities at a cost point that makes automation feasible even for numerous smaller-scale applications.
Common Applications: Where 4mm Sensors Shine
The utility of the 4mm proximity sensor spans numerous industries:
- Factory Automation & Robotics: End-effector tooling verification, part positioning, gripper confirmation, safety interlocks on robotic cells, conveyor jam detection, small actuator position feedback.
- Machine Tools: Tool presence/absence detection in spindles or tool changers, chuck jaw position sensing, coolant level detection (capacitive), guarding position monitoring.
- Packaging Machinery: Detecting small metal components (caps, lids), verifying pouch sealing jaws are closed, monitoring filler valve positions.
- Automotive Manufacturing: Verifying small bracket placement, detecting pistons or valves in sub-assemblies, sensor positioning within tight engine compartments.
- Consumer Electronics Assembly: PCB component presence detection, verifying connector insertion, actuator feedback in miniature mechanisms.
- Material Handling: Position detection for compact linear actuators, verifying pallet presence in constrained spaces, counting small metallic parts.
- Embedded Systems: Integrating into custom machinery, lab equipment, security devices, and consumer products requiring reliable non-contact detection.
Choosing the Right 4mm Sensor: Key Considerations
Selecting the ideal 4mm proximity sensor involves more than just the sensing distance. Key factors include:
- Sensing Technology: Inductive (metal targets only) or Capacitive (metal & non-metal targets)? This is the primary decision.
- Housing Material & Shape: Common options include robust nickel-plated brass, rugged stainless steel (particularly for washdown or corrosive environments), or engineering plastics. Shapes range from cylindrical (M5, M8, M12, M18 diameters are very common) to rectangular block designs. The M8 sensor body is frequently used for 4mm inductive types, offering a good size compromise.
- Electrical Output: NPN or PNP? Normally Open (NO) or Normally Closed (NC)? This must match the input requirements of your controller (PLC, microcontroller, etc.). PNP sourcing outputs are often preferred for standard PLC inputs. Solid-state (transistor) outputs are standard for fast switching speeds and long life.
- Operating Voltage: Typically available in wide DC ranges (e.g., 10-30 VDC) or AC variants. Ensure compatibility with your power supply.
- Environmental Ratings: Consider IP (Ingress Protection) rating (e.g., IP67 for protection against dust and temporary water immersion) and operating temperature range, especially for harsh environments. Look for rugged sensors designed for factory-floor resilience.
- Flush or Non-Flush Mounting: Inductive sensors come in “shielded” (flush mountable) or “non-shielded” types. Shielded sensors allow flush installation in metal without affecting detection range, crucial in tight spaces. Non-shielded sensors offer slightly longer range but require clearance around the sensing face. Most compact 4mm sensors are shielded.
- Response Frequency: How fast can the sensor switch? Important for high-speed counting or detecting rapidly moving targets.
Advantages of 4mm Proximity Sensors
- Non-Contact Operation: Eliminates wear and tear from physical switches, ensuring long service life.
- High Reliability & Speed: Solid-state outputs provide millions of operations and fast switching times (often kHz range).
- Robustness: Particularly inductive versions excel in dirty, oily, dusty, or humid environments where other sensors fail.
- Positional Accuracy: The 4mm range enables precise detection critical for automation sequencing.
- Compact Size: Enables installation in space-restricted locations.
- Versatility: Applicable to a vast array of targets and scenarios.
- Simple Installation & Long Life: Easy to mount and integrate, requiring minimal maintenance.
Looking Ahead: The Future of Compact Sensing
The demand for 4mm proximity sensors remains strong, driven by the relentless pursuit of miniaturization and efficiency. Future trends likely involve:
- Increased Integration: Combining proximity sensing with other functions, like IO-Link connectivity for advanced diagnostics, parameterization, and process data integration.
- Enhanced Materials: Developing even more chemically resistant and higher-temperature tolerant housings.
- Smarter Diagnostics: Embedded intelligence to predict maintenance needs or signal degradation