inductive sensor m12
- time:2025-07-04 01:24:32
- Click:0
The M12 Inductive Sensor: The Tiny Titan Powering Precision Automation
Ever wonder how packaging lines count cans at blinding speed, how robotic arms precisely locate metal parts, or how CNC tools avoid catastrophic collisions? Often, the unsung hero enabling this reliability is a remarkably compact device: the M12 inductive sensor. These miniature proximity sensors serve as the fundamental “eyes” for countless metal detection tasks in demanding industrial environments. Understanding their workings and advantages is key to unlocking efficient and robust automation solutions. Let’s explore what makes M12 inductive proximity sensors such indispensable components in modern manufacturing.
Demystifying the Core Technology: Sensing Without Touch
At its heart, an inductive proximity sensor operates on fundamental principles of electromagnetic induction. The sensor contains an internal oscillating circuit generating a high-frequency electromagnetic field emanating from its active face. When a conductive metal target (like steel, aluminum, brass, or copper) enters this detection field, it disrupts the field’s flow. This disturbance causes tiny eddy currents to form within the metal object itself. The sensor’s sophisticated electronics constantly monitor the strength of its internal oscillator. These induced eddy currents sap energy from the oscillator, weakening its signal. The sensor detects this specific drop in amplitude, triggering its internal solid-state switch. This seamless, non-contact process results in a clean digital output signal (ON/OFF), reliably indicating the presence or absence of the target metal.
Why “M12” Matters: The Power of Standardization
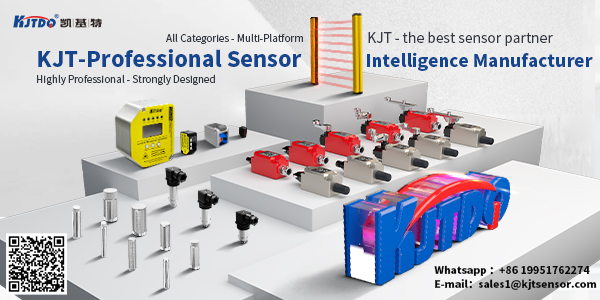
The “M12” designation refers specifically to the sensor’s threaded barrel housing diameter. An M12 sensor has a cylindrical body measuring 12 millimeters in diameter with an external thread conforming to ISO standards. This standardization delivers critical advantages:
- Compact Size: The small M12 form factor allows installation in incredibly tight spaces where larger sensors simply wouldn’t fit, enabling dense packaging of components on machinery.
- Ease of Installation & Replacement: The ubiquitous M12 threaded housing simplifies mounting using standard locknuts. Their prevalence means replacements are readily available, minimizing downtime.
- Robustness and Protection: Designed for harsh industrial environments, quality M12 inductive sensors typically achieve high IP (Ingress Protection) ratings, commonly IP67 or even IP68/IP69K. This signifies excellent resistance to dust, water jets, washdowns, oils, and coolants. The rugged M12 metal or PBT plastic housing provides physical resilience against vibration and minor impacts.
- Connection Simplicity: M12 sensors predominantly feature integrated quick-disconnect M12 connector cables. These plug-and-play connectors drastically simplify wiring, reduce connection errors, and speed up installation and maintenance compared to hard-wired alternatives.
Where M12 Inductive Sensors Shine: Core Applications
The versatility and robustness of M12 inductive proximity switches make them ubiquitous across diverse industries:
- Position Detection: Verifying the presence or absence of metal parts on conveyors, slides, chutes, or at specific machine stations. Crucial for verifying part positioning before a process begins.
- Object Counting: Accurately counting metal objects like cans, bottles (via metal caps), automotive components, or machined parts moving along a production line.
- Jog/Overstroke Prevention: Safeguarding actuators and cylinders by detecting their end positions. Prevents mechanical damage from over-travel.
- Rotational Speed Monitoring: Detecting gear teeth, keyways, or bolts on rotating shafts to calculate RPM or provide feedback on motion.
- Machine Safety: Contributing to safety systems by confirming guards are closed or detecting forbidden metal objects entering dangerous zones.
- Level Control: Detecting metal floats in tanks or confirming the presence of metal bins/silos.
Navigating Selection: Key Parameters for M12 Inductive Sensors
Choosing the right M12 inductive sensor involves more than just size. Consider these vital parameters:
- Sensing Range (Sn): The nominal sensing distance for a specific target size (usually mild steel). M12 inductive sensors typically offer standard sensing ranges between 1mm to 4mm (e.g., 2mm, 4mm). Ensure your target consistently enters this detection zone.
- Target Material: Sensors are calibrated primarily for steel. Other metals like aluminum or brass induce weaker eddy currents, significantly reducing the effective sensing range. Always check the sensor’s data sheet for reduction factors.
- Output Configuration: Select the electronic switching type needed for your control system:
- PNP (Sourcing): Switches the positive (+) supply voltage to the output when activated. Predominantly used in Europe and PLCs/SDCs.
- NPN (Sinking): Switches the negative (-) supply voltage (ground) to the output when activated. Common in Asia and often used with programmable controllers.
- NO (Normally Open) / NC (Normally Closed): Defines the output state when no target is present. NO remains off until detection; NC remains on until detection.
- Operating Voltage: Most M12 inductive sensors operate on DC voltages, commonly 10-30V DC. Some AC/DC universal versions exist.
- Surrounding Material: Avoid mounting flush with or embedding sensors in ferrous metal (iron, steel) without specific provision. This material can dampen the sensing field, drastically reducing range. Non-ferrous metals like aluminum create less interference but still require careful mounting distance as specified in the manual.
- Environmental Needs: For extreme washdown (food/beverage/pharma), select sensors with stainless steel housings (V4A/AISI 316L) and IP69K ratings. High-temperature environments demand sensors rated for continuous operation at temperatures exceeding the standard 70-80°C limit.
- Shielding: Shielded M12 inductive sensors concentrate their field towards the front face, minimizing side interference and allowing flush mounting in metal. Unshielded sensors offer slightly longer ranges but require a non-ferrous mounting zone around them.
Maintaining Peak Performance: Installation & Care
Maximizing the lifespan and reliability of your M12 proximity sensors involves attention to detail:
- Secure Mounting: Use the appropriate M12 locknut and ensure a tight, vibration-resistant fit. Avoid stressing the cable.
- Respect Sensing Distances: Maintain the specified gap between the sensor face and the target. Account for any reduction factors if using non-steel targets.
- Electrical Protection: Implement suppression diodes or suppressors when switching inductive loads (relays, solenoids) to protect the sensor’s internal electronics from voltage spikes.
- Cleanliness: Regularly wipe the sensor face free of metal chips, dirt, oil, or grime buildup, especially in machining environments. Debris can reduce the effective sensing range.
- Environmental Guarding: Ensure the sensor’s IP rating is suitable for its specific location (e.g., splash zone vs. submerged). Regularly check cable jackets and connectors for damage.
The Unseen Engine: Driving Efficiency and Reliability
From the precise assembly of intricate electronics to the relentless pace of automotive production lines, the M12 inductive sensor operates tirelessly behind the scenes. Its combination of **robust M12 threaded construction