atex proximity sensor
- time:2025-07-03 02:00:40
- Click:0
ATEX Proximity Sensors: Safeguarding Operations in Explosive Atmospheres
Imagine a flour mill, its air thick with combustible dust. Or a chemical plant processing volatile solvents. Or an offshore oil rig where flammable gases are ever-present. In these critical environments, standard sensors aren’t just inadequate; they can be the spark that ignites catastrophe. This is where the specialized world of ATEX proximity sensors becomes not just a technical requirement, but a fundamental pillar of operational safety and continuity.
Understanding the Hazard: Why Standard Sensors Fall Short
Standard proximity sensors detect the presence or absence of objects without physical contact, typically using electromagnetic fields (inductive sensors for metals) or capacitance changes (capacitive sensors for various materials). However, in environments with potentially explosive atmospheres – containing flammable gases, vapours, mists, or dusts – the inherent risk lies in the sensor itself. A minor electrical fault, a tiny spark, or even excessive surface temperature generated during normal operation could trigger a devastating explosion. Standard sensors lack the design features to prevent this.
The ATEX Directive: The European Safety Mandate
ATEX derives its name from the French “ATmosphères EXplosibles.” The ATEX directive (specifically Directive 2014/34/EU) is a set of mandatory regulations within the European Union governing equipment and protective systems intended for use in potentially explosive atmospheres. Its primary goal is ensuring a high level of protection for the health and safety of workers and facilities.
For proximity sensors, this means they must be specifically designed, certified, and marked to guarantee they will not ignite the surrounding explosive atmosphere. Compliance is not optional; it’s a legal requirement for operating within the EU in hazardous zones. Similar international standards exist, most notably IECEx (International Electrotechnical Commission System for Certification to Standards Relating to Equipment for Use in Explosive Atmospheres), which provides global recognition.
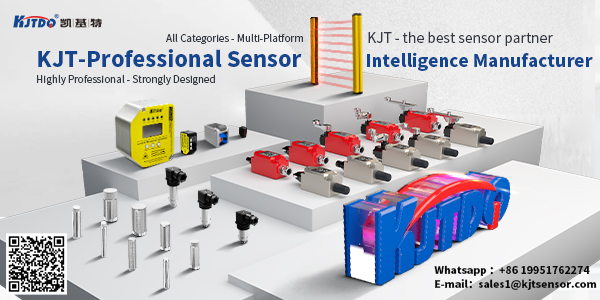
How ATEX Proximity Sensors Mitigate Risk
ATEX-certified proximity sensors incorporate critical design features to eliminate ignition sources:
- Intrinsic Safety (Ex i): This is one of the most common protection concepts for proximity sensors in gas environments. It limits the electrical energy (both for sparks and thermal effects) within the sensor circuits to levels below what is needed to ignite the specific hazardous atmosphere. This involves careful design of circuits, use of barriers, and limiting capacitance and inductance values.
- Flameproof Enclosure (Ex d): This method contains any explosion that might occur within the sensor’s enclosure, preventing it from igniting the external atmosphere. The robust housing withstands internal pressure and cools expelled gases below the ignition temperature of the surrounding atmosphere.
- Increased Safety (Ex e): Focuses on preventing excessive temperatures, sparks, and arcs during normal operation through enhanced constructional measures like improved terminals, creepage distances, and robust enclosures.
- Encapsulation (Ex m): Potentially ignition-capable components are completely sealed in resin to prevent contact with the explosive atmosphere.
- Temperature Rating (T-rating): Crucially, the sensor’s maximum surface temperature, even under fault conditions, must be lower than the ignition temperature of the specific gas, vapour, or dust cloud present in the environment (e.g., T6 rating indicates ≤85°C).
Zones and Categories: Matching the Sensor to the Hazard
Hazardous areas are classified into Zones based on the likelihood and duration of an explosive atmosphere being present:
- Gas Atmospheres:
- Zone 0: Explosive atmosphere present continuously or for long periods.
- Zone 1: Explosive atmosphere likely to occur in normal operation occasionally.
- Zone 2: Explosive atmosphere not likely to occur in normal operation and, if it does, persists only for a short time.
- Dust Atmospheres:
- Zone 20: Combustible dust present continuously or frequently.
- Zone 21: Combustible dust likely in normal operation occasionally.
- Zone 22: Combustible dust not likely in normal operation and, if it occurs, persists only for a short time.
ATEX equipment is classified into Categories corresponding to the level of protection required:
- Category 1: Equipment for use in Zone 0/20. Offers very high protection level.
- Category 2: Equipment for use in Zone 1⁄21. Offers high protection level.
- Category 3: Equipment for use in Zone 2⁄22. Offers normal protection level.
Selecting the Right ATEX Proximity Sensor
Choosing the correct ATEX proximity sensor involves several critical factors beyond sensing range and output type (PNP/NPN, NO/NC):
- Hazard Type: Is the environment gas/vapour/mist (Gas Ex) or dust (Dust Ex)? Or both (dual certification)?
- Zone Classification: What is the specific Zone (0, 1, 2 / 20, 21, 22) where the sensor will be installed?
- Required Category: Does the application require Category 1, 2, or 3 equipment?
- Protection Concept: Which concept (e.g., Ex i, Ex d, Ex e, Ex m) is suitable for the application and environment?
- Temperature Class (T-rating): What is the ignition temperature (T class) of the hazardous substance(s)? The sensor’s T-rating must be lower.
- Gas Group (for Gas Ex): What is the specific group of gas/vapour present (I for mining, IIA, IIB, IIC for surface industries, where IIC is the most volatile)? The sensor must be certified for the applicable group.
- IP Rating: What degree of protection against dust and water ingress is required for the specific location?
- Material Compatibility: Are the sensor’s housing and sensing face materials compatible with chemicals, solvents, or cleaning agents used in the environment?
Applications: Where ATEX Proximity Sensors are Essential
You’ll find these critical sensors safeguarding countless processes:
- Chemical & Pharmaceutical: Monitoring valves, pumps, mixers, tank levels.
- Oil & Gas (Onshore/Offshore): Detecting position on drilling equipment, pipelines, separators, safety systems.
- Paint & Coatings: Monitoring conveyor positions near spray booths or flammable solvents.
- Food & Beverage (e.g., Flour Mills, Sugar Plants): Detecting fill levels, package presence, machine guards in dusty areas.
- Mining: Equipment monitoring where methane (Group I) is present.
- Wastewater Treatment: Monitoring equipment in areas with potentially explosive biogas.
- Grain Handling & Storage: Position sensing on conveyors and silos where dust clouds are prevalent.
Best Practices for Installation and Maintenance
Simply installing an ATEX sensor isn’t enough. Proper practices are vital:
- Strict Adherence to Certification: Never modify or tamper with a certified sensor or its cabling. Use only approved accessories and intrinsic safety barriers if required by the design (Ex i).
- Correct Zoning: Ensure the sensor’s Zone/Category certification precisely matches the area it’s installed in.
- Professional Installation: Installation should be performed by competent personnel familiar with hazardous area regulations.
- Regular Inspection & Maintenance: Follow manufacturer guidelines and regulatory requirements for inspection intervals and procedures. Check for damage, corrosion, and ensure integrity of seals and enclosures.
- Documentation: Maintain clear records of all ATEX equipment, certifications, installation locations (zones), and maintenance history.
ATEX proximity sensors are far more than just a sensor; they are a meticulously engineered safety component. Understanding the principles of hazardous area classification and the rigorous design requirements behind ATEX certification is paramount for engineers, safety managers, and procurement specialists operating in industries where explosive atmospheres are a reality. Selecting, installing, and maintaining the correct ATEX proximity sensor is a critical step in preventing accidents, protecting lives and assets, and