ifm inductive proximity sensor
- time:2025-07-02 01:54:45
- Click:0
IFM Inductive Proximity Sensors: The Silent Sentinels of Industrial Automation
In the unseen corners of modern factories, whirring robots, and intricate assembly lines, silent sentinels tirelessly perform a critical function: detecting the presence or absence of metal objects. Often overlooked yet absolutely fundamental, these guardians are frequently IFM inductive proximity sensors. Far more than simple switches, they are the bedrock of precision, safety, and efficiency in countless automated processes, operating reliably in the harshest industrial environments without ever needing physical contact.
Understanding the Inductive Principle: Seeing Without Touching
At the heart of every IFM inductive proximity sensor lies a fundamental scientific principle: electromagnetic induction. Here’s how these remarkably robust devices operate:
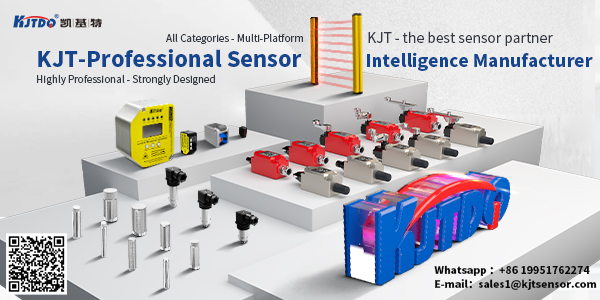
- Generating the Field: The sensor contains an oscillator circuit that generates a high-frequency electromagnetic field emanating from the active face of the sensor.
- The Eddy Current Effect: When a metallic object (the “target”) enters this electromagnetic field, tiny circulating electrical currents, called eddy currents, are induced within the target material.
- Detecting the Change: These eddy currents draw energy from the sensor’s oscillating circuit, causing its amplitude to decrease. Sophisticated electronics within the sensor precisely monitor this amplitude.
- Triggering the Output: Once the amplitude drop reaches a pre-defined threshold (indicating the target is within the effective sensing range), the sensor’s solid-state electronic switch instantly changes state – typically turning a load (like a PLC input) on or off. When the target moves away, the field recovers, and the switch reverts to its original state.
This entire process happens instantaneously and without any physical wear and tear, making inductive sensors exceptionally durable and reliable.
Why IFM Inductive Sensors? A Reputation Built on Performance
IFM has established itself as a global leader in industrial automation sensors, and their inductive proximity range exemplifies this leadership. Choosing an IFM inductive proximity sensor brings distinct advantages:
- Unparalleled Robustness: Engineered for demanding industrial settings, IFM sensors boast exceptional resistance to shock, vibration, dirt, dust, moisture (IP67, IP68, IP69K ratings are common), and even aggressive chemicals. Their hermetically sealed housings, often made from rugged nickel-plated brass or high-grade stainless steel (V4A/AISI 316L), ensure longevity. This resilience minimizes downtime and maintenance costs.
- Precision Sensing: Consistent and accurate detection is paramount. IFM offers sensors with varied sensing ranges, from very short (millimeters) to longer distances, and highly repeatable switching points. Factors like target material (steel, stainless steel, aluminum, brass, etc.), size, and shape are carefully considered in their designs, with specific variants optimized for different metals. High switching frequencies enable tracking of fast-moving objects.
- Diverse Range & Specialization: IFM doesn’t offer a one-size-fits-all solution. Their catalog includes:
- Standard cylindrical sensors (M8, M12, M18, M30): The workhorses for general applications.
- Cubic/Block-style sensors: Offer compact installation where space is tight.
- High-temperature sensors: Built to withstand extreme heat near furnaces or foundries.
- Factor 1 sensors: Detect all metals (steel, stainless steel, aluminum, brass) at the same rated sensing distance.
- Welding-resistant sensors: Feature special protective coatings to withstand spatter and intense electromagnetic interference (EMC) in robotic welding cells.
- Analog output sensors: Provide continuous distance measurement, not just a simple on/off signal.
- IO-Link enabled sensors: Offer advanced diagnostics, remote parameterization, and process data integration for Industry 4.0 readiness. This connectivity transforms simple sensors into intelligent data points.
- Innovation Features: IFM incorporates technologies like ShockAbsorb (enhanced mechanical protection) and AS-Interface compatibility directly into sensor designs, simplifying connectivity and boosting system resilience.
- Global Support & Reliability: Backed by IFM’s extensive global network, technical support, and consistent manufacturing quality, these sensors represent a reliable long-term investment.
Where They Work: Applications Driving Efficiency
The versatility of IFM inductive proximity sensors makes them indispensable across diverse sectors:
- Manufacturing & Machining: Precise positioning of parts on conveyors, pallets, or fixtures; confirming tool presence/changing in CNC machines; detecting end positions of hydraulic/pneumatic cylinders; counting metallic parts. Ensuring the correct sequence of operations.
- Packaging & Material Handling: Detecting tins, cans, foil seals, or metallic components on high-speed lines; confirming box presence for labeling or filling; monitoring conveyor belt sections for jams or position control.
- Automotive & Robotics: Verifying component presence before welding or assembly; detecting robot arm positions; confirming gripper closure on metallic parts; safety guarding for machine access points (often used alongside other safety devices).
- Food & Beverage: Utilizing high-grade stainless steel (V4A/AISI 316L) sensors suitable for washdown environments; detecting stainless steel containers, fill levels in metallic tanks (using appropriate variants), or mixer positions.
- Intralogistics & Warehousing: Monitoring position of metallic racks in AS/RS systems; detecting forklift position; confirming the presence of pallets or metal components on automated guided vehicles (AGVs).
Selecting the Right IFM Sensor: Key Considerations
Choosing the optimal inductive proximity sensor requires careful analysis:
- Application: What exactly needs to be detected? (Presence, absence, position, counting)
- Target Material: Steel, stainless steel, aluminum, brass, copper? (Affects sensing range).
- Target Size & Shape: A small bolt vs. a large metal plate? Shape can influence the effective sensing distance.
- Required Sensing Distance (Sn): How far away does the target need to be reliably detected? Always refer to IFM datasheets for exact specifications based on target. Consider installation tolerances.
- Installation Space & Mounting: Is space constrained? Flush mountable (“shielded/surround”) or non-flush mountable (“non-shielded”)? Shielded sensors have a shorter range but can be mounted flush in metal. Non-shielded offer longer ranges but require a non-metallic surrounding.
- Environmental Conditions: Temperature extremes? Exposure to water, chemicals, welding spatter, or intense vibration/shock? Dictates housing material and IP rating.
- Electrical Requirements: Operating voltage (e.g., 10-30V DC, 20-250V AC/DC), output type (e.g., NPN, PNP, NO, NC), connection type (cable or connector), and special features needed (IO-Link, analog output)? Matching the sensor output to your PLC or controller is critical.
- Special Needs: Analog measurement? High-temperature resistance? Welding application? Factor 1 capability?
**Relentlessly monitoring position, presence, and end points, IF