omron inductive sensor
- time:2025-07-02 01:12:34
- Click:0
Omron Inductive Sensors: The Unsung Heroes of Industrial Automation
Imagine a high-speed production line, robots whirring, conveyor belts humming. Amidst this orchestrated chaos, countless tiny sentinels stand guard. Unseen, often overlooked, they perform millions of operations without fail, ensuring flawless positioning, detecting metal parts with unwavering precision, and safeguarding equipment and processes. These vital components are often Omron Inductive Sensors, the reliable backbone of modern industrial automation.
Inductive proximity sensors, the core type under the Omron inductive sensor umbrella, operate on a fascinating principle. Essentially, they generate an electromagnetic field from a coiled wire within their sensing face. When a metallic target (like steel, aluminum, copper, or brass) enters this field, it induces tiny eddy currents within the target material itself. These eddy currents draw energy from the sensor’s coil, subtly altering the field’s characteristics. The sensor’s sophisticated internal circuitry detects this change and triggers a clean, reliable output signal – switching it ON or OFF. The brilliance lies in its non-contact detection. There’s no physical touch, meaning zero wear and tear on the sensor or the target, leading to exceptionally long operational lifespans measured often in millions of operations.
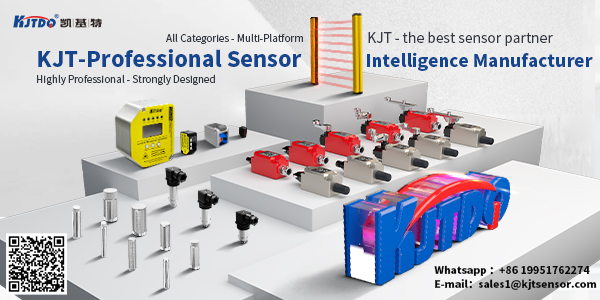
So, why choose Omron specifically within this critical category? The answer lies in a potent combination of engineering excellence and practical design tailored for harsh industrial realities:
- Exceptional Robustness & Reliability: Omron sensors are built like tanks. Encased in durable, often nickel-plated brass or rugged plastics like PBT, they shrug off impacts, vibrations, and the general rough-and-tumble life on the factory floor. This inherent toughness translates directly to minimized downtime and reduced maintenance costs – crucial factors for production efficiency.
- Superior Environmental Resistance: Factories are dirty. Coolant mist, metal shavings, dust, and oil spray are common adversaries. Omron inductive sensors boast impressive IP67 and IP69K ratings, signifying excellent resistance to dust ingress and powerful water jets. This resilience ensures stable operation even in foundries, machine shops, food processing lines (with suitable washdown-rated models), and outdoor applications.
- Temperature Resilience: Industrial environments can swing to extremes. Omron sensors typically operate flawlessly over wide temperature ranges (e.g., -25°C to +70°C standard, with options for even wider extremes), providing consistent performance whether it’s a freezing warehouse or a sweltering foundry.
- Electromagnetic Compatibility (EMC): Modern factories buzz with electromagnetic noise from motors, drives, and welding equipment. Omron rigorously tests its sensors to meet stringent EMC standards (like IEC 61000-6), ensuring stable operation and resistance to interference that could cause false triggering in less robust sensors.
- Detection Precision & Consistency: Omron leverages advanced coil designs and signal processing to deliver highly repeatable switching points. This precision is vital for applications demanding exact positioning, such as verifying the presence of a screw head or precisely stopping a cylinder stroke.
- Intuitive Installation & Versatility: Many Omron inductive sensors feature LED status indicators (visible even from the side on many models), providing instant visual confirmation of power and target detection. They often come in diverse form factors (tubular, rectangular, block), mounting styles (flush, non-flush), and connection types (pre-wired cables, plug connectors like M8/M12), offering enormous flexibility for integration into virtually any machinery setup. Popular series like the E2E, E2A, and E2B encompass thousands of variants catering to almost any specific need.
The applications for Omron inductive sensors are as vast as industry itself:
- Position Verification: Confirming the presence of pistons in cylinders, slides in position, or clamps are closed.
- End-of-Travel Detection: Safely signaling when a moving part (like a robot arm or linear actuator) has reached its limit.
- Object Counting: Detecting metal parts moving past a point on a conveyor for accurate counting and inventory control (e.g., cans, automotive components).
- Speed Monitoring: Counting teeth on rotating metal gears to calculate RPM.
- Level Detection: Sensing the presence or absence of liquid in metal tanks via floats or directly detecting metallic tank interfaces.
- Machine Safeguarding: Acting as vital components within safety circuits (using specifically certified safety sensors) to detect guard door positions or hazardous machine states.
Choosing the right Omron inductive sensor involves considering several key factors:
- Target Material: Ferrous metals (steel, iron) offer the longest sensing distances. Non-ferrous metals (aluminum, brass, copper) have shorter ranges. Omron provides specific sensing distance (Sn) data for both types.
- Required Sensing Distance: How far away from the sensing face does the target need to be reliably detected? Select a sensor with an appropriate nominal sensing distance (Sn), often providing a little headroom.
- Target Size & Shape: Smaller targets require sensors designed for closer detection or featuring factors ensuring reliable sensing with minimal target area.
- Environmental Conditions: Temperature extremes, chemical exposure (coolants, oils, cleaning agents), potential for washdown (requiring IP69K), and presence of metal filings/shrapnel dictate the required housing material and IP rating.
- Mounting Constraints: Physical space limitations determine whether a compact tubular sensor or a rectangular block sensor is needed. Will it be mounted flush with surrounding metal or in a non-flush configuration?
- Electrical Requirements: Voltage supply (commonly 10-30V DC), output type (NPN or PNP transistor switching, normally open/closed), and connection style (cable length/type or connector).
- Special Features: Options include analog output for distance measurement (inductive analog sensors), high-temperature variants, resistance to specific chemicals, or built-in diagnostics.
For those delving into technical specifics, Omron publishes detailed specification sheets (spec sheets) for every sensor model. Understanding parameters like repeatability, response frequency, hysteresis, and voltage drop is essential for ensuring optimal performance in demanding applications. Libraries of 2D and 3D CAD models are readily available to streamline mechanical design integration.
In essence, Omron Inductive Sensors transcend being mere components; they are fundamental enablers of automation. Their robust, reliable, and contactless operation provides the critical feedback loops necessary for machines to “see,” position, count, and react to the metal world around them with speed and precision. While they may operate unseen within the machinery, their contribution to productivity, quality, and safety is profound. When reliability in harsh industrial environments is non-negotiable, specifying Omron is a choice trusted by engineers worldwide, forming the quiet, dependable foundation upon which efficient automation is built.