omron inductive proximity sensor
- time:2025-07-02 00:12:11
- Click:0
The Unseen Guardian: Mastering Detection with Omron Inductive Proximity Sensors
In the pulsating heart of modern industry – on assembly lines weaving intricate products, within robotic arms executing flawless maneuvers, and deep inside machinery humming with relentless power – lies a critical, often unnoticed sentinel. Its task? Reliably, instantly, and without physical touch, detecting the presence or absence of vital metal components. The hero fulfilling this crucial role? The Omron inductive proximity sensor. These rugged, versatile devices are fundamental building blocks of automation, providing the non-contact sensing backbone for countless applications demanding precision and unwavering reliability.
Understanding the Core Principle: The Invisible Field
At the core of every Omron inductive proximity sensor lies a simple yet brilliant electromagnetic principle. Inside the sensor’s robust housing, an oscillator generates a high-frequency alternating magnetic field around its active face. When a conductive metal target – like steel, aluminum, copper, or brass – enters this electromagnetic field, eddy currents are induced within the target material. These eddy currents draw energy from the sensor’s internal oscillator circuit.
The sensor meticulously monitors this energy drain. When it exceeds a specific threshold – precisely when the target comes within the specified sensing distance (Sn) – the sensor’s solid-state electronics trigger an immediate state change in its output signal. This output switch occurs without any physical contact between the sensor and the target, making it immune to wear and tear from mechanical impact. This fundamental non-contact operation is the cornerstone of their reliability and longevity.
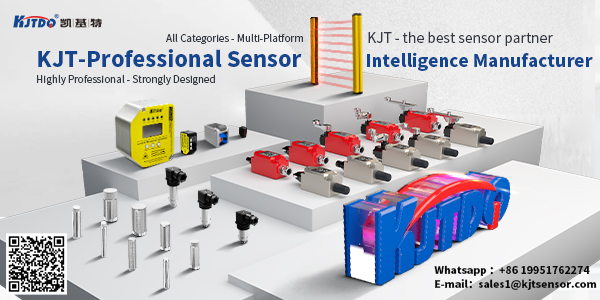
Why Omron Stands Out in the Field
Omron didn’t invent the inductive proximity sensor, but they have relentlessly refined it, becoming a global leader synonymous with quality and innovation. Choosing an Omron inductive sensor means leveraging key advantages purpose-built for demanding industrial environments:
- Legendary Durability: Encased in high-grade PPS or stainless steel and featuring exceptional sealing (often IP67, IP68, IP69K), Omron sensors thrive where others fail. They resist ingress from water, oils, cutting fluids, dust, and chemicals. Extreme shock and vibration? Designed to withstand it.
- Unwavering Performance: Renowned for exceptional repeat accuracy and stable sensing distances, Omron sensors deliver consistent performance shift after shift, critical for high-precision automation where millimetres matter. Their immunity to common environmental interference like dust, oil, and moisture ensures dependable operation.
- Blazing Speed & Versatility: With high-speed response times often measured in microseconds or sub-milliseconds, these sensors keep pace with the fastest production lines and robotic movements. Available in barrel (cylindrical) or block shapes, diverse mounting styles (threaded, bracket), and various output configurations (NPN, PNP, NO, NC, AC/DC), Omron offers a sensor for virtually any position detection, object counting, or end-of-travel sensing task involving metal objects.
- Long Sensing Range: Omron offers models capable of remarkably long detection ranges for their type – often several times their diameter – providing greater flexibility in installation and targeting.
- Shielded vs. Unshielded: Understanding the critical distinction is vital:
- Shielded Sensors (Flush Mountable): Feature a metal ring surrounding the sensing face, focusing the magnetic field axially forward. This allows them to be flush-mounted in metal brackets or panels without affecting performance. Essential for compact installations.
- Unshielded Sensors (Non-Flush Mountable): Lack the front shield, resulting in a larger, more radial magnetic field. They offer a longer sensing distance compared to a shielded counterpart of the same size but must be installed with adequate clearance from surrounding metal.
- Intelligent Features: Modern Omron lines often incorporate advanced features like short-circuit protection, reverse polarity protection, and robust EMC noise immunity, simplifying wiring and enhancing system robustness. Some also offer IO-Link capabilities for digital communication and diagnostics.
Omron Inductive Proximity Sensors: Where They Shine
The application landscape for these sensors is vast, underpinning factory automation and process control across almost every sector:
- Machine Tooling & CNC: Detecting tool presence/absence in holders, confirming workpiece clamping, signalling end-of-axis travel, verifying turret indexing. Position detection ensures machining accuracy.
- Material Handling & Packaging: Counting metallic parts/cans on conveyors, verifying the presence of pallets or containers, detecting metallic caps or seals, confirming the position of grippers or actuators.
- Automotive Assembly: Verifying placement of engine blocks, pistons, transmission components; detecting robotic end-effector position; confirming door or hood closure; sensing metallic fasteners.
- Robotics: Providing precise end-of-arm tooling (EOAT) feedback, verifying part pickup/placement, detecting joint limits, enabling collision avoidance near metal structures.
- Food & Beverage (Metal Can/Equipment Sensing): Monitoring fill levels by detecting metal lids/containers, counting cans/bottles with metal components, verifying position of metallic machinery parts like valves or fillers (where contact is impossible).
- Conveyor Systems: Object detection for sorting, confirming part transfers, triggering sorting gates, detecting jams (via presence of stalled metal parts).
The Tangible Benefits: Efficiency, Reliability, Cost Savings
Integrating Omron inductive proximity sensors translates into measurable operational advantages:
- Zero Contact, Zero Wear: Eliminates the mechanical failure points inherent in limit switches. Dramatically reduces maintenance costs and downtime.
- Supreme Reliability: Consistent operation under harsh conditions (dirt, moisture, vibration) ensures continuous process control and fewer false triggers or missed detections.
- High-Speed Operation: Enables faster machine cycles, increasing throughput and productivity.
- Simplified Design & Installation: Solid-state design with no moving parts simplifies integration. Flush mounting capability saves space. Long cable options offer flexibility.
- Long Service Life: Built for longevity, significantly reducing replacement frequency and total cost of ownership.
- Enhanced Safety: Non-contact sensing inherently provides a level of safety by keeping electronics isolated from moving parts.
Selecting the Right Omron Inductive Sensor
To maximize performance, careful selection based on application requirements is crucial:
- Target Material: Different metals affect sensing distance. Iron (steel) yields the longest range, followed by stainless steel, brass, copper, and aluminum (shortest). Factor in the target’s size and shape.
- Required Sensing Distance (Sn): Choose a model where the sensor’s rated Sn comfortably exceeds the actual installation distance needed, allowing for tolerances and variations.
- Mounting Constraints: Space limitations dictate body shape (barrel vs block). **