inductive proximity sensor
- time:2025-07-01 15:28:42
- Click:0
The Unseen Guardian: How Inductive Proximity Sensors Drive Modern Automation
Imagine a high-speed production line where robotic arms move with blinding speed, assembling components with millimeter precision. One misstep, one undetected metal part out of place, could cause catastrophic damage, halt production for hours, and cost thousands. What invisible sentinel prevents this chaos? More often than not, it’s the humble yet incredibly robust inductive proximity sensor, silently performing millions of critical detections daily, far from the limelight but foundational to industrial efficiency.
Demystifying the Inductive Proximity Sensor
At its core, an inductive proximity sensor is a non-contact electronic device specifically designed to detect the presence or absence of metallic objects within its sensing range – without requiring any physical touch. Unlike mechanical switches prone to wear or optical sensors affected by dust, induction sensors thrive in challenging industrial environments.
The Core Principle: Harnessing Electromagnetic Fields
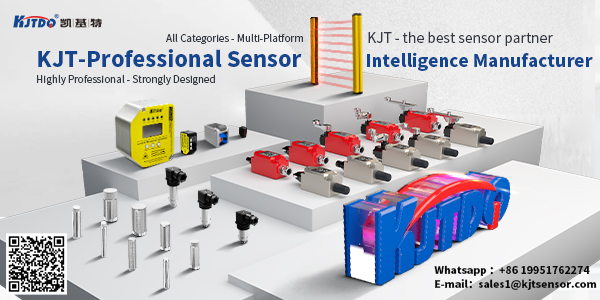
The magic, grounded in Faraday’s Law of Induction, is elegantly simple yet profoundly effective. Here’s the breakdown:
- The Active Element: The sensor’s face contains a coil wound around a ferrite core, forming an inductor. This coil is part of an oscillator circuit.
- Generating the Field: An alternating current passes through the coil, generating a high-frequency oscillating electromagnetic field at the sensor’s active surface.
- The Eddy Current Effect: When a metallic target enters this magnetic field, it acts like the secondary winding of a transformer. Small circulating electrical currents, called eddy currents, are induced within the target object.
- Energy Drain & Detection: The creation of these eddy currents draws energy away from the sensor’s oscillator coil. This energy loss causes a measurable change – typically a reduction in amplitude – in the oscillator’s signal.
- Signal Processing & Output: The sensor’s internal circuitry continuously monitors the oscillator’s amplitude. When the energy loss (and thus amplitude reduction) reaches a predefined threshold (indicating a target is present within the sensing range), the sensor triggers its output signal. This output is commonly a solid-state switch (like an NPN or PNP transistor) opening or closing a circuit, or sometimes an analog signal proportional to distance.
Why Choose Inductive Proximity Sensors? Key Advantages
Their operational principle translates into a suite of compelling advantages, making them ubiquitous in automation:
- Non-Contact Operation: No physical wear occurs between the sensor and the target, ensuring extremely long operational life and eliminating friction-related failures. This is crucial for high-cycle applications.
- Exceptional Robustness & Reliability: Housed in rugged materials like nickel-plated brass or stainless steel, and often potted with resin, these sensors resist shocks, vibrations, moisture, dust, dirt, oil, and coolant splashes. IP67 and IP69K ratings are common.
- High Switching Frequency: Capable of detecting targets moving at high speeds (hundreds or even thousands of times per second), outpacing mechanical switches by orders of magnitude.
- Completely Insensitive to Non-Metals: Ideal for environments with water, plastic chips, wood dust, or oil mist where optical sensors might false-trigger. They only detect metals.
- No Moving Parts: Eliminates a major source of potential failure points, enhancing overall system reliability compared to mechanical limit switches.
- Solid-State Outputs: Provide fast, bounce-free switching signals vital for PLCs (Programmable Logic Controllers) and modern control systems.
- Simple Installation & Use: Typically require only a power connection and output wiring. No complex alignment needed beyond ensuring the target passes within the specified sensing range.
Understanding Critical Specifications
When selecting an inductive sensor, several specifications are paramount:
- Sensing Distance (Sn): The nominal operating distance at which a standard target (usually mild steel) will reliably trigger the sensor under defined conditions. Real-world effective range depends on target material and size.
- Target Material: Different metals induce eddy currents with varying efficiency. Mild steel offers the longest range. Stainless steel, aluminum, brass, and copper have shorter ranges (typically listed as a percentage reduction relative to steel). Non-ferrous metals generally require sensors optimized for them.
- Target Size & Shape: Larger targets are detected more readily than smaller ones. The target must generally be at least equivalent in size to the sensor’s active face diameter for maximum range.
- Hysteresis: The difference between the switch-on point when the target approaches and the switch-off point when it moves away. This prevents chattering when the target is near the detection threshold.
- Output Configuration: NPN (sinking) or PNP (sourcing) transistor outputs, NO (Normally Open) or NC (Normally Closed) logic. Analog outputs (0-10V, 4-20mA) are also available for distance-proportional monitoring.
- Operating Frequency (Switching Frequency): How many times per second the sensor can reliably switch its output on and off.
- Environmental Ratings: IP rating for ingress protection (dust/water), temperature range, resistance to chemicals or welding spatter.
Where Do They Shine? Diverse Applications
The robustness and reliability of inductive proximity sensors make them indispensable across countless industries:
- Manufacturing & Assembly Lines: Position verification of machine parts, robots, clamps, and slides; end-of-travel detection on cylinders; object counting (metal parts on conveyors); presence/absence checking for quality control; monitoring filling levels of metal powders or granules.
- Material Handling & Packaging: Detecting metal rollers, chains, pallets, or the presence of metal containers/caps on conveyors and packaging machinery. Safeguarding access points on automated guided vehicles (AGVs).
- Automotive Industry: Monitoring camshaft/crankshaft position and speed; detecting gears, pistons, and valves during engine assembly; tool positioning on robotic welders; door and hatch open/close status.
- Machine Tools: Tool breakage detection (sensor positioned to detect the tool shank); tool changer position and spindle orientation confirmation; workpiece positioning and clamping verification.
- Food & Beverage Processing: Position detection on stainless steel machinery, even in washdown environments (using specialized high-grade stainless steel sensors); metal detection to prevent contamination; monitoring fill levels in tanks and hoppers.
- Robotics: Providing precise feedback on joint limits, gripper closure (detecting metal components held), and end effector position.
The Unseen Backbone of Industry
From the cars we drive to the packages we receive, inductive proximity sensors play an indispensable, often invisible, role. Their ability to provide reliable, high-speed, non-contact detection of metallic objects in the toughest environments translates directly into increased productivity, enhanced safety, reduced downtime, and lower maintenance costs. Understanding their operating principle – the elegant dance of electromagnetic fields and eddy currents – reveals why they remain a fundamental, trusted technology and a cornerstone of modern industrial automation. As factories continue to push towards greater speed and intelligence, the robust performance of these sensors ensures they will remain vital components on the production floor for the foreseeable future.