allen bradley proximity sensor
- time:2025-07-01 13:28:26
- Click:0
Allen-Bradley Proximity Sensors: Precision Detection for Demanding Industrial Automation
The relentless hum of a modern production line. Robotic arms executing intricate maneuvers. Conveyors seamlessly transporting components. Beneath this orchestrated chaos lies an unsung hero ensuring everything runs smoothly and safely: the proximity sensor. When uncompromising reliability and precision are non-negotiable, Allen-Bradley proximity sensors stand as the trusted cornerstone of industrial sensing solutions.
The Silent Guardians: Understanding Proximity Sensing Fundamentals
At their core, proximity sensors perform a vital, yet invisible function: detecting the presence or absence of an object without physical contact. This non-contact detection offers immense advantages over mechanical switches – reduced wear and tear, faster response times, and immunity to dirt, oil, and harsh environments common in factories.
The most prevalent type is the inductive proximity sensor. These clever devices generate an electromagnetic field. When a metallic object enters this field, it induces eddy currents within the target, causing a detectable change in the sensor’s internal oscillator. This change triggers the sensor’s output switch. Inductive sensors are champions for detecting metals like steel, aluminum, and brass.
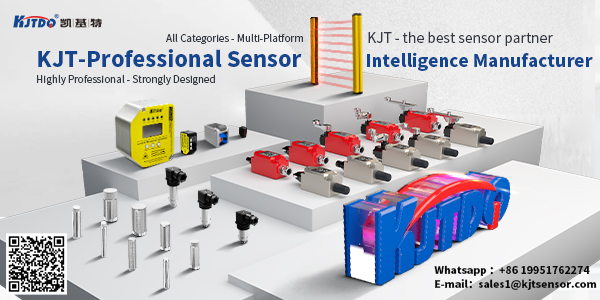
Beyond inductive, capacitive proximity sensors detect both metallic and non-metallic targets (like plastics, liquids, wood, or granules) by sensing changes in capacitance caused by the target object entering an electrostatic field. Magnetic proximity sensors, often called reed switches or solid-state equivalents, specifically detect the presence of permanent magnets, commonly used for position sensing on cylinders.
Why Allen-Bradley Proximity Sensors Command the Field
Allen-Bradley, a flagship brand within Rockwell Automation, has built its reputation on delivering robust, reliable components that industrial engineers can depend on in mission-critical applications. Their proximity sensors embody this legacy:
- Legendary Durability: Engineered to withstand the rigors of industrial life. Expect exceptional resistance to shock, vibration, cutting fluids, coolants, washdowns, and wide temperature fluctuations. Housings are often constructed from rugged nickel-plated brass or high-grade PBT plastic.
- Unwavering Reliability & Precision: Consistent and accurate detection is paramount. Allen-Bradley sensors offer minimal sensing distance drift over time and temperature, ensuring processes run predictably. Their repeatability is exceptional.
- Advanced Features & Smart Capabilities: Beyond basic detection, many models boast enhanced functionality. Think:
- IO-Link Integration: Enables advanced diagnostics (like temperature monitoring, switch count), parameterization, and simplified replacement – a cornerstone of Industrie 4.0.
- Short-Circuit & Overload Protection: Safeguards the sensor and control circuit from wiring faults.
- Enhanced Resistance to Electromagnetic Interference (EMI): Crucial in environments laden with drives, motors, and welders.
- Seamless Logix Integration: For facilities running on Rockwell Automation’s premier Logix Control Platform (including ControlLogix® and CompactLogix®), Allen-Bradley sensors integrate flawlessly. This simplifies configuration, diagnostics, and network visibility within Studio 5000 Logix Designer®.
- Comprehensive Range: Catering to virtually any demand, the portfolio includes:
- Barrel-style sensors (M12, M18, M30)
- Block-style sensors
- High-temperature variants
- Washdown / harsh environment models
- Specialty sensors for unique applications like weld immune or factor 1 variants.
Allen-Bradley Proximity Sensors in Action: Powering Diverse Industries
The versatility of these sensors makes them indispensable across countless sectors:
- Automotive Manufacturing: Precision detection on robotic weld lines, verifying part presence in assembly fixtures (critical for traceability and quality), monitoring spindle position on machining centers.
- Food & Beverage Processing: Counting bottles/cans on high-speed lines, detecting fill levels in tanks (using capacitive sensors), confirming package sealing, ensuring safety guarding on slicing equipment. Hygienic designs and IP69K ratings are vital here.
- Material Handling & Packaging: Detecting pallet presence on conveyors, verifying case sealing, tracking box counts, and ensuring robotic pick-and-place operations locate items accurately.
- Pharmaceutical Production: Sensitive detection of vials, caps, and blister packs within cleanroom environments demanding ultra-reliability.
- Heavy Machinery & Mobile Equipment: Monitoring hydraulic cylinder position, detecting bucket angles, ensuring safety interlocks on access doors are engaged.
Selecting the Right Allen-Bradley Proximity Sensor: Key Considerations
Choosing the optimal sensor isn’t arbitrary. Several factors guide the selection:
- Sensing Technology: Inductive (metal only), Capacitive (metal and non-metal), or Magnetic (for magnets)? Match the target material.
- Sensing Distance: Required nominal range? Consider mounting constraints and ensure adequate margin.
- Environmental Conditions: Temperature extremes? Chemical exposure? Intense washdown (IP67, IP68, IP69K)? High vibration levels? Allen-Bradley offers specific ruggedized models.
- Electrical Requirements: Voltage (12-24V DC, 90-250V AC, AC/DC universal?), Output type (NPN, PNP, NO, NC), Current rating?
- Physical Size & Mounting: Space constraints dictate barrel size (M12, M18, M30) or necessitate a block-style sensor. Consider flush or non-flush mounting capability.
- Connectivity & Intelligence: Does the application benefit from IO-Link for diagnostics and remote configuration? Integration within a Logix architecture?
- Special Requirements: Weld immunity (resistance to spatter and high currents)? High-temperature? Factor 1? High-speed sensing?
Beyond Detection: Investing in Uptime and Peace of Mind
Implementing Allen-Bradley proximity sensors transcends simply installing a component. It’s an investment in the foundational reliability of an automation system. Their proven durability minimizes unplanned downtime. Their accuracy ensures process consistency and product quality. Features like IO-Link unlock predictive maintenance capabilities, shifting from reactive fixes to proactive management.
In the high-stakes environment of modern manufacturing and processing, overlooking the critical role of the proximity sensor is a risk few can afford. Allen-Bradley proximity sensors deliver the robustness, precision, and advanced capabilities demanded by today’s sophisticated automation landscapes. They are the invisible sentinels, working tirelessly to keep operations running smoothly, safely, and efficiently – a testament to engineering excellence designed for the real world.